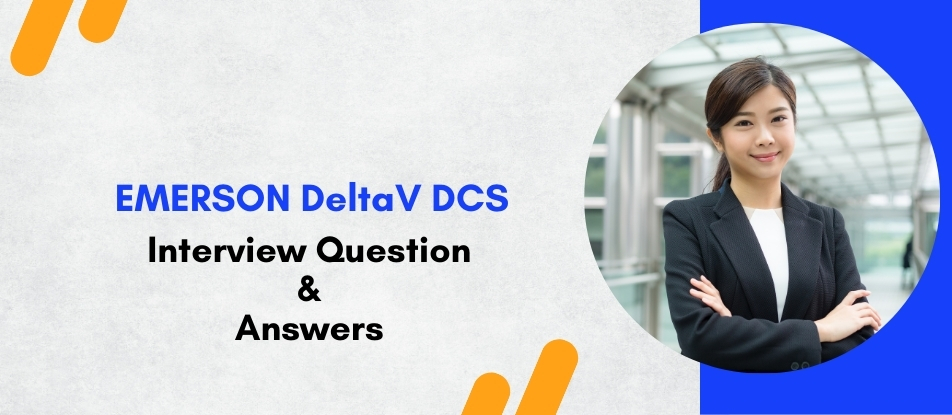
This Emerson DeltaV DCS training course is designed to equip automation professionals with comprehensive skills in configuring, operating, and maintaining the DeltaV Distributed Control System. The course covers system architecture, controller setup, CHARMs I/O, Control Studio programming, HMI development, alarm handling, and diagnostics. Through practical sessions and expert instruction, participants gain the confidence to manage complex process control environments using DeltaV technologies effectively and efficiently.
EMERSON DeltaV DCS Training Interview Questions Answers - For Intermediate
1. What is the DeltaV Explorer and what functions does it perform?
DeltaV Explorer is the central configuration and navigation tool used to manage the DeltaV system. It provides a tree-based view of all system components, including controllers, I/O, modules, devices, and network settings. Users can configure hardware, assign I/O channels, create control modules, and download configurations to the system. It also offers access to diagnostics, batch setup, and security settings.
2. What are modules in DeltaV and how are they categorized?
Modules in DeltaV represent the logical containers for control logic and are categorized into Control Modules (CMs) and Equipment Modules (EMs). Control Modules contain logic for process control, such as loops and interlocks, while Equipment Modules manage physical equipment like pumps, valves, and tanks. These modules enhance modular design, facilitate reuse, and simplify troubleshooting and maintenance.
3. How does DeltaV handle I/O calibration and testing?
DeltaV provides tools for calibrating and testing I/O channels during commissioning. Calibration can be done through DeltaV Explorer or AMS Device Manager, where you can apply simulated values, perform loop checks, and monitor live readings. This helps ensure signal accuracy and proper wiring before the system goes live. Diagnostic feedback confirms the health of sensors and wiring integrity.
4. Explain how interlocks are implemented in DeltaV.
Interlocks in DeltaV are implemented using logic within Control Modules, usually through function blocks like logical operators, comparators, and alarms. Interlock conditions are often tied to permissive states for starting or stopping equipment. Operators can view interlock statuses on HMI graphics. Using structured modules for interlocks ensures clarity, maintainability, and operational safety in automated systems.
5. What is the purpose of the DeltaV Historian?
The DeltaV Continuous Historian stores real-time process data, alarms, and events for analysis and reporting. It allows operators and engineers to view historical trends, detect anomalies, and generate performance reports. Data can be exported to external tools like Excel or integrated with PI systems. Historian settings include sampling rates, deadbands, and archiving durations.
6. How does DeltaV support Foundation Fieldbus communication?
DeltaV natively supports Foundation Fieldbus, a digital communication protocol that allows multi-variable field devices to connect via a single cable. Control can be distributed to the device level, reducing controller load. Fieldbus segments are configured using DeltaV Explorer, and function blocks from devices (like AI, PID) are integrated into control modules. It supports diagnostics and device parameter access.
7. What is a Node in DeltaV, and what types are there?
A Node in DeltaV refers to any hardware component connected to the control network. Common node types include Operator Stations (Workstations), Application Stations, Controllers, and I/O Subsystems. Each node has a unique node address and plays a specific role in the DCS ecosystem. Nodes are managed via DeltaV Explorer and can be monitored for diagnostics and performance.
8. Describe the process of downloading control strategies in DeltaV.
Downloading in DeltaV involves transferring control logic from the configuration database to the controllers and I/O modules. This is typically done from DeltaV Explorer after compiling modules. Downloads can be full or partial, and the system verifies controller availability and validates the configuration. Online downloads allow changes without stopping the process, ensuring continuous operations.
9. What are DeltaV Smart Switches and their role in the network?
DeltaV Smart Switches are industrial-grade, managed Ethernet switches specifically designed for DeltaV networks. They offer features like automatic device detection, traffic prioritization, diagnostics, and security configurations. They help ensure network health by isolating traffic, supporting redundancy, and providing alarms on port or communication failures. They are an essential part of the robust DeltaV control network.
10. What is AMS Device Manager, and how is it integrated with DeltaV?
AMS Device Manager is an asset management solution that integrates with DeltaV to monitor and configure smart field devices. It provides predictive diagnostics, calibration tools, device alerts, and audit trails. AMS helps reduce unplanned downtime by enabling proactive maintenance. It supports HART, Foundation Fieldbus, and WirelessHART devices and is accessible from engineering or application stations.
11. How does DeltaV facilitate alarm prioritization and rationalization?
DeltaV allows each alarm to be assigned a priority (High, Medium, Low) based on its impact on process safety, environment, or production. During configuration, engineers can perform alarm rationalization using criteria like consequence, time to respond, and operator action. Tools like Alarm Help provide detailed operator guidance, while alarm shelving and suppression help reduce nuisance alarms.
12. What is the DeltaV Virtual Studio?
DeltaV Virtual Studio is Emerson’s virtualization platform that allows users to deploy and manage virtual DeltaV workstations, controllers, and applications. It simplifies system design, testing, training, and development by reducing hardware needs. It supports templates, snapshots, and high availability setups. Virtual Studio helps in cost reduction, improved flexibility, and faster system deployment for large projects.
13. How are reports and trends generated in DeltaV?
Reports and trends are generated using the Continuous Historian and DeltaV Operate or DeltaV Live tools. Operators can create trend displays for real-time and historical data with multiple pens and time scales. Reports can be automated or manually generated and exported in standard formats. Trending helps in identifying process variations, improving diagnostics, and optimizing performance.
14. What are DeltaV control campaigns and when are they used?
Control campaigns in DeltaV are used to execute control actions across multiple loops or units based on a predefined schedule or trigger. Commonly used in batch or shutdown/startup operations, campaigns ensure coordinated and repeatable execution of changes like setpoint updates or mode changes. They enhance operational consistency and minimize manual intervention during repetitive tasks.
15. Explain how security patches and updates are managed in DeltaV systems.
Emerson provides validated Microsoft security patches and DeltaV updates to ensure cybersecurity and system stability. These patches are tested by Emerson before release and can be applied using Patch Management tools within the system. Updates should be applied during maintenance windows with proper backup and rollback plans. Patch management is essential for maintaining system compliance and security.
EMERSON DeltaV DCS Training Interview Questions Answers - For Advanced
1. How does DeltaV handle device-level integration using Foundation Fieldbus and what are the key benefits?
DeltaV fully supports Foundation Fieldbus, allowing smart field devices to connect and communicate digitally over a single twisted pair. This digital protocol enables multivariable communication, embedded control (e.g., PID in the field device), and advanced diagnostics. DeltaV assigns each device to a segment and allows configuration through DeltaV Explorer and AMS Device Manager. One of the key benefits is the reduction of wiring and I/O hardware, since multiple devices can share a segment. Fieldbus also facilitates better predictive maintenance due to rich diagnostic information directly from the devices. Control can be distributed—offloading the controller—and loop integrity is enhanced by precise, synchronized execution.
2. What mechanisms are in place for managing configuration changes and ensuring version control in DeltaV?
DeltaV provides robust configuration management through project files (.fhx, .exp), version history, and integrated change tracking. Engineers use DeltaV Explorer and Control Studio to build, modify, and save configuration files. The system supports online/offline modes and allows exporting/importing of modules, which can be archived with version stamps. User audit trails record who made what changes and when. For larger teams or projects, Emerson recommends versioning and documentation using electronic change management tools or integration with revision control systems. These practices ensure traceability, rollback capability, and regulatory compliance, especially in validated environments like pharmaceuticals.
3. How does the DeltaV system support SIL-rated safety applications in conjunction with SIS (Safety Instrumented Systems)?
While the core DeltaV system is designed for control, safety instrumented functions (SIFs) are handled by Emerson’s DeltaV SIS, which is TUV-certified up to SIL 3. It runs on separate logic solvers (LSs) that integrate tightly with DeltaV for unified engineering and monitoring but maintain safety-critical separation. DeltaV SIS supports cause-and-effect logic, trip diagnostics, bypass management, and safety reporting. The same AMS and historian tools can be used for asset diagnostics and event logging. Safety-critical paths are executed independently and validated per IEC 61511 and IEC 61508 standards. Integration with basic process control allows clear visualization of safety states and facilitates comprehensive shutdown strategies.
4. How is inter-controller communication optimized for performance and reliability in DeltaV?
Inter-controller communication in DeltaV is achieved through deterministic peer-to-peer data referencing over the DeltaV Control Network. The system uses an internal communication protocol that is optimized for minimal latency and includes buffering mechanisms to ensure smooth data transfer. Each reference is defined in the module and verified for link integrity. The communication is event-driven, reducing unnecessary traffic. In redundant controller setups, the system synchronizes peer data for both active and standby controllers. Robust diagnostics are available to detect stale data, broken references, or failed communication. This architecture supports complex, multi-unit processes that require real-time coordination between multiple control areas.
5. What best practices are followed in designing scalable and maintainable DeltaV control strategies?
Designing scalable control strategies in DeltaV involves modular programming, consistent naming conventions, and template-based development. Engineers use parameterized modules, function block libraries, and equipment modules to simplify configuration and reuse logic. Aliasing and structured parameter access improve readability. Logical segregation between control, interlocks, and sequences enhances clarity and testing. Thorough commenting, signal description, and documentation ensure maintainability. Strategies should also be load-tested to avoid scan overruns. During commissioning, simulation blocks can be used to validate logic without hardware dependencies. Adhering to these practices ensures the system is easier to scale, troubleshoot, and transfer between teams or sites.
6. How does DeltaV implement redundancy across system components beyond the controller?
DeltaV implements redundancy not only in controllers but also across power supplies, communication networks (dual NICs and switches), and I/O subsystems. Redundant CHARMs I/O cards and redundant Smart I/O busses provide fail-safe communication with field devices. Application stations and operator workstations can also be deployed in redundant pairs for visualization reliability. Network redundancy is achieved using ring topologies or redundant Ethernet. Diagnostics tools continuously monitor redundancy health, and automatic failover ensures that even if one component fails, the system continues to operate without process impact. This holistic redundancy design supports mission-critical applications requiring 24/7 uptime.
7. What strategies does DeltaV use for time synchronization and why is it important?
Time synchronization in DeltaV is crucial for aligning events, alarms, and historical data across distributed components. DeltaV employs a dedicated Time Master (often the Application Station or Domain Controller), and all nodes synchronize via Network Time Protocol (NTP). Controllers, workstations, historians, and SIS nodes maintain synchronized timestamps, ensuring accurate sequence of events and consistent trending. This synchronization is especially important in batch operations, compliance auditing (e.g., CFR 21 Part 11), and incident investigation. Tools are provided to monitor synchronization status, and deviation alerts can trigger alarms or corrective actions.
8. Explain the use of electronic marshalling in brownfield project migrations using DeltaV.
In brownfield projects, electronic marshalling with CHARMs offers tremendous flexibility and efficiency. Traditional systems require rigid I/O mapping and rewiring during migrations. With CHARMs, existing field wiring is connected to terminal blocks without concern for I/O channel types. During the migration, engineers assign signal types electronically, which reduces physical rewiring and allows for staged, safe cutovers. This modular and flexible approach supports phased migrations, shortens downtime, and enables easier FAT and SAT execution. It also aids in reverse-engineering legacy logic, making the transition smoother and less error-prone.
9. How does DeltaV’s Control Studio manage PID tuning and optimization?
DeltaV’s Control Studio offers integrated PID loop tuning tools, including step response, autotune, and manual tuning methods. Engineers can observe loop responses in real-time and adjust gain, reset, and derivative values interactively. Simulation mode can be used for safe offline tuning, and live modules provide trending, mode control (AUTO, MAN, CAS), and alarm visibility. For advanced optimization, DeltaV integrates with Emerson’s Plantweb Advisor or embedded advanced control tools like DeltaV InSight. These tools analyze loop performance, identify poorly tuned loops, and recommend tuning parameters, helping maximize process stability, efficiency, and product quality.
10. What is the role of the DeltaV Application Station, and what services can it host?
The Application Station in DeltaV serves as a multifunctional node for hosting essential services like Continuous Historian, Batch Executive, OPC Servers, and custom applications. It acts as the data bridge to third-party systems like ERP or MES and runs advanced control applications, report generators, and specialized scripts. It supports web-based clients, SQL connectivity, and integration with external historians like PI. Redundant Application Stations can be configured for high availability. This centralization simplifies architecture, reduces hardware footprint, and enhances system performance by offloading tasks from operator workstations.
11. How does DeltaV assist with operator situational awareness and abnormal situation management (ASM)?
DeltaV incorporates the ASM Consortium's design principles to enhance situational awareness. This includes high-performance HMI graphics with minimalist color schemes, alarm prioritization, and trend integration. Features like dynamic faceplates, graphical interlocks, and process overview screens help operators understand plant conditions quickly. Alarm flood suppression, diagnostic displays, and process navigation tools improve decision-making under stress. Operator training simulators (OTS) built using DeltaV Simulate Pro also help operators prepare for abnormal scenarios. These strategies reduce human error and improve response during critical situations.
12. Describe the implementation of dynamic parameterization in DeltaV and its application in batch processes.
Dynamic parameterization allows values such as setpoints, limits, or phase parameters to be defined at runtime, enabling flexibility in operations. In batch applications, recipe parameters are passed dynamically to Batch Control Modules (BCMs) or equipment modules. This reduces hardcoding and allows the same logic to be reused across different products or campaigns. Parameters can be sourced from batch records, operator entries, or external systems. Dynamic parameters enhance modularity, facilitate recipe management, and improve system adaptability to changing production needs.
13. How does DeltaV handle system backup and disaster recovery?
DeltaV provides backup tools that allow full and incremental backups of configuration databases, graphics, module files, historian data, and system logs. Regular backups can be scheduled and stored to secure locations or mirrored servers. In the event of failure, system recovery involves restoring controller configurations, application stations, and operator stations using validated backups. Emerson recommends following a validated recovery plan and storing backups both locally and offsite. DeltaV Virtual Studio further simplifies disaster recovery by using snapshots and templates for fast restoration of virtualized systems.
14. What’s the importance of DeltaV Smart Switches, and how do they differ from commercial switches?
DeltaV Smart Switches are hardened, managed switches specifically engineered for use in control networks. They differ from commercial switches by offering automatic device detection, bandwidth reservation, port security, diagnostics, and integrated management with DeltaV Diagnostics. These switches prioritize control traffic and support network redundancy protocols. Smart Switches alert operators and engineers to port failures, unauthorized connections, or bandwidth anomalies, thereby ensuring network reliability and simplifying troubleshooting. They play a key role in enforcing Emerson’s recommended secure and deterministic network architecture.
15. How are DeltaV systems validated in regulated industries like pharmaceuticals?
Validation in regulated industries is achieved by following structured lifecycle methodologies such as GAMP 5. DeltaV provides built-in features like audit trails, user access control, electronic signatures, and batch record generation. During qualification, documents like URS, FDS, HDS, IQ, OQ, and PQ are developed, and tests are executed to ensure system compliance. Emerson offers validation templates and services that align with FDA 21 CFR Part 11 requirements. Continuous monitoring and change management features ensure the system remains in a validated state even during upgrades or configuration changes.
Course Schedule
Apr, 2025 | Weekdays | Mon-Fri | Enquire Now |
Weekend | Sat-Sun | Enquire Now | |
May, 2025 | Weekdays | Mon-Fri | Enquire Now |
Weekend | Sat-Sun | Enquire Now |
Related Courses
Related Articles
Related Interview
Related FAQ's
- Instructor-led Live Online Interactive Training
- Project Based Customized Learning
- Fast Track Training Program
- Self-paced learning
- In one-on-one training, you have the flexibility to choose the days, timings, and duration according to your preferences.
- We create a personalized training calendar based on your chosen schedule.
- Complete Live Online Interactive Training of the Course
- After Training Recorded Videos
- Session-wise Learning Material and notes for lifetime
- Practical & Assignments exercises
- Global Course Completion Certificate
- 24x7 after Training Support
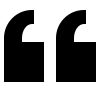