.jpg)
Distributed Control System (DCS) Training covers the fundamentals of industrial automation, focusing on system architecture, real-time process control, redundancy, communication networks, and cybersecurity. Participants will gain expertise in configuring, troubleshooting, and optimizing DCS for various industries, including oil & gas, power plants, and manufacturing. This course is ideal for engineers and technicians looking to enhance their knowledge of modern control systems and Industry 4.0 integration.
Distributed Control System (DCS) Training Interview Questions Answers - For Intermediate
1. How does DCS handle system failures to ensure continuous operation?
DCS employs multiple layers of redundancy and fault-tolerant mechanisms to handle system failures and ensure continuous operation. Redundant controllers, power supplies, communication networks, and I/O modules allow seamless switching in case of failure. Automatic failover mechanisms ensure that a backup system takes over without manual intervention. Alarm notifications and diagnostic tools help operators quickly identify and resolve issues. This approach minimizes downtime and enhances overall system reliability in critical industrial applications.
2. What is the role of Human-Machine Interface (HMI) in DCS?
The Human-Machine Interface (HMI) in a DCS allows operators to monitor and control industrial processes through graphical displays, real-time data visualization, and alarm notifications. It provides an intuitive interface to adjust process variables, analyze trends, and diagnose system issues. HMIs in modern DCS systems are designed for user-friendly interaction, supporting touchscreen displays, mobile access, and multi-layered security. An effective HMI enhances situational awareness and enables faster decision-making for process optimization.
3. What is the function of a control loop in DCS?
A control loop in DCS is a closed-loop system where a controller continuously adjusts a process variable to maintain it at a desired setpoint. It consists of a sensor to measure the variable, a controller to process the data, and an actuator to apply corrections. Common control loops include proportional-integral-derivative (PID) control, which fine-tunes the system response to minimize deviations. Efficient control loops enhance process stability, reduce waste, and improve product quality.
4. What are the different types of I/O modules used in DCS?
DCS uses several types of Input/Output (I/O) modules, including analog input, analog output, digital input, and digital output modules. Analog input modules collect continuous data from sensors, such as temperature or pressure readings. Analog output modules send control signals to actuators like valves. Digital input modules receive binary signals from switches or alarms, while digital output modules control on/off devices like pumps and motors. I/O modules play a crucial role in data acquisition and process control.
5. How does DCS integrate with Manufacturing Execution Systems (MES) and Enterprise Resource Planning (ERP)?
DCS integrates with Manufacturing Execution Systems (MES) and Enterprise Resource Planning (ERP) through industrial communication protocols and middleware solutions. This integration enables real-time data exchange between process control and business systems, allowing organizations to optimize production planning, inventory management, and performance tracking. DCS collects process data, which MES uses for scheduling and execution, while ERP utilizes this information for supply chain and financial decision-making. Such integration enhances overall plant efficiency and resource utilization.
6. What is the significance of data logging in DCS?
Data logging in DCS involves continuous recording of process variables, alarms, and system events for analysis and troubleshooting. It helps identify trends, detect anomalies, and optimize process performance. Historical data logs are essential for compliance reporting, predictive maintenance, and root cause analysis. Advanced DCS systems use high-speed data logging and cloud-based storage to enhance accessibility and data security. Accurate data logging ensures informed decision-making and process improvement.
7. How does DCS support batch processing in industries like pharmaceuticals and food production?
DCS supports batch processing by providing recipe management, sequence control, and real-time monitoring to ensure consistent product quality. It allows operators to configure and execute predefined process sequences while maintaining traceability and regulatory compliance. Batch automation in DCS ensures precise control over ingredient mixing, reaction times, and environmental conditions. Features such as electronic batch records (EBR) help industries maintain high standards of quality assurance and documentation.
8. What is the function of a setpoint in DCS control loops?
A setpoint in DCS control loops is the desired value of a process variable that the controller aims to maintain. The system continuously compares real-time process measurements to the setpoint and adjusts control outputs to minimize deviation. For example, in a temperature control loop, if the actual temperature deviates from the setpoint, the DCS adjusts heating or cooling elements to restore balance. Proper setpoint tuning ensures process stability and optimal performance.
9. How does a DCS handle load changes in a power plant or industrial process?
DCS manages load changes by dynamically adjusting control parameters based on real-time demand and process conditions. Advanced algorithms such as feedforward control and adaptive control help anticipate variations and make proactive adjustments. Load-sharing strategies distribute process loads efficiently across multiple units, preventing system overload or underutilization. In power plants, for example, DCS modulates fuel input and generator output to maintain grid stability and efficiency during fluctuating demand.
10. What are the benefits of modular architecture in DCS?
A modular architecture in DCS offers flexibility, scalability, and ease of maintenance. It allows system components such as controllers, I/O modules, and communication networks to be expanded or replaced without disrupting operations. This design reduces downtime, simplifies troubleshooting, and supports future upgrades. Modular DCS systems also enhance cybersecurity by segmenting control networks and restricting access to critical components. Industries benefit from improved system longevity and reduced lifecycle costs.
11. How does DCS contribute to predictive maintenance?
DCS enables predictive maintenance by continuously monitoring equipment health, detecting early signs of wear, and predicting potential failures. Sensors connected to the DCS collect vibration, temperature, and pressure data, which is analyzed using machine learning and trend analysis. Predictive maintenance reduces unplanned downtime, minimizes repair costs, and extends equipment lifespan. Integration with asset management systems allows automated maintenance scheduling, ensuring uninterrupted plant operations.
12. What is the significance of loop tuning in DCS?
Loop tuning in DCS is the process of adjusting control parameters to achieve optimal system performance. Proper tuning minimizes oscillations, reduces overshoot, and enhances response time. The three primary tuning parameters in a PID controller are proportional (P), integral (I), and derivative (D) gains. Various tuning methods, such as Ziegler-Nichols and trial-and-error approaches, are used to fine-tune control loops. Well-tuned control loops improve process stability, energy efficiency, and product quality.
13. How does a DCS manage process safety in hazardous industries?
DCS enhances process safety by integrating safety instrumented systems (SIS), alarm management, and emergency shutdown (ESD) mechanisms. Safety interlocks prevent unsafe operating conditions, while real-time monitoring ensures early detection of hazardous situations. Advanced DCS systems comply with safety standards such as IEC 61511 and OSHA regulations. Operators receive automated alerts and guided response procedures to mitigate risks. These safety features help industries prevent accidents and ensure regulatory compliance.
14. What role does cloud computing play in modern DCS implementations?
Cloud computing in modern DCS implementations enables remote access, data analytics, and centralized monitoring of industrial processes. Cloud-based DCS solutions provide scalable data storage, predictive maintenance insights, and integration with artificial intelligence (AI). Remote monitoring via cloud platforms allows real-time access to plant performance from anywhere, reducing the need for on-site personnel. Secure cloud connections enhance cybersecurity while improving collaboration between different plant locations.
15. How does DCS contribute to environmental sustainability in industrial processes?
DCS contributes to environmental sustainability by optimizing resource utilization, reducing emissions, and minimizing waste generation. Real-time monitoring ensures efficient energy use and compliance with environmental regulations. Integration with emissions monitoring systems helps track greenhouse gas output and implement corrective actions. Advanced control strategies such as process optimization and energy-efficient scheduling further reduce the carbon footprint of industrial operations. Sustainable practices driven by DCS lead to cost savings and regulatory compliance.
Distributed Control System (DCS) Training Interview Questions Answers - For Advanced
1. How does artificial intelligence (AI) and machine learning (ML) enhance DCS performance and decision-making?
Artificial intelligence (AI) and machine learning (ML) enhance DCS performance by enabling predictive analytics, process optimization, and automated anomaly detection. AI-driven systems analyze historical and real-time data to identify patterns and predict potential failures before they occur. Machine learning algorithms improve control loop tuning by continuously adapting to changing process conditions, reducing variability, and optimizing performance. AI-based anomaly detection helps identify subtle deviations in equipment behavior that may indicate early signs of failure, allowing maintenance teams to take proactive measures. Advanced AI models also enhance alarm management by filtering out nuisance alarms and prioritizing critical ones based on historical response data. Additionally, AI-powered digital twins create virtual replicas of industrial processes, enabling operators to simulate different scenarios and optimize production strategies. As industries adopt AI and ML in DCS, they benefit from increased efficiency, reduced downtime, and enhanced decision-making capabilities.
2. How does a DCS support multi-site operations, and what challenges arise in its implementation?
A DCS supports multi-site operations by enabling centralized monitoring and control of multiple geographically dispersed facilities through high-speed communication networks and cloud-based integration. In such configurations, each site operates with its local controllers while sharing critical data with a central control center. Secure remote access allows operators to monitor processes, analyze performance trends, and coordinate production strategies across multiple locations. However, implementing multi-site DCS comes with challenges such as network latency, cybersecurity risks, and data synchronization issues. Network latency can impact real-time control, requiring high-speed fiber-optic connections or edge computing solutions. Cybersecurity concerns arise due to the increased exposure of DCS networks to external threats, necessitating encryption, firewalls, and intrusion detection systems. Data synchronization ensures consistency across sites, preventing discrepancies in control parameters. By leveraging cloud-based historians, virtualized control environments, and secure connectivity, organizations can achieve efficient multi-site operations with optimized resource allocation and enhanced decision-making capabilities.
3. Explain the role of virtual DCS and its impact on industrial automation.
Virtual Distributed Control Systems (vDCS) are software-based control environments that replace traditional hardware controllers with virtualized instances running on industrial-grade servers or cloud platforms. vDCS enables process automation without requiring physical control hardware, reducing infrastructure costs and improving system flexibility. These systems leverage containerization and virtualization technologies such as VMware or Kubernetes to create scalable and redundant control environments. The impact of vDCS on industrial automation is significant, as it allows organizations to deploy, update, and test control strategies remotely without physical modifications. Virtual DCS also enhances disaster recovery and cybersecurity by enabling automated backups and sandboxed testing environments. However, challenges such as real-time processing constraints, cybersecurity risks, and reliability concerns must be addressed before full-scale adoption. As industries move towards Industry 4.0, vDCS is becoming an essential component of modern automation strategies, facilitating predictive maintenance, cloud-based analytics, and autonomous process optimization.
4. How does DCS support energy management and sustainability in industrial processes?
DCS plays a crucial role in energy management and sustainability by optimizing resource consumption, reducing waste, and ensuring compliance with environmental regulations. By integrating energy monitoring modules, DCS can track power usage, fuel consumption, and emissions in real-time, allowing operators to identify inefficiencies and implement corrective measures. Advanced control strategies such as load shedding, demand response management, and heat recovery optimization enable industries to minimize energy wastage. Additionally, DCS systems support renewable energy integration by balancing conventional power sources with solar, wind, or biomass energy inputs. Carbon footprint reduction is another major focus, as DCS can automatically adjust process parameters to maintain optimal efficiency while reducing greenhouse gas emissions. The integration of AI and machine learning with DCS further enhances sustainability efforts by predicting energy demand, identifying maintenance needs, and optimizing production schedules to reduce peak-hour power consumption.
5. What are the key considerations for designing a fault-tolerant DCS architecture?
Designing a fault-tolerant DCS architecture requires a multi-layered approach that includes redundancy, predictive failure detection, and robust system recovery mechanisms. Redundancy is the foundation of fault tolerance, ensuring that critical components such as controllers, power supplies, and communication networks have backup counterparts ready to take over in case of failure. Predictive failure detection, powered by AI and machine learning, continuously monitors system health, identifying potential issues before they escalate. Robust recovery mechanisms, such as automated failover switching and self-healing network architectures, further enhance resilience. Another key consideration is distributed control logic, which ensures that localized control operations remain functional even if the central network experiences disruptions. Proper segmentation of control loops and data paths minimizes the risk of cascading failures. Additionally, adherence to industry safety and cybersecurity standards (such as IEC 61508 and ISA-99) ensures compliance with best practices for high-reliability DCS implementations.
6. How does a DCS integrate with MES and ERP systems, and what are the benefits of such integration?
DCS integration with Manufacturing Execution Systems (MES) and Enterprise Resource Planning (ERP) systems bridges the gap between plant-floor operations and business-level decision-making. This integration enables real-time data exchange, improving production planning, quality control, and supply chain management. MES provides a layer between DCS and ERP, handling production scheduling, batch tracking, and performance analysis. Through industrial communication protocols such as OPC UA, DCS can transmit process data to MES for monitoring production efficiency, detecting bottlenecks, and generating reports. MES then relays critical insights to ERP systems, which oversee inventory management, financial planning, and procurement. The benefits of this integration include improved production visibility, reduced downtime, optimized resource utilization, and enhanced regulatory compliance. By implementing MES and ERP connectivity, industries achieve a seamless flow of information from the shop floor to executive decision-makers, enhancing overall business agility and responsiveness.
7. What is the role of edge computing in enhancing DCS performance, and how does it improve real-time decision-making?
Edge computing enhances DCS performance by processing data closer to the source, reducing latency, improving real-time decision-making, and minimizing network congestion. Traditional DCS architectures rely on centralized data processing, which can lead to delays in high-speed industrial applications. By deploying edge computing nodes within the DCS framework, data from field devices is processed locally before being sent to higher-level control or cloud-based systems. This decentralized approach reduces dependency on long-distance communication networks, making DCS systems more resilient to connectivity failures. Edge computing also supports advanced analytics, enabling predictive maintenance, anomaly detection, and automated process adjustments in real-time. Additionally, it enhances cybersecurity by limiting exposure to external threats, as sensitive data is processed locally rather than being transmitted across open networks. With the increasing adoption of IoT-enabled devices, edge computing is becoming a critical component of modern DCS implementations, improving responsiveness and overall system efficiency.
8. How does a DCS manage batch processing in industries like pharmaceuticals and food manufacturing?
DCS manages batch processing by implementing recipe-based control, strict compliance tracking, and flexible sequencing strategies to ensure product consistency and regulatory adherence. Unlike continuous processes, batch processing involves multiple production stages, where different ingredients or raw materials must be combined, reacted, or processed according to predefined sequences. DCS ensures precision by automating batch execution, enforcing quality control parameters, and logging critical process variables. Recipe-based control systems allow operators to define and modify batch parameters, ensuring repeatability and scalability. Compliance tracking is crucial in industries like pharmaceuticals and food manufacturing, where regulatory standards such as FDA 21 CFR Part 11 mandate electronic records, traceability, and data integrity. DCS integrates with MES systems to facilitate electronic batch records (EBR), providing complete documentation of each batch’s history, deviations, and quality control checkpoints. The flexibility of modern DCS batch management allows industries to adapt to changing market demands while maintaining high levels of efficiency and product quality.
9. How does digital twin technology enhance DCS functionality and predictive analysis?
Digital twin technology enhances DCS functionality by creating a virtual replica of industrial processes, allowing real-time monitoring, simulation, and predictive analysis. A digital twin mirrors the actual plant environment, integrating live data from DCS sensors and control systems to simulate performance under various operating conditions. This technology enables engineers to test process optimizations, troubleshoot issues, and forecast system behavior without disrupting live operations. By leveraging AI and machine learning, digital twins analyze historical and real-time data to identify potential failures, optimize control strategies, and improve efficiency. Predictive analysis through digital twins reduces maintenance costs by detecting anomalies before they lead to breakdowns, allowing proactive interventions. Additionally, digital twin technology supports remote monitoring, enabling global teams to assess plant performance and make data-driven decisions. As industries embrace Industry 4.0, digital twins are becoming a critical tool for enhancing DCS functionality, minimizing downtime, and improving overall process reliability.
10. How does a DCS handle real-time data processing, and what are the challenges associated with high-speed control applications?
A DCS handles real-time data processing by continuously collecting, analyzing, and responding to process variables from field sensors, actuators, and control loops. The system operates on a deterministic control architecture, ensuring precise timing for executing control commands and process adjustments. To achieve this, DCS employs high-speed processors, optimized I/O modules, and industrial communication protocols such as OPC UA, Modbus TCP/IP, and Profibus. These components work together to minimize latency, enabling millisecond-level response times for critical control applications. However, challenges arise when handling high-speed control applications such as turbine control, robotic automation, and precision manufacturing. Network congestion, processing delays, and data synchronization issues can affect real-time performance, leading to inefficiencies or potential safety risks. Addressing these challenges requires advanced buffering techniques, edge computing integration, and redundant communication pathways. Additionally, using AI-based predictive analytics can enhance DCS decision-making by identifying process deviations before they escalate into failures. Ensuring robust cybersecurity measures is also crucial, as real-time data processing systems are increasingly targeted by cyber threats.
11. How does a DCS ensure regulatory compliance in industries such as pharmaceuticals, oil and gas, and nuclear power?
DCS ensures regulatory compliance by integrating standardized process controls, maintaining audit trails, and implementing automated reporting systems to meet industry-specific legal and safety requirements. In pharmaceutical manufacturing, compliance with FDA 21 CFR Part 11 is essential for electronic records and data integrity. DCS systems in pharmaceutical plants enable batch recordkeeping, deviation tracking, and validation testing to meet Good Manufacturing Practice (GMP) standards. In the oil and gas sector, DCS is designed to adhere to environmental and safety regulations such as API (American Petroleum Institute) and IEC 61511 for Safety Instrumented Systems (SIS). These systems monitor emissions, prevent hazardous incidents, and ensure process safety through automated emergency shutdowns (ESD). In nuclear power plants, regulatory bodies such as the International Atomic Energy Agency (IAEA) and the Nuclear Regulatory Commission (NRC) mandate strict control measures, real-time monitoring, and redundancy in safety-critical systems. The DCS in nuclear facilities must comply with IEC 60880, ensuring fault tolerance and reliability under extreme conditions. By integrating compliance-focused modules and secure reporting tools, DCS helps industries meet regulatory obligations while optimizing operational performance.
12. How does artificial intelligence (AI) enhance alarm management in modern DCS implementations?
AI enhances alarm management in modern DCS implementations by reducing false alarms, prioritizing critical notifications, and providing predictive analytics for proactive issue resolution. Traditional DCS alarm systems generate vast numbers of alerts, often leading to alarm fatigue, where operators become desensitized to warnings due to excessive notifications. AI-driven alarm management uses machine learning algorithms to analyze alarm patterns, suppress redundant alerts, and identify abnormal behavior that requires immediate attention. Predictive analytics enable AI to assess real-time process data and forecast potential failures before they trigger alarms, allowing preventive actions to be taken in advance. Additionally, AI-based alarm systems incorporate natural language processing (NLP) to generate intelligent recommendations for operators, providing step-by-step guidance on resolving issues efficiently. Adaptive learning mechanisms also allow AI to refine alarm thresholds over time, optimizing system response to process variations. By implementing AI-enhanced alarm management, industries improve operator efficiency, reduce downtime, and enhance overall plant safety.
13. What are the best practices for securing DCS from cyber threats, and how do industrial cybersecurity frameworks assist in this process?
Securing a DCS from cyber threats requires a multi-layered defense strategy, including network segmentation, access control, intrusion detection, and compliance with cybersecurity frameworks such as IEC 62443 and NIST 800-82. Network segmentation involves isolating the DCS from corporate IT networks and the internet to prevent unauthorized access. Implementing firewalls, virtual private networks (VPNs), and secure communication protocols such as TLS/SSL enhances network security. Role-based access control (RBAC) ensures that only authorized personnel can modify control settings, reducing insider threats. Intrusion detection and prevention systems (IDPS) continuously monitor network traffic for anomalies, blocking potential cyberattacks before they compromise system integrity. Regular software patching and firmware updates address known vulnerabilities, preventing exploits from targeting outdated systems. Compliance with industrial cybersecurity frameworks like IEC 62443 provides a structured approach to risk assessment, security policy development, and incident response planning. Additionally, conducting regular cybersecurity audits, penetration testing, and employee awareness training strengthens the overall security posture of a DCS, ensuring resilience against evolving cyber threats.
14. How does DCS support remote operations and what are the security risks involved?
DCS supports remote operations by enabling web-based access, cloud integration, and mobile connectivity for monitoring and controlling industrial processes from off-site locations. Remote access capabilities allow engineers, operators, and decision-makers to review real-time process data, adjust control parameters, and receive alerts from anywhere. This is particularly beneficial for geographically distributed industries such as oil and gas, water treatment, and power generation, where on-site staffing may be limited. Secure VPN connections, multi-factor authentication (MFA), and encrypted communication channels are commonly used to protect remote access. However, security risks associated with remote DCS operations include unauthorized access, malware attacks, and data interception. If not properly secured, remote access points can serve as entry points for cybercriminals to infiltrate critical control networks. Implementing zero-trust security models, real-time access logging, and strict authentication protocols mitigates these risks. Additionally, continuous network monitoring and anomaly detection tools help identify suspicious activities before they escalate into security incidents. Ensuring compliance with cybersecurity best practices allows industries to leverage the benefits of remote DCS operations without compromising system integrity.
15. How does DCS contribute to Industry 4.0, and what future advancements can be expected?
DCS plays a pivotal role in Industry 4.0 by enabling smart manufacturing, real-time data analytics, and seamless integration with advanced technologies such as IIoT, AI, and cloud computing. The transition from traditional DCS to intelligent automation systems enhances operational efficiency through predictive maintenance, autonomous process optimization, and digital twin simulations. Future advancements in DCS will include self-learning AI models that continuously refine control algorithms based on historical and real-time data. Edge computing will further enhance DCS performance by reducing latency and enabling faster decision-making at the device level. Integration with blockchain technology will provide secure and tamper-proof data records, ensuring transparency and reliability in process tracking. As 5G networks become more prevalent, DCS will leverage high-speed wireless connectivity for ultra-low-latency communication between sensors, controllers, and cloud platforms. The adoption of augmented reality (AR) and virtual reality (VR) for operator training and remote troubleshooting will enhance human-machine interaction within industrial environments. As industries continue embracing digital transformation, the next-generation DCS will evolve into a fully autonomous, AI-driven ecosystem capable of self-optimizing production processes with minimal human intervention.
Course Schedule
Apr, 2025 | Weekdays | Mon-Fri | Enquire Now |
Weekend | Sat-Sun | Enquire Now | |
May, 2025 | Weekdays | Mon-Fri | Enquire Now |
Weekend | Sat-Sun | Enquire Now |
Related Courses
Related Articles
Related Interview
Related FAQ's
- Instructor-led Live Online Interactive Training
- Project Based Customized Learning
- Fast Track Training Program
- Self-paced learning
- In one-on-one training, you have the flexibility to choose the days, timings, and duration according to your preferences.
- We create a personalized training calendar based on your chosen schedule.
- Complete Live Online Interactive Training of the Course
- After Training Recorded Videos
- Session-wise Learning Material and notes for lifetime
- Practical & Assignments exercises
- Global Course Completion Certificate
- 24x7 after Training Support
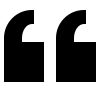