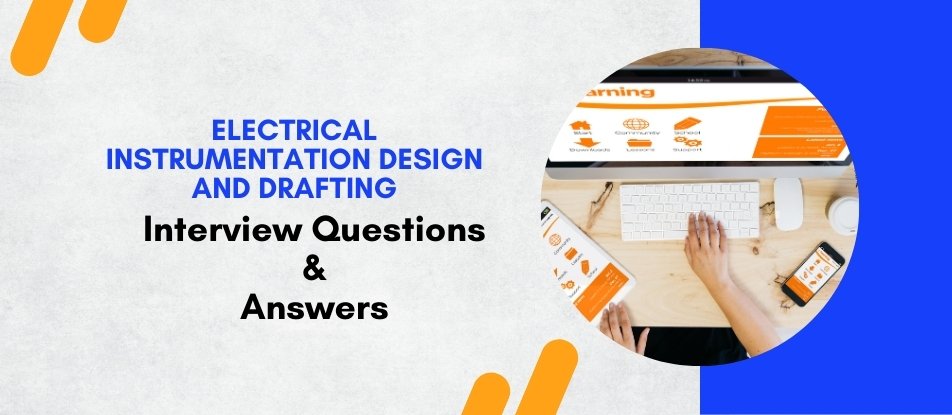
Electrical Instrumentation Design and Drafting Training equips participants with essential skills in designing and drafting electrical and instrumentation systems. This course covers key topics such as control systems, wiring diagrams, loop drawings, and P&IDs. Ideal for engineers and designers, it provides hands-on experience with industry-standard tools to enhance precision and efficiency in electrical and instrumentation projects.
Electrical Instrumentation Design and Drafting Interview Questions Answers - For Intermediate
1. Explain the purpose of a Piping and Instrumentation Diagram (P&ID) in the design of an instrumentation system.
A P&ID provides a detailed graphical representation of a process system, showing all piping, equipment, instrumentation, and control devices. It serves as a blueprint for designing and understanding the process flow and control strategies, facilitating communication among engineers, and ensuring proper integration of instruments within the system.
2. What is the significance of loop diagrams in instrumentation, and what key information do they convey?
Loop diagrams depict the wiring and connections of an individual control loop, including instruments, junction boxes, marshaling panels, and control systems. They provide detailed information on signal types, cable numbers, terminal points, and instrument ranges, essential for the installation, troubleshooting, and maintenance of control loops.
3. Describe the difference between analog and digital signals in instrumentation and give an example of each.
Analog signals vary continuously within a range and represent physical quantities proportionally, such as a 4–20 mA current loop representing pressure. Digital signals have discrete levels or states, typically in binary form, like a Modbus communication protocol transmitting digital data between devices.
4. What are the key considerations when selecting an instrument for use in a hazardous area classified as Zone 1?
In a Zone 1 hazardous area, instruments must be certified for explosive atmospheres. Key considerations include using intrinsically safe or explosion-proof devices, proper enclosures, adherence to relevant standards (like ATEX or IECEx), temperature classification, and ensuring material compatibility to prevent ignition sources.
5. How do you determine the appropriate cable size for an instrumentation signal loop?
Cable size is determined based on current-carrying capacity, voltage drop, signal integrity, and installation environment. Calculations consider cable length, conductor resistance, permissible voltage drop, and electromagnetic interference. Adhering to electrical codes and standards ensures proper sizing for safe and effective operation.
6. Explain the function of a control valve positioner and why it is used in control systems.
A control valve positioner receives a control signal and adjusts the actuator to achieve the desired valve position. It ensures accurate and responsive control by compensating for factors like friction or pressure differentials. Positioners improve control loop performance by enhancing valve accuracy and stability.
7. What is a Fieldbus system in instrumentation, and what advantages does it offer over traditional wiring methods?
Fieldbus is a digital, two-way communication system connecting field devices and control systems on a single network. Advantages include reduced wiring complexity, enhanced data exchange capabilities, remote diagnostics, easier device integration, and improved system flexibility and scalability.
8. Describe the importance of grounding and shielding in instrumentation cabling.
Grounding and shielding protect instrumentation signals from electromagnetic interference (EMI) and ensure safety. Proper grounding provides a reference point and helps dissipate fault currents while shielding blocks external EMI from affecting signal integrity. This ensures accurate measurements and prevents signal degradation.
9. What information is typically included on an instrument data sheet?
An instrument data sheet includes specifications like instrument type, model, range, accuracy, materials of construction, process conditions (temperature, pressure), electrical requirements, certifications, mounting details, and any special features. It serves as a detailed specification for procurement and design.
10. How does a Programmable Logic Controller (PLC) differ from a Distributed Control System (DCS) in industrial automation?
A PLC is a ruggedized computer used for discrete control applications, handling high-speed logic operations. A DCS manages complex, continuous processes with multiple control loops, providing centralized control and monitoring. DCS systems offer higher-level functions like advanced control strategies and integrated operator interfaces.
11. Explain the concept of signal conditioning and why it is necessary for instrumentation systems.
Signal conditioning processes a sensor signal to make it suitable for further processing or display. This may include amplification, filtering, isolation, or conversion. It enhances signal quality, ensures compatibility with control systems, protects equipment from transients, and improves measurement accuracy.
12. What are the main differences between 2-wire and 4-wire transmitters?
A 2-wire transmitter uses the same two wires for both power supply and signal transmission, typically in a 4–20 mA loop. A 4-wire transmitter has separate pairs for power and signal, allowing for higher power consumption and improved performance but requiring more wiring.
13. In drafting, why is it important to adhere to standardized instrumentation symbols and notation?
Using standardized symbols ensures clear communication among engineers, designers, contractors, and operators. It reduces misinterpretation, facilitates international collaboration, and maintains consistency across documents. Standards like ISA S5.1 provide common definitions for symbols used in P&IDs and other diagrams.
14. What factors should be considered when selecting materials for instrumentation enclosures in corrosive environments?
Material selection should consider chemical compatibility, corrosion resistance, temperature range, mechanical strength, and compliance with environmental standards. Materials like stainless steel or specialized plastics prevent corrosion, ensure longevity, and maintain the integrity of the instrumentation in harsh conditions.
15. Describe the purpose of a marshaling cabinet in an instrumentation system.
A marshaling cabinet serves as an intermediate wiring point between field instruments and the control system. It organizes and groups signals simplifies wiring, allows for easier maintenance and troubleshooting, and provides a location for signal conditioning components like isolators and barriers.
16. How does a HART communicator function in configuring field instruments?
AA HART communicator uses the HART protocol to communicate digitally with smart field instruments over existing 4–20 mA analog loops. It allows technicians to configure, calibrate, and diagnose instruments remotely without interrupting the analog signal, enhancing efficiency and reducing downtime.
17. What is an instrument loop check, and why is it performed during commissioning?
An instrument loop check verifies the proper operation of each control loop from the field instrument through the wiring to the control system and back. It ensures correct installation, wiring integrity, signal accuracy, and appropriate system response, crucial for safe and reliable operation.
18. Explain the purpose of using redundant instrumentation in critical control systems.
Redundant instrumentation provides backup in case of failure, enhancing system reliability and safety. In critical applications, duplicate instruments, controllers, or communication paths ensure continuous operation, prevent downtime and mitigate risks associated with single-point failures.
19. What role does calibration play in maintaining instrumentation accuracy, and how often should it be performed?
Calibration adjusts an instrument to provide accurate measurements by comparing it against a known standard. Regular calibration accounts for drift, environmental effects, and wear. The frequency depends on the instrument type, usage, regulatory requirements, and manufacturer recommendations, often ranging from quarterly to annually.
20. Discuss the importance of following industry standards and codes in electrical instrumentation design.
Adhering to industry standards and codes ensures safety, reliability, and interoperability. It ensures compliance with legal and regulatory requirements, promotes best practices and provides design, installation, and maintenance guidelines. Standards from organizations like ISA, IEC, and NEC help maintain consistency and quality across projects.
Electrical Instrumentation Design and Drafting Interview Questions Answers - For Advanced
1. Explain the key differences between Intrinsic Safety (IS) and Explosion-Proof (XP) protection methods in hazardous area instrumentation design, and discuss when each method is preferred.
Intrinsic Safety (IS) limits electrical energy within devices to prevent ignition in hazardous areas, making it ideal for low-power instrumentation where live maintenance is advantageous. Explosion-proof (XP) encloses equipment in robust housings to contain any internal explosions. XP is preferred for high-power devices unsuitable for IS, whereas IS is favored for ease of maintenance and lower overall costs.
2. Describe the role of the HART communication protocol in smart instrumentation and how it integrates with traditional 4-20 mA current loops.
HART (Highway Addressable Remote Transducer) superimposes digital signals onto the standard 4-20 mA analog current loop, enabling two-way communication with smart instruments without disrupting the analog measurement. This integration allows for remote configuration, diagnostics, and enhanced data acquisition while maintaining compatibility with existing analog control systems.
3. In designing an instrument loop diagram, what considerations must be taken into account for grounding and shielding to minimize electrical noise?
Proper grounding involves single-point grounding to prevent ground loops, while shielding requires conductive enclosures or cable shields connected to the ground at one end to avoid noise induction. Careful separation of signal and power cables, using twisted pairs, and maintaining consistent grounding practices are crucial to minimize electromagnetic interference in instrument loops.
4. Discuss the importance of the Safety Integrity Level (SIL) in the selection of instrumentation and how it affects the design process.
SIL determines the required risk reduction for safety functions, guiding the selection of instruments with appropriate reliability and diagnostic capabilities. Higher SIL levels necessitate redundant systems, increased testing, and rigorous documentation. Incorporating SIL into design ensures compliance with safety standards like IEC 61508, impacting component choice, system architecture, and validation procedures.
5. Explain how a Foundation Fieldbus network differs from a traditional analog instrumentation network and its advantages in process control systems.
Foundation Fieldbus is a digital, bi-directional communication protocol that allows multiple instruments to share a single network segment, reducing wiring complexity. Unlike traditional 4-20 mA loops, it supports advanced diagnostics, device interoperability, and distributed control functions within field devices, leading to enhanced system flexibility, scalability, and improved operational efficiency.
6. Outline the process of performing a Hazard and Operability Study (HAZOP) in instrumentation design and its impact on safety and compliance.
A HAZOP systematically examines potential deviations in process parameters using guide words (e.g., "No," "More," "Less") to identify hazards. In instrumentation design, it evaluates how instrument failures or misconfigurations could lead to unsafe conditions. The process informs safety system requirements, ensures compliance with regulations, and enhances overall system reliability by mitigating risks.
7. What are the critical factors to consider when selecting a flow measurement technology for a process involving viscous, non-Newtonian fluids?
Key factors include fluid properties (viscosity, density), flow profile, and compatibility with non-Newtonian behavior. Technologies like Coriolis or positive displacement flowmeters are suitable due to their ability to handle high viscosities and provide accurate measurements regardless of flow regime changes. Installation constraints and maintenance requirements also influence technology selection.
8. Describe the procedure for calibrating a pressure transmitter and ensuring its accuracy in a process control application.
Calibration involves applying known pressure values across the transmitter's range and adjusting its output to match these standards. The procedure includes zero and span adjustments, linearity checks, and documenting results. Regular calibration ensures measurement accuracy, compensates for sensor drift, and maintains compliance with quality control and industry standards.
9. How does the implementation of redundancy in a Distributed Control System (DCS) enhance system reliability, and what are the design considerations?
Redundancy involves duplicating critical components like controllers, networks, and power supplies to provide failover capabilities. It enhances reliability by minimizing single points of failure. Design considerations include synchronization between redundant units, seamless switchover mechanisms, and increased system complexity. Proper testing and maintenance are essential to ensure redundancy functions as intended.
10. In drafting Piping and Instrumentation Diagrams (P&IDs), what are the conventions for representing instrumentation and control devices, and why are they important?
P&IDs use standardized symbols and tagging per ISA or ISO standards to represent instruments and controls. Conventions include specific shapes for devices, line types for signals, and consistent labeling. Adherence to these standards is crucial for clear communication among engineers, accurate construction, effective maintenance, and compliance with regulatory requirements.
Course Schedule
Jul, 2025 | Weekdays | Mon-Fri | Enquire Now |
Weekend | Sat-Sun | Enquire Now | |
Aug, 2025 | Weekdays | Mon-Fri | Enquire Now |
Weekend | Sat-Sun | Enquire Now |
Related Courses
Related Articles
- SAP BRIM Training & Certification Course - Unlocking New Avenues in Billing and Revenue Management
- Masters in Artificial Intelligence Online as a Safe and Refined Career Option
- Earn Business Analyst Certification Online: Find the Key Benefits
- Today 80% MNC Companies Recruit SAP Professionals
- A Guide to PEGA Training
Related Interview
- Distributed Control Systems ( DCS ) Interview Questions Answers
- Foxboro DCS Interview Questions Answers
- AZ-305: Designing Microsoft Azure Infrastructure Solutions Interview Questions Answers
- COMOS P&ID (COM-PID) Admin Training Interview Questions Answers
- SAP TM (Transportation Management) Interview Questions Answers
Related FAQ's
- Instructor-led Live Online Interactive Training
- Project Based Customized Learning
- Fast Track Training Program
- Self-paced learning
- In one-on-one training, you have the flexibility to choose the days, timings, and duration according to your preferences.
- We create a personalized training calendar based on your chosen schedule.
- Complete Live Online Interactive Training of the Course
- After Training Recorded Videos
- Session-wise Learning Material and notes for lifetime
- Practical & Assignments exercises
- Global Course Completion Certificate
- 24x7 after Training Support
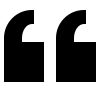