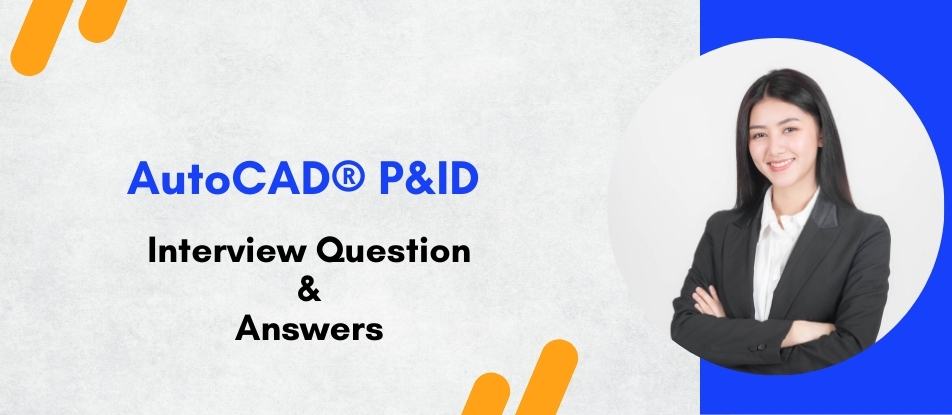
AutoCAD® P&ID Certification Training provides hands-on expertise in designing, modifying, and managing intelligent P&ID schematics. Learn to create standardized diagrams, configure tag formats, validate process flows, and generate reports. This course enhances efficiency, ensures regulatory compliance, and integrates seamlessly with AutoCAD Plant 3D. Ideal for engineers and designers, it empowers professionals with industry-relevant skills for process and plant design certification.
AutoCAD® P&ID Certification Training Interview Questions Answers- For Intermediate
1. What is the purpose of a P&ID drawing in process engineering?
A P&ID drawing serves as a detailed schematic representation of a process system, showing the relationship between equipment, pipelines, instrumentation, and control devices. It provides engineers, operators, and maintenance personnel with a comprehensive visual reference for understanding process flow, safety interlocks, and system functionality. P&IDs are essential for process design, troubleshooting, and compliance with industry regulations.
2. How do you add and manage revision control in AutoCAD P&ID?
Revision control in AutoCAD P&ID is managed through the Project Manager, where users can track drawing changes, assign revision numbers, and maintain a history of modifications. The software allows users to compare versions, highlight differences, and add revision clouds to indicate updates. Proper revision control ensures that all stakeholders work with the latest design and maintain compliance with project documentation standards.
3. What are instrument bubbles, and how are they used in AutoCAD P&ID?
Instrument bubbles are graphical representations of measurement and control devices within a P&ID. They typically include information such as instrument tags, loop numbers, and function identifiers. In AutoCAD P&ID, these symbols can be selected from predefined libraries and linked to process lines or equipment. Properly labeled instrument bubbles ensure accurate communication of process control details and facilitate system automation.
4. How do you create a piping line group in AutoCAD P&ID?
To create a piping line group, select multiple pipeline segments that share common characteristics, such as material, pressure rating, or service type. Using the Line Grouping feature, assign a unique group name and properties, ensuring that all associated segments follow the same specifications. This grouping simplifies pipeline management, improves consistency, and helps in generating accurate reports for procurement and installation.
5. What is the role of process flow arrows in P&ID drawings?
Process flow arrows indicate the direction of fluid, gas, or material movement within a system. They are essential for understanding process behavior and ensuring proper sequencing of operations. In AutoCAD P&ID, flow arrows can be placed on pipelines using predefined symbols, helping engineers and operators quickly interpret system functionality and identify potential issues in the design.
6. How do you modify an existing P&ID component in AutoCAD P&ID?
To modify an existing P&ID component, select the component within the drawing and use the Properties Palette to adjust attributes such as tag number, specifications, and connectivity. Alternatively, the Data Manager allows bulk modifications of multiple components at once. These modifications automatically update across linked reports and databases, ensuring data consistency throughout the project.
7. What is the difference between dynamic and static blocks in AutoCAD P&ID?
Static blocks are standard symbols that remain unchanged once placed in a drawing, while dynamic blocks offer flexibility by allowing adjustments such as rotation, scaling, or parameter modifications. In AutoCAD P&ID, dynamic blocks are commonly used for valves, instrumentation, and other components requiring different orientations or multiple configurations. They enhance design efficiency by reducing the need for multiple symbol variations.
8. How do you check the connectivity of a P&ID drawing?
AutoCAD P&ID provides a Validation Tool that checks for connectivity issues, such as unconnected pipelines, orphaned components, and missing flow arrows. Running a validation report helps detect and resolve errors before finalizing the drawing. Proper connectivity ensures accurate process representation, prevents misinterpretation, and improves the reliability of the design.
9. How can you customize report templates in AutoCAD P&ID?
Report templates in AutoCAD P&ID can be customized using the Report Creator, where users can define data fields, sorting orders, and formatting preferences. Reports such as equipment lists, line schedules, and instrument summaries can be generated based on specific project requirements. Customization ensures that reports align with industry standards and project documentation needs.
10. What is the purpose of assigning process line numbers in a P&ID?
Process line numbers help identify and track pipelines within a P&ID. Each number typically follows a standard format that includes information such as system type, pipe diameter, and service description. Assigning unique line numbers ensures proper referencing in reports, simplifies troubleshooting, and facilitates communication between engineering teams.
11. How does AutoCAD P&ID handle spec-driven design?
AutoCAD P&ID allows users to assign specifications to pipelines and components, ensuring that selected materials, pressure ratings, and sizes align with project requirements. The software provides validation tools to check for compliance with predefined specifications, preventing design errors. This spec-driven approach enhances design accuracy and ensures regulatory compliance.
12. How do you create a new annotation style in AutoCAD P&ID?
To create a new annotation style, access the Project Setup menu and navigate to the Annotation Styles section. Define parameters such as text font, size, color, and alignment to match project standards. Once created, the new style can be applied to all annotations within a project, maintaining consistency across multiple drawings.
13. What are off-page connectors, and why are they important?
Off-page connectors are symbols used to indicate process flow continuity across different P&ID sheets. They link pipelines or signals that span multiple drawings, helping users understand the overall process flow without overcrowding a single sheet. In AutoCAD P&ID, off-page connectors are automatically tracked in the Data Manager, ensuring accurate referencing and documentation.
14. How do you import and export data from AutoCAD P&ID?
AutoCAD P&ID allows importing and exporting data through formats such as Excel, XML, and SQL databases. Users can export component lists, tag information, and report data for external analysis or integration with other engineering tools. Similarly, importing external data enables bulk updates of drawing components, improving workflow efficiency.
15. What is the function of the Validation Report in AutoCAD P&ID?
The Validation Report in AutoCAD P&ID identifies design inconsistencies, such as missing tags, disconnected pipelines, and duplicate components. It provides a structured summary of errors, allowing users to review and correct issues before finalizing the drawing. Using this tool ensures that P&IDs meet quality standards and reduce potential operational issues.
AutoCAD® P&ID Certification Training Interview Questions Answers - For Advanced
1. How do you integrate AutoCAD P&ID with cloud-based project management systems, and what benefits does this offer?
Integrating AutoCAD P&ID with cloud-based project management systems involves linking project files, process data, and documentation with cloud storage solutions such as Autodesk BIM 360, SharePoint, or other document management platforms. This integration allows teams to collaborate in real time, access up-to-date drawings from any location, and track project changes efficiently. The key benefits of cloud integration include improved version control, enhanced collaboration among distributed teams, and reduced data loss due to centralized backups. By leveraging cloud-based systems, organizations can improve project transparency, accelerate decision-making, and streamline workflows, leading to increased productivity and reduced project delays.
2. What are the common challenges in maintaining AutoCAD P&ID projects, and how can they be addressed?
Maintaining AutoCAD P&ID projects presents several challenges, including data inconsistencies, drawing version control, and compliance with changing industry standards. One common issue is the misalignment of process data between different project drawings, which can be mitigated by using the Data Manager to enforce data consistency. Another challenge is managing multiple drawing versions, which can lead to confusion and errors if not properly tracked. Utilizing a document management system or a cloud-based collaboration platform ensures that the latest versions are accessible to all stakeholders. Additionally, regulatory changes may require frequent updates to process designs. Keeping project standards and templates up to date helps address this challenge by ensuring that all new and existing drawings comply with current regulations. Regular training and adherence to best practices can further improve project maintenance and efficiency.
3. How does AutoCAD P&ID support compliance with industry standards such as ANSI/ISA 5.1 and ISO 10628?
AutoCAD P&ID supports compliance with industry standards by providing symbol libraries, tag formats, and documentation tools that align with recognized guidelines such as ANSI/ISA 5.1 for instrumentation and ISO 10628 for process flow diagrams. These standards define the graphical representation, naming conventions, and process documentation rules that must be followed in industrial projects. By adhering to these standards, AutoCAD P&ID ensures that process diagrams are clear, consistent, and easily interpretable by industry professionals. Compliance with these standards is crucial for regulatory approvals, safety assessments, and effective communication across engineering teams.
4. How does AutoCAD P&ID support process optimization, and what role does it play in improving plant efficiency?
AutoCAD P&ID plays a crucial role in process optimization by providing engineers with a clear and organized representation of process workflows, equipment connections, and control instrumentation. By creating accurate and standardized P&ID diagrams, organizations can analyze system layouts, identify bottlenecks, and improve fluid or gas flow efficiencies. The software also enables engineers to conduct validation checks, ensuring all components are properly connected and labeled, reducing operational inefficiencies caused by design flaws. Furthermore, AutoCAD P&ID facilitates integration with process simulation and control software, allowing users to optimize parameters such as pressure, temperature, and flow rates before implementation. This proactive approach leads to reduced downtime, energy savings, and improved overall plant efficiency.
5. What are some best practices for managing large-scale AutoCAD P&ID projects with multiple users?
Managing large-scale AutoCAD P&ID projects with multiple users requires a structured approach to maintain data consistency, workflow efficiency, and version control. One of the best practices is using a centralized database to store project files and component data, ensuring that all team members are working with the latest version of the drawings. Establishing clear user roles and permissions prevents accidental modifications and unauthorized changes. Version control tools, such as Autodesk Vault or cloud-based collaboration platforms, help track changes, maintain revision histories, and ensure that previous versions can be restored if needed. Another best practice is enforcing company-wide P&ID standards, including consistent tag formats, annotation styles, and symbol libraries. Regular team communication and scheduled project audits further enhance coordination and reduce errors.
6. How do you ensure compliance with industry regulations when designing P&IDs in AutoCAD P&ID?
Ensuring compliance with industry regulations in AutoCAD P&ID requires strict adherence to standards such as ANSI/ISA 5.1 for instrumentation, ISO 10628 for process flow diagrams, and OSHA regulations for safety considerations. Compliance begins with using standard P&ID symbols, line notations, and annotation formats as defined by regulatory bodies. AutoCAD P&ID also offers validation tools that help detect missing tags, disconnected components, or incorrect specifications, reducing the risk of non-compliance. Additionally, integrating P&IDs with document control systems ensures that design modifications are properly reviewed, approved, and documented before implementation. Conducting periodic audits and reviews by regulatory experts further ensures that P&ID designs align with industry best practices and legal requirements.
7. What is the significance of pipeline classification in AutoCAD P&ID, and how does it impact design accuracy?
Pipeline classification in AutoCAD P&ID is essential for defining the characteristics of different process pipelines, including material, pressure rating, temperature limits, and service type. Each pipeline in a P&ID is assigned a classification that helps engineers determine the appropriate pipe size, fittings, and insulation requirements. Proper pipeline classification prevents compatibility issues, reduces the risk of failures, and ensures compliance with industry standards such as ASME B31.3 for process piping. In AutoCAD P&ID, pipelines can be tagged and categorized based on predefined specifications, enabling quick identification and accurate documentation in reports and material takeoffs. This systematic approach enhances design accuracy, minimizes rework, and facilitates seamless coordination between engineering, procurement, and construction teams.
8. How does AutoCAD P&ID facilitate collaboration between different engineering disciplines?
AutoCAD P&ID enhances collaboration between different engineering disciplines by providing a common platform for process engineers, mechanical engineers, electrical engineers, and control system designers to work on a unified project. The software allows for seamless integration with AutoCAD Plant 3D, enabling mechanical engineers to develop 3D models while referencing the P&ID for accurate equipment placement. Electrical engineers can use the P&ID to identify instrumentation, control loops, and wiring connections. Additionally, process engineers benefit from real-time data synchronization, ensuring that any changes in the P&ID automatically reflect in related documents and reports. By maintaining a centralized project database, AutoCAD P&ID eliminates discrepancies between disciplines, streamlines workflows, and reduces design conflicts, leading to more efficient project execution.
9. What is the role of intelligent data linking in AutoCAD P&ID, and how does it improve project efficiency?
Intelligent data linking in AutoCAD P&ID allows process components, such as valves, pumps, and instruments, to be associated with real-world specifications, material databases, and control system parameters. This feature ensures that each component in the P&ID carries metadata that can be accessed, updated, and exported for various project needs. For example, linking equipment to an external database enables real-time updates to component specifications without requiring manual edits in multiple drawings. This data-driven approach improves project efficiency by automating reporting, reducing redundancy, and ensuring that all stakeholders have access to up-to-date process information. Additionally, intelligent data linking supports integration with asset management systems, allowing maintenance teams to retrieve operational data directly from P&ID drawings.
10. How do you configure and apply default property settings for new P&ID components in AutoCAD P&ID?
Configuring default property settings in AutoCAD P&ID ensures that newly added components follow predefined standards, reducing manual modifications and maintaining consistency across a project. This setup is done through the Project Setup menu, where users can define default values for attributes such as tag formats, line specifications, and annotation styles. By applying standardized property settings, engineers can automate component placement while ensuring compliance with project specifications. The ability to configure default properties also streamlines workflow efficiency, as designers no longer need to manually adjust each new component’s properties. Additionally, default settings help prevent discrepancies and maintain uniformity in reports, making it easier to manage process documentation.
11. What challenges do engineers face when updating existing P&ID drawings, and how can these be overcome?
Updating existing P&ID drawings presents several challenges, including maintaining data consistency, ensuring version control, and preventing miscommunication between engineering teams. One common issue is discrepancies between updated P&IDs and older versions used by other departments, leading to errors in project execution. This can be overcome by implementing a revision control system, where every update is tracked, documented, and reviewed before approval. Engineers also face challenges in maintaining connectivity when modifying pipelines, valves, or instrumentation. Using AutoCAD P&ID’s validation tool helps detect broken connections, missing tags, or incorrect flow directions. Additionally, clear communication protocols between design, operations, and maintenance teams ensure that updates reflect actual process modifications and are not based on outdated information.
12. How does AutoCAD P&ID support integration with SCADA and DCS systems for automation?
AutoCAD P&ID supports integration with Supervisory Control and Data Acquisition (SCADA) and Distributed Control Systems (DCS) by providing a structured representation of process control elements such as sensors, transmitters, and controllers. Each instrument in the P&ID can be assigned real-world input/output (I/O) parameters that correspond to control system configurations. By exporting P&ID data in XML or database formats, automation engineers can directly import process information into SCADA/DCS systems for programming and real-time monitoring. This integration reduces manual data entry errors, improves process automation accuracy, and enhances overall system efficiency. Additionally, linking P&ID components to SCADA data allows plant operators to visualize process conditions directly from the control interface.
13. What are some key differences between AutoCAD P&ID and traditional 2D CAD drafting for process design?
Unlike traditional 2D CAD drafting, which primarily focuses on manual linework and static drawings, AutoCAD P&ID provides intelligent process diagrams that store metadata, enable validation checks, and automate component tagging. Traditional 2D CAD lacks built-in data management features, making it more error-prone when handling large projects. AutoCAD P&ID also offers predefined symbol libraries for valves, pumps, and instruments, reducing design time compared to manually drafting each component. Another major difference is reporting capability—AutoCAD P&ID automatically generates process data reports, reducing manual data extraction efforts. These features make AutoCAD P&ID a superior choice for process design, improving efficiency, accuracy, and integration with engineering workflows.
14. How does AutoCAD P&ID handle version control, and why is it crucial for process design projects?
Version control in AutoCAD P&ID is essential for tracking design modifications, preventing errors, and ensuring that all stakeholders are working with the latest approved version of a project. The software allows users to manage revisions through project databases, document control systems, or integration with Autodesk Vault, which provides centralized storage and version tracking. Each time a change is made, a new revision can be logged, with notes indicating what was updated, who made the changes, and why the modification was necessary. This systematic approach reduces confusion, prevents rework caused by using outdated drawings, and ensures regulatory compliance by maintaining a clear history of design changes. In large-scale projects, proper version control also enhances collaboration between teams, ensuring that updates to pipelines, equipment, or instrumentation are properly reviewed and approved before implementation.
15. How do you optimize AutoCAD P&ID performance when working with large-scale industrial projects?
Optimizing AutoCAD P&ID performance for large-scale projects involves several best practices, including efficient file management, hardware optimization, and workflow improvements. One of the most effective strategies is breaking down large P&ID drawings into smaller, linked sheets, reducing file size and improving software responsiveness. Using external references (Xrefs) instead of embedding all components within a single file helps distribute the workload across multiple drawings. Additionally, limiting the number of active layers, optimizing annotation styles, and keeping block libraries organized improves performance. From a hardware perspective, ensuring that workstations are equipped with sufficient RAM, a high-performance graphics card, and SSD storage significantly reduces lag when handling complex drawings. Finally, using database cleanup tools and regularly validating P&IDs to remove unused elements prevents data bloat, ensuring smooth project execution even with extensive datasets.
Course Schedule
Apr, 2025 | Weekdays | Mon-Fri | Enquire Now |
Weekend | Sat-Sun | Enquire Now | |
May, 2025 | Weekdays | Mon-Fri | Enquire Now |
Weekend | Sat-Sun | Enquire Now |
Related Courses
Related Articles
- Microsoft SQL Server 2012 Certification Training Benefits
- Unlocking the Potential of Identity Management with SailPoint Training at Multisoft Virtual Academy
- Top 10 Questions with Answers for Blue Prism Interview
- What is the difference between SAP APO and SAP IBP? - SAP IBP Online Training Course
- Top 10 Hadoop Big Data Interview Questions & Answers for 2021
Related Interview
- AutoCAD Civil 3D Grading Interview Questions Answers
- PERL Scripting Training Interview Questions Answers
- Murex Software Interview Questions Answers
- Dynamics 365: Supply Chain Management Functional Consultant Expert (MB-335) Training Interview Questions Answers
- IDMC Administration Training Interview Questions Answers
Related FAQ's
- Instructor-led Live Online Interactive Training
- Project Based Customized Learning
- Fast Track Training Program
- Self-paced learning
- In one-on-one training, you have the flexibility to choose the days, timings, and duration according to your preferences.
- We create a personalized training calendar based on your chosen schedule.
- Complete Live Online Interactive Training of the Course
- After Training Recorded Videos
- Session-wise Learning Material and notes for lifetime
- Practical & Assignments exercises
- Global Course Completion Certificate
- 24x7 after Training Support
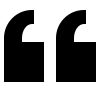