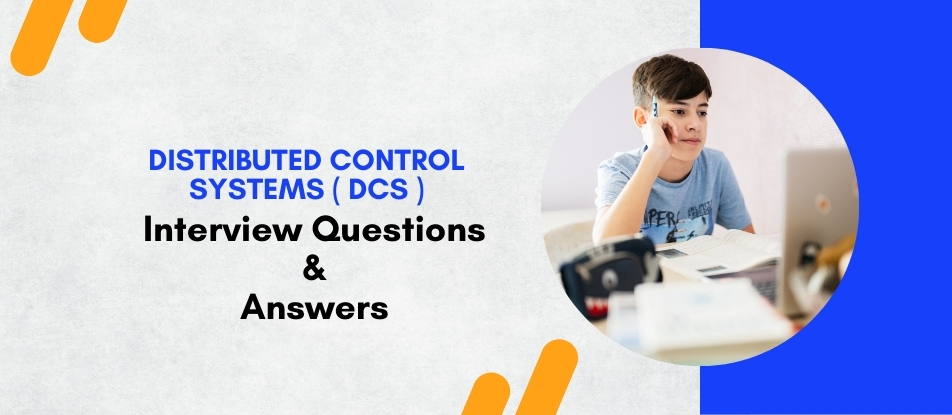
Master the fundamentals and advanced features of Distributed Control Systems (DCS) with this in-depth training. The course covers system architecture, control strategies, real-time data processing, redundancy, and alarm management. Participants will gain hands-on expertise in configuring, maintaining, and optimizing DCS for seamless process automation. Designed for engineers and technicians, this training prepares you to handle complex industrial operations with precision and reliability.
Distributed Control Systems ( DCS ) Interview Questions Answers - For Intermediate
1. What industries commonly use DCS systems?
Industries like oil and gas, petrochemicals, power generation, water treatment, and manufacturing rely on DCS for monitoring and controlling complex processes involving multiple interconnected subsystems.
2. How is data redundancy achieved in DCS systems?
Data redundancy in a DCS is achieved by replicating critical data and communication paths across redundant servers, controllers, and networks. This ensures no data loss during failures.
3. What is the role of field devices in a DCS?
Field devices like sensors and actuators measure process variables (e.g., temperature, pressure) and execute control commands. They serve as the interface between the process and the control system.
4. Explain the difference between open-loop and closed-loop control in a DCS.
Open-loop control sends predefined commands without feedback, suitable for simple operations. Closed-loop control uses real-time feedback from sensors to adjust process variables, ensuring desired outputs.
5. What is a control strategy, and how is it implemented in DCS?
A control strategy defines how a process is managed, including control algorithms, loops, and logic. In a DCS, it is implemented using function blocks, logic diagrams, and predefined templates.
6. What is the significance of process historians in DCS?
Process historians store long-term process data for analysis, trend monitoring, and optimization. They help identify inefficiencies and improve system performance over time.
7. How does DCS manage alarms during critical events?
DCS systems prioritize alarms based on severity and use features like alarm suppression, shelving, and filtering to prevent alarm flooding, ensuring operators can focus on critical issues.
8. What are the steps involved in configuring a new control loop in a DCS?
Steps include:
- Identifying process variables.
- Configuring I/O modules.
- Setting up the control logic.
- Tuning parameters (e.g., PID settings).
- Testing and commissioning.
9. What is the purpose of I/O modules in a DCS?
I/O modules connect field devices to the controllers. They handle analog and digital signals, converting them as necessary for processing by the system.
10. How does a DCS support remote monitoring?
DCS systems integrate with secure networks and web-based interfaces to enable operators to monitor and control processes remotely, ensuring operational continuity in off-site scenarios.
11. What is the importance of loop tuning in DCS?
Loop tuning ensures control loops operate optimally by adjusting parameters like proportional, integral, and derivative settings. Proper tuning minimizes overshoot, oscillations, and response time.
12. What is hot swapping in DCS, and why is it beneficial?
Hot swapping allows components like I/O cards to be replaced without shutting down the system. It reduces downtime and maintains operational continuity.
13. What are the challenges of scaling a DCS system?
Scaling a DCS involves adding more controllers, I/O points, and HMIs. Challenges include maintaining system performance, and network bandwidth, and ensuring backward compatibility with existing configurations.
14. What is the difference between Foundation Fieldbus and Profibus in DCS?
Foundation Fieldbus is used for process automation with features like field-level control and diagnostics. Profibus is more versatile, supporting both discrete and process automation but relies more on controllers for processing.
15. How does a DCS handle fail-safe operations?
Fail-safe operations ensure the system transitions to a safe state during a failure. DCS achieves this using predefined safety logic, redundant components, and emergency shutdown (ESD) systems.
Distributed Control Systems ( DCS ) Interview Questions Answers - For Advanced
1. How does a Distributed Control System (DCS) manage system load balancing across multiple controllers, and why is it crucial?
In a DCS, load balancing is achieved by distributing process control tasks across multiple controllers. Each controller handles a subset of the process, ensuring no single controller is overwhelmed. For example, in a refinery, one controller might manage distillation while another oversees heat exchange. The communication network ensures coordination between controllers for smooth process operations. This distribution is crucial as it prevents bottlenecks, enhances performance, and ensures system reliability. In cases of heavy computational loads, tasks can be reallocated dynamically to maintain optimal performance and prevent system degradation.
2. What is the role of failover mechanisms in ensuring the reliability of a DCS system?
Failover mechanisms in a DCS are designed to seamlessly switch to backup systems or components when a failure occurs. For instance, if a primary controller becomes non-functional, the system automatically shifts control to a redundant controller with minimal or no disruption to the process. This is achieved by maintaining real-time synchronization between primary and backup components. Failover mechanisms are critical in industries like nuclear power and pharmaceuticals, where even minor disruptions can have catastrophic consequences. They ensure uninterrupted operations, safeguarding both product quality and plant safety.
3. How does a DCS handle dynamic process variability in real-time control?
A DCS handles dynamic process variability by leveraging real-time data acquisition, advanced control algorithms, and predictive analytics. Sensors continuously monitor process variables like pressure, flow, and temperature, and the system adjusts control outputs dynamically to maintain stability. For instance, in a chemical plant, sudden fluctuations in reactant feed rates are immediately corrected by adjusting valve positions and pump speeds. Predictive algorithms anticipate potential deviations based on historical trends and intervene proactively. This ability to respond to variability ensures consistent process performance and minimizes risks.
4. Explain the importance of integrating safety instrumented systems (SIS) with DCS and how it is achieved.
Safety Instrumented Systems (SIS) are integrated with DCS to provide an additional layer of protection against hazardous events. While the DCS focuses on process control and optimization, the SIS operates independently to take emergency actions like shutting down equipment or activating alarms. Integration is achieved through dedicated communication protocols and gateways, ensuring seamless data exchange while maintaining functional independence. For example, in an oil refinery, the SIS might trigger a shutdown if it detects a critical pressure rise, even if the DCS is still operational. This integration enhances overall plant safety and ensures compliance with industrial safety standards.
5. How do modern DCS systems support remote diagnostics and maintenance?
Modern DCS systems enable remote diagnostics and maintenance through secure communication protocols, cloud-based platforms, and IoT-enabled devices. Operators can access system diagnostics, performance metrics, and alarms from remote locations, facilitating real-time decision-making. For instance, vibration analysis data from rotating equipment can be accessed remotely to identify potential failures. Remote maintenance reduces downtime and operational costs by allowing experts to troubleshoot and resolve issues without being physically present on-site. However, robust cybersecurity measures are essential to protect against unauthorized access.
6. How does a DCS manage large-scale process data efficiently for real-time and historical analysis?
DCS systems manage large-scale process data using hierarchical storage and advanced data compression techniques. Real-time data is processed and stored in controllers and HMIs for immediate use, while historical data is archived in data historians. These historians utilize optimized databases designed for time-series data, enabling fast retrieval and analysis. For instance, operators in a power plant can access 10 years of turbine efficiency data within seconds to identify trends. This dual approach ensures both immediate decision-making and long-term process optimization.
7. What is the role of advanced analytics in improving DCS performance and decision-making?
Advanced analytics enhance DCS performance by identifying inefficiencies, predicting failures, and optimizing control strategies. Techniques like machine learning and artificial intelligence analyze historical and real-time data to uncover patterns and correlations that are not apparent through traditional methods. For example, predictive analytics can forecast equipment failures based on vibration patterns, enabling proactive maintenance. Advanced analytics also support process optimization by identifying optimal operating conditions, reducing energy consumption, and improving product quality.
8. How does a DCS handle multi-site operations, and what challenges does this pose?
A DCS handles multi-site operations by employing centralized monitoring and control through networked systems. Each site operates its own localized DCS, but they are connected to a central supervisory system that aggregates data and enables coordination. For example, a multinational chemical company might monitor production lines in different countries from a single control center. Challenges include ensuring reliable communication across sites, maintaining data synchronization, and addressing differences in local regulatory requirements. Scalability and robust cybersecurity are critical to overcoming these challenges.
9. What are the security challenges associated with integrating IoT devices into a DCS, and how are they addressed?
Integrating IoT devices into a DCS introduces security challenges like increased attack surfaces, vulnerabilities in device firmware, and risks of unauthorized access. These challenges are addressed through encryption, secure boot mechanisms, and regular firmware updates. Additionally, network segmentation isolates IoT devices from critical DCS components, reducing exposure to threats. For instance, in a smart grid system, IoT sensors collecting energy usage data are securely linked to the DCS while being isolated from the core control network to prevent cyberattacks.
10. What is the role of virtualization in modern DCS systems, and what are its advantages?
Virtualization in DCS involves running multiple virtual machines (VMs) on a single physical server to host control applications, HMIs, and data historians. This reduces hardware dependency, improves system flexibility, and simplifies disaster recovery. For example, a virtualized DCS can quickly restore operations on backup servers in case of hardware failure. Virtualization also enables easier upgrades and testing, as new configurations can be validated in virtual environments before deployment.
11. How does DCS handle control loop optimization, and why is it important?
Control loop optimization in DCS is achieved through techniques like tuning PID parameters, implementing feedforward control, and using advanced algorithms like fuzzy logic or neural networks. Properly optimized loops reduce process variability, enhance product quality, and minimize energy consumption. For instance, in a distillation column, precise control of reflux ratios ensures optimal separation efficiency. Regular loop audits and optimization are essential to maintaining long-term process performance.
12. Explain the importance of standardized communication protocols in ensuring interoperability in DCS systems.
Standardized communication protocols like OPC, Modbus, and Profibus ensure interoperability between devices from different manufacturers in a DCS. These protocols define rules for data exchange, enabling seamless integration of sensors, actuators, and controllers. For example, a DCS can connect a third-party flow meter using Modbus without requiring custom configurations. Standardization simplifies system design, reduces integration costs, and ensures compatibility with future technologies.
13. What challenges arise in upgrading legacy DCS systems, and how can they be mitigated?
Upgrading legacy DCS systems involves challenges like compatibility with modern components, data migration, and minimizing operational disruptions. These challenges can be mitigated by adopting a phased approach, where new systems are integrated alongside existing ones gradually. Gateways and protocol converters facilitate communication between old and new components. Rigorous testing in simulation environments ensures a smooth transition, reducing the risk of downtime during the upgrade process.
14. How does a DCS support compliance with industry standards and regulations?
DCS systems support compliance by implementing features like electronic batch records, audit trails, and validation protocols. These ensure that processes adhere to industry standards such as ISA-88 for batch control or IEC 61511 for functional safety. For example, in pharmaceutical manufacturing, a DCS can maintain detailed records of production parameters to meet FDA requirements. Automated reporting and validation tools simplify the compliance process and reduce the risk of regulatory penalties.
15. What role do simulation and emulation play in DCS training and system testing?
Simulation and emulation are integral to DCS training and system testing, providing a safe environment to develop, validate, and optimize control strategies without impacting live operations. In training, simulation allows operators to practice handling process scenarios and emergencies, improving their preparedness. In testing, emulation mimics hardware and process behavior to verify system configurations and logic. For instance, before commissioning a new control strategy in a power plant, engineers can simulate its impact on turbine performance, ensuring reliability and efficiency. These tools reduce commissioning risks and enhance overall system performance.
Course Schedule
Jul, 2025 | Weekdays | Mon-Fri | Enquire Now |
Weekend | Sat-Sun | Enquire Now | |
Aug, 2025 | Weekdays | Mon-Fri | Enquire Now |
Weekend | Sat-Sun | Enquire Now |
Related Courses
Related Articles
Related Interview
Related FAQ's
- Instructor-led Live Online Interactive Training
- Project Based Customized Learning
- Fast Track Training Program
- Self-paced learning
- In one-on-one training, you have the flexibility to choose the days, timings, and duration according to your preferences.
- We create a personalized training calendar based on your chosen schedule.
- Complete Live Online Interactive Training of the Course
- After Training Recorded Videos
- Session-wise Learning Material and notes for lifetime
- Practical & Assignments exercises
- Global Course Completion Certificate
- 24x7 after Training Support
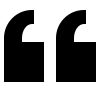