.jpg)
The Dynamics 365: Supply Chain Management Functional Consultant Expert (MB-335) course provides in-depth training on configuring and managing key supply chain components within Microsoft Dynamics 365. Participants will learn to implement solutions across procurement, manufacturing, inventory, warehousing, and transportation. Designed for functional consultants and professionals, the course prepares learners to streamline operations, enhance efficiency, and successfully pass the MB-335 certification exam with confidence.
Dynamics 365: Supply Chain Management Functional Consultant Expert (MB-335) Training Interview Questions Answers - For Intermediate
1. What is the difference between planned orders and firmed orders in Master Planning?
Planned orders are system-generated suggestions based on demand and supply calculations from master planning. They are not yet confirmed and allow planners to review and adjust as needed. Once a planner validates and approves a planned order, it is firmed—converted into an actual purchase, transfer, or production order. Firming helps lock down the supply chain process for execution.
2. How does the system handle backorders in Dynamics 365 Supply Chain Management?
Backorders occur when demand cannot be met due to insufficient inventory. Dynamics 365 provides backorder management tools that allow sales orders to remain open until stock becomes available. Users can view backorder details, reserve inventory once it's restocked, and communicate delays with customers. It also helps in analyzing supply gaps and adjusting inventory or procurement strategies accordingly.
3. Explain the use of inventory reservations and their types.
Inventory reservation ensures that specific inventory is set aside for particular orders or processes. Dynamics 365 allows manual and automatic reservations at different levels—batch, serial, or location. Reservation policies prevent double-booking of inventory and improve order fulfillment rates. Automatic reservation can be configured during order creation, while manual reservation gives planners greater control in constrained scenarios.
4. What are the key differences between discrete, lean, and process manufacturing in Dynamics 365?
Discrete manufacturing handles assembly of distinct items (e.g., electronics), lean manufacturing focuses on flow efficiency and waste reduction (e.g., kanban processes), while process manufacturing deals with formulas and recipes (e.g., chemicals or food). Dynamics 365 supports all three with tailored functionalities like production orders, kanban boards, and batch orders, providing flexibility across industries.
5. How are sales and purchase agreements used in supply chain transactions?
Sales and purchase agreements are contracts with customers or vendors that define conditions like pricing, quantity, and validity dates. They help in enforcing negotiated terms over multiple transactions. When processing orders, the system automatically applies agreement terms, improving compliance, streamlining transactions, and enabling better tracking of volume commitments or rebates.
6. What is dual-write integration, and how does it benefit supply chain operations?
Dual-write integration provides real-time, bidirectional data synchronization between Dynamics 365 Supply Chain Management and Dynamics 365 Customer Engagement apps. This ensures that customer, product, and order data are consistent across CRM and ERP systems. It enhances collaboration between sales and operations, improves order accuracy, and reduces data silos, thereby supporting better end-to-end visibility.
7. How do warehouse mobile devices integrate into Dynamics 365?
Warehouse mobile devices connect through the Warehouse Management mobile app, enabling workers to perform real-time inventory activities like receiving, picking, and cycle counting. Admins configure mobile device menus and work templates to streamline tasks. The app improves data accuracy, reduces paperwork, and increases warehouse productivity by providing guided workflows and barcode scanning.
8. What is the purpose of location directives in warehouse management?
Location directives determine where items should be picked from or put away during warehouse work. They guide workers to optimal locations based on rules like zone, aisle, item type, or quantity. Location directives enhance space utilization, reduce travel time, and ensure consistency in warehouse operations, especially when combined with work templates.
9. How do you manage transportation and logistics within Dynamics 365?
Transportation management in Dynamics 365 allows users to plan and execute inbound and outbound shipments efficiently. It includes features like route planning, freight reconciliation, and carrier rating. Businesses can consolidate shipments, generate transportation orders, and assign carriers. Integration with warehouse and sales processes ensures coordinated delivery and cost tracking.
10. Explain how kanban boards are used in lean manufacturing setups.
Kanban boards in Dynamics 365 are visual tools that represent manufacturing processes. They track the status of kanban jobs, allowing users to manage pull-based production efficiently. Boards reflect real-time updates on material requirements, work-in-progress, and delivery schedules. This supports lean principles like reducing waste, increasing flow, and aligning production with demand.
11. How does the costing method impact inventory valuation in Dynamics 365?
Dynamics 365 supports multiple costing methods—FIFO, LIFO, Standard, Weighted Average, and Moving Average. The selected method directly affects inventory valuation, cost of goods sold, and profitability analysis. For example, standard costing provides predictable margins, while FIFO may be used for perishable goods. The right method aligns with accounting policies and operational needs.
12. What is the purpose of inventory aging reports?
Inventory aging reports show how long inventory items have been in stock, categorized into aging buckets. This helps identify slow-moving or obsolete items, informing decisions on markdowns, promotions, or disposal. The report supports better inventory turnover, reduces carrying costs, and helps maintain healthy stock levels in the warehouse.
13. How is demand forecasting adjusted in real-world scenarios?
While Dynamics 365 uses historical data and statistical models to create forecasts, real-world adjustments are common. Planners may override forecast values based on seasonality, upcoming promotions, or market shifts. Excel integration allows easy collaboration, while machine learning models in Azure can be linked for enhanced predictive accuracy. Forecast accuracy is continuously monitored and refined.
14. How do you perform physical inventory counting using Dynamics 365?
Physical inventory counting involves generating counting journals, selecting items or locations, entering actual quantities, and posting differences. Users can conduct blind counts or enable system guidance. Dynamics 365 offers cycle counting for periodic checks and full inventory counts for year-end audits. Integration with mobile devices makes counting faster and more accurate.
15. What is the role of batch attributes in process manufacturing?
Batch attributes represent specific characteristics of a product batch, such as potency, color, or expiry date. In Dynamics 365, these attributes are used during production, quality checks, and sales to ensure compliance with standards. They help in batch selection, product substitution, and customer-specific requirements. Proper configuration ensures traceability and product consistency.
Dynamics 365: Supply Chain Management Functional Consultant Expert (MB-335) Training Interview Questions Answers - For Advanced
1. How would you design and implement a make-to-order (MTO) production process in Dynamics 365?
Designing a make-to-order (MTO) process involves configuring production and sales integration so that items are produced only upon receiving a customer order. In D365, this starts with defining items as MTO using the default order type settings or by using planning groups. Sales orders can trigger automatic generation of production orders via the ‘order-to-production’ feature. Pegging ensures each production order is linked to a specific sales order, maintaining traceability. Master planning can be fine-tuned to calculate specific requirements per order. Batch jobs ensure automation, while delivery control groups help manage customer promise dates. This setup minimizes inventory holding, improves customization flexibility, and aligns production closely with demand.
2. Explain how to use business events in Dynamics 365 to enhance supply chain visibility.
Business events in D365 are used to trigger external workflows or notifications based on specific system activities—such as purchase order confirmations or inventory adjustments. These events can be configured to send payloads to Azure Event Grid, Service Bus, or Power Automate. For supply chain visibility, business events can notify planners about delays, trigger alerts on inventory thresholds, or initiate vendor collaboration updates. This real-time communication supports proactive decision-making. For example, when a production order is released, a business event can update external MES systems or notify supervisors via Teams or email.
3. How can you manage hazardous materials compliance in D365 SCM?
Managing hazardous materials (HAZMAT) requires classification, documentation, and controls throughout procurement, storage, transport, and disposal. In D365, HAZMAT items are flagged with specific product attributes. You can configure transportation codes, safety data sheets, and warehouse handling instructions. Labels and documents can be generated via Electronic Reporting. Integration with warehouse management ensures that storage and picking rules are enforced—e.g., avoiding co-storage of reactive chemicals. Compliance with global regulations like OSHA, REACH, or GHS can be achieved through extensions or integration with third-party regulatory databases.
4. How do you implement multi-echelon inventory planning in D365?
Multi-echelon inventory planning (MEIP) involves managing stock across multiple levels of the supply chain, such as central warehouses, regional hubs, and retail outlets. In D365, MEIP is supported through hierarchical site and warehouse configurations, inventory allocation policies, and transfer planning. Master planning can be configured with different coverage groups and safety stock policies for each echelon. Replenishment can be set to trigger automatically between levels, maintaining optimal flow. Analytics like days of inventory on hand and fulfillment rates help optimize stocking decisions and reduce overall supply chain costs.
5. What strategies can be used for demand-driven material requirements planning (DDMRP) in Dynamics 365?
Though D365 doesn’t natively offer full DDMRP, elements can be mimicked through smart configuration. You can use safety stock, demand forecasts, and real-time supply signals to drive planning. Reorder point planning, minimum coverage settings, and buffer zones at key decoupling points simulate DDMRP logic. With real-time dashboards, planners can respond to demand spikes or supply delays. Power BI can visualize stock buffers and lead time variances. For full DDMRP functionality, ISVs or Power Platform-based customizations may be integrated.
6. How does D365 manage substitute items in sales and production scenarios?
Substitute items are configured in the released product’s item substitution section. In sales, when a product is out of stock, substitutes can be offered based on rules or manually selected by the sales agent. In production, substitutions can be defined on the BOM with validity dates, conditions, and approval levels. During material shortage, planners can switch to substitutes with minimal disruption. This feature supports continuity in operations, reduces downtime, and improves customer service levels in supply chain disruptions.
7. How would you approach implementing cross-docking in warehouse management?
Cross-docking enables goods to be received and immediately moved to outbound staging without long-term storage. In D365, this is configured through location directives and work templates. You define cross-docking templates that evaluate existing demand—like sales or transfer orders—and link them to inbound receipts. Upon receiving goods, the system automatically creates work to transfer the items to the outbound dock. This reduces handling costs, speeds up delivery, and is especially beneficial for high-volume or perishable items.
8. Explain how you would customize inventory dimensions for a specific industry requirement.
Custom inventory dimensions are added through the inventory dimensions framework. For example, a fashion retailer may require a "season" or "collection" dimension. After extending the data model and enabling the dimension in product tracking and inventory forms, the new dimension can be applied to all relevant transactions. Proper testing is required to ensure compatibility with costing, reservations, and warehouse operations. Custom dimensions allow for more granular reporting and better alignment with industry-specific tracking needs.
9. How do you use data entities and integration tools to enable third-party logistics (3PL) integration?
To integrate with 3PL providers, data entities like sales orders, inventory transactions, ASN (advanced shipping notice), and shipment confirmations are exposed via OData or batch exports. Power Automate or Logic Apps can be used to create middleware pipelines for scheduling, transforming, and sending/receiving data. APIs are also used for real-time operations such as order updates or tracking. Security via Azure AD tokens and throttling controls are important considerations. 3PL integration improves visibility and reduces manual work across outbound logistics.
10. How would you manage seasonality and promotional events in planning and forecasting?
Seasonality is managed through statistical forecasting models that factor in historical patterns and cycles. D365 allows for importing forecast data with time periods and allocation keys. Promotional events can be overlaid as manual adjustments. Separate forecast models can be created for each region or product group. Integration with CRM or external market data sources further enhances accuracy. Planners should analyze the uplift from past promotions to model future events. Monitoring forecast accuracy post-event helps refine future strategies.
11. How do you manage security and segregation of duties (SoD) in SCM processes?
Security in D365 is managed through roles, duties, and privileges. For SCM, roles like inventory manager, warehouse worker, or production planner are configured with precise access controls. SoD policies are defined to prevent users from executing conflicting tasks (e.g., creating and approving purchase orders). The security diagnostics workspace flags violations. Workflows enforce process controls. This setup reduces fraud risk and ensures compliance with standards like SOX (Sarbanes–Oxley).
12. How do you support sustainability goals using Dynamics 365 Supply Chain Management?
Sustainability initiatives are supported through features like product lifecycle management, recycling tracking, and carbon footprint monitoring. D365 allows capturing environmental attributes on products, tracking energy usage in production, and enforcing supplier compliance standards. Batch traceability supports responsible sourcing. Integration with Microsoft Sustainability Manager helps collect and analyze ESG data. Smart planning and route optimization reduce waste and emissions, aligning the supply chain with corporate sustainability goals.
13. How would you handle a scenario involving simultaneous production and subcontracting?
In such scenarios, some route operations are performed in-house, while others are outsourced. The system allows mixed-mode production by marking specific operations as subcontracted and generating PO lines accordingly. Coordination is key—production cannot proceed until subcontracted operations are completed. Proper scheduling ensures minimal delays. Costs are tracked distinctly for each type of operation, allowing for profitability analysis. Quality checks can be configured both pre- and post-subcontracting.
14. How do you leverage Power Platform in combination with D365 for SCM enhancements?
Power Platform tools—Power BI, Power Apps, and Power Automate—extend D365 functionality. Power Apps can be used to build mobile apps for field inventory management or vendor onboarding. Power Automate enables workflow automation—like triggering reorder approvals or notifying warehouse teams. Power BI provides analytics on supply chain KPIs like OTIF, backorders, and lead times. These tools offer low-code options to tailor solutions without modifying the core ERP system.
15. How do you approach a full-scale SCM implementation from discovery to go-live?
The process begins with discovery and requirements gathering, including business process mapping and gap analysis. The fit-gap results inform solution design and functional specifications. Next, the system is configured in phases, starting with master data and foundational modules. Data migration strategies are defined early, with mock runs and validation checkpoints. Testing involves unit tests, user acceptance testing (UAT), and performance testing. Change management, including training and communication, is critical to adoption. Cutover planning ensures minimal downtime. After go-live, post-deployment support and continuous improvement processes help stabilize operations and drive value.
Course Schedule
Apr, 2025 | Weekdays | Mon-Fri | Enquire Now |
Weekend | Sat-Sun | Enquire Now | |
May, 2025 | Weekdays | Mon-Fri | Enquire Now |
Weekend | Sat-Sun | Enquire Now |
Related Courses
Related Articles
Related Interview
Related FAQ's
- Instructor-led Live Online Interactive Training
- Project Based Customized Learning
- Fast Track Training Program
- Self-paced learning
- In one-on-one training, you have the flexibility to choose the days, timings, and duration according to your preferences.
- We create a personalized training calendar based on your chosen schedule.
- Complete Live Online Interactive Training of the Course
- After Training Recorded Videos
- Session-wise Learning Material and notes for lifetime
- Practical & Assignments exercises
- Global Course Completion Certificate
- 24x7 after Training Support
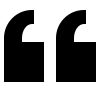