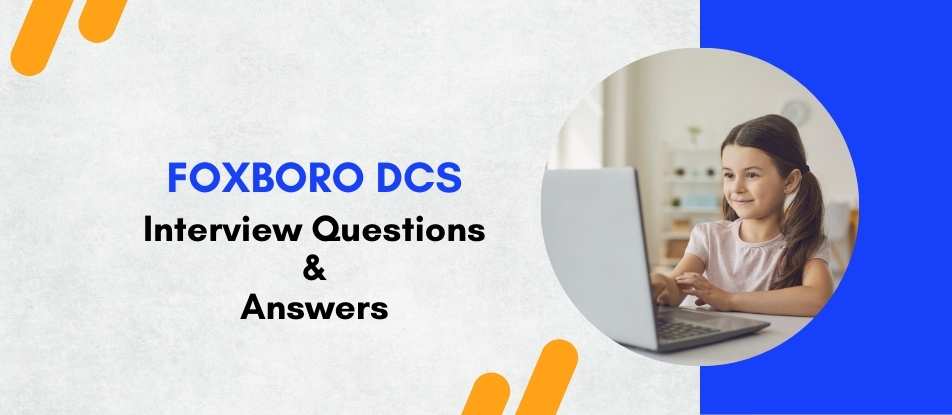
Foxboro DCS Training is designed to provide in-depth knowledge of Distributed Control Systems, focusing on configuration, operation, and advanced control techniques. Participants will learn system architecture, redundancy management, alarm handling, and integration with field devices. Through practical exercises and real-world scenarios, this course enhances skills in process optimization, troubleshooting, and ensuring system reliability. Ideal for engineers and technicians, it prepares professionals for efficient management of complex industrial processes.
Foxboro DCS Interview Questions Answers - For Intermediate
1. What distinguishes a Distributed Control System (DCS) like Foxboro from traditional automation systems?
A Distributed Control System (DCS) like Foxboro is unique because it decentralizes control across multiple nodes or controllers, ensuring better system reliability and scalability. Unlike traditional automation systems, which often rely on centralized control, Foxboro DCS spreads control logic across various field control processors (FCPs). This architecture minimizes the risk of system-wide failures, improves redundancy, and enables seamless integration with complex industrial processes.
2. How does the Foxboro DCS achieve real-time process control?
Foxboro DCS achieves real-time process control through its high-speed communication networks and powerful processors. Field Control Processors continuously gather data from sensors and execute control algorithms to adjust process variables in milliseconds. The system’s design ensures that time-critical operations are not delayed, maintaining process stability and efficiency even under demanding conditions.
3. Can you explain the concept of redundancy in Foxboro DCS?
Redundancy in Foxboro DCS is designed to enhance system reliability by duplicating critical components. For instance, redundant controllers, power supplies, and communication networks ensure that if one element fails, its backup automatically takes over without interrupting operations. This feature is vital in industries where downtime can lead to significant financial losses or safety risks.
4. What are the typical applications of Foxboro DCS in industrial settings?
Foxboro DCS is used in various industrial sectors, including oil and gas, power generation, pharmaceuticals, and chemicals. It excels in managing continuous processes such as refining crude oil, generating electricity in power plants, or producing bulk chemicals. The system’s ability to handle complex process variables and ensure precise control makes it indispensable in these industries.
5. How does Foxboro DCS handle alarms and notifications?
Foxboro DCS employs an advanced alarm management system to notify operators about abnormal conditions. Alarms are prioritized based on their severity, helping operators address critical issues promptly. The system also includes features like alarm suppression and historical logging, which aid in analyzing recurring problems and reducing alarm fatigue.
6. What is the role of Advanced Process Control (APC) in Foxboro DCS?
Advanced Process Control (APC) in Foxboro DCS enhances traditional control by incorporating predictive algorithms and optimization techniques. These advanced features improve process efficiency, reduce energy consumption, and minimize variability. For example, APC might use model-based predictive control to anticipate changes in process conditions and adjust operations proactively.
7. How is data visualization implemented in Foxboro DCS?
Data visualization in Foxboro DCS is facilitated through its intuitive Human-Machine Interface (HMI). Operators can view process trends, monitor real-time data, and interact with graphical representations of plant systems. These visual tools make it easier to identify issues and optimize performance, even in complex industrial environments.
8. What are the key security features of Foxboro DCS?
Foxboro DCS prioritizes cybersecurity with features like role-based access control, which restricts system access to authorized personnel. It also includes secure communication protocols and audit trails to track system changes. These measures protect the system from unauthorized access and cyber threats, ensuring the integrity of critical operations.
9. How does Foxboro DCS integrate with third-party systems?
Foxboro DCS supports integration with third-party systems using standard communication protocols like Modbus, OPC, and Ethernet/IP. This interoperability allows it to communicate seamlessly with devices and systems from other manufacturers, enabling comprehensive process control and data exchange across the enterprise.
10. What is the significance of process historians in Foxboro DCS?
Process historians in Foxboro DCS store time-stamped process data, providing a comprehensive record of plant operations. This data is invaluable for trend analysis, predictive maintenance, and compliance reporting. By analyzing historical data, operators can identify inefficiencies and implement changes to improve overall process performance.
11. How does Foxboro DCS manage scalability in expanding plants?
Foxboro DCS is designed for scalability, allowing users to add controllers, I/O modules, and workstations as their plants expand. The system’s modular architecture ensures that new components integrate seamlessly without requiring major reconfigurations. This flexibility makes it suitable for industries with evolving production needs.
12. Can you describe the typical workflow for creating control strategies in Foxboro DCS?
Creating control strategies in Foxboro DCS typically involves using the Foxboro Control Editor, a graphical tool for configuring control logic. Engineers design control loops by defining inputs, outputs, and algorithms, such as PID control. The configured strategies are then tested in a simulation environment before being deployed to the field.
13. What challenges might arise when implementing Foxboro DCS, and how can they be addressed?
Challenges in implementing Foxboro DCS may include compatibility issues with existing systems, a steep learning curve for new users, and initial setup costs. These challenges can be addressed through thorough planning, comprehensive training for operators and engineers, and leveraging Foxboro’s integration capabilities to ensure smooth adoption.
14. How does Foxboro DCS contribute to operational efficiency?
Foxboro DCS contributes to operational efficiency by automating repetitive tasks, minimizing human error, and optimizing process variables. Its advanced control algorithms ensure processes run at peak performance, reducing energy consumption and raw material waste. Real-time monitoring also enables quick responses to issues, further enhancing efficiency.
15. What advancements have been made in the latest versions of Foxboro DCS?
Recent advancements in Foxboro DCS include enhanced cybersecurity measures, improved HMI features, and support for cloud-based analytics. The system now integrates more seamlessly with IoT devices, providing deeper insights into plant operations. These updates make it more adaptable to modern industrial challenges, such as sustainability and data-driven decision-making.
Foxboro DCS Interview Questions Answers - For Advanced
1. How does Foxboro DCS support high-speed data acquisition, and why is this critical in real-time operations?
Foxboro DCS uses high-speed Ethernet-based communication protocols and advanced Field Control Processors (FCPs) to acquire data from sensors and devices in milliseconds. This rapid data acquisition is critical in maintaining real-time process control, especially in industries like oil and gas, where slight deviations in parameters can lead to catastrophic outcomes. The system’s architecture ensures minimal latency in transmitting data from the field to operator workstations, enabling timely responses to dynamic process changes. Advanced buffering and priority mechanisms prevent data loss even under heavy network loads.
2. What challenges are associated with upgrading legacy Foxboro DCS systems, and how can they be addressed?
Upgrading legacy Foxboro DCS systems poses challenges such as compatibility with existing hardware, downtime during migration, and operator retraining. These challenges can be addressed by employing phased migration strategies that replace components incrementally while maintaining operational continuity. Middleware can bridge compatibility gaps between old and new systems, enabling data exchange. Extensive pre-testing in simulation environments minimizes risks during deployment, while operator training ensures that staff can utilize new features effectively.
3. How is advanced control functionality, such as model predictive control (MPC), implemented in Foxboro DCS?
Model Predictive Control (MPC) in Foxboro DCS is implemented using advanced algorithms that predict future process behaviors based on mathematical models. MPC takes into account constraints, disturbances, and desired outcomes to calculate optimal control actions over a predictive horizon. The integration of MPC in Foxboro allows operators to handle complex, multivariable systems more efficiently than traditional PID controllers. Applications include reducing energy consumption in chemical processes or optimizing throughput in manufacturing.
4. What is the role of redundancy in Foxboro DCS power supplies, and how does it enhance reliability?
Foxboro DCS employs redundant power supplies to ensure uninterrupted operation in case of a power failure. These power supplies are designed to switch over seamlessly when a fault occurs in the primary unit, maintaining continuous power to critical components like FCPs and workstations. This redundancy is vital for high-reliability industries, where even brief power interruptions could result in significant safety hazards or financial losses. The system also features monitoring tools to detect and alert operators about power anomalies.
5. Explain how Foxboro DCS enables predictive maintenance in industrial applications.
Foxboro DCS integrates predictive maintenance by analyzing historical and real-time data to identify patterns that indicate potential equipment failures. The system uses advanced diagnostics and algorithms to monitor asset health, flagging issues such as wear and tear, misalignments, or temperature anomalies. Operators can schedule maintenance activities based on these insights, reducing unplanned downtime and extending equipment lifecycles. This approach not only lowers operational costs but also enhances overall system reliability.
6. How does Foxboro DCS support integration with cloud-based platforms, and what are the benefits?
Foxboro DCS supports integration with cloud-based platforms through secure APIs and communication protocols like OPC UA. This integration allows for centralized data storage, remote monitoring, and advanced analytics powered by machine learning algorithms. Benefits include improved operational visibility, scalability, and access to powerful predictive tools that help optimize performance. Cloud connectivity also enables multi-site collaboration, where data from different plants can be analyzed collectively for benchmarking and strategic decision-making.
7. How does Foxboro DCS manage complex I/O configurations, and what features ensure scalability?
Foxboro DCS manages complex I/O configurations by supporting a wide range of analog and digital I/O modules, as well as smart devices using communication protocols like HART and FOUNDATION Fieldbus. Its modular I/O design allows for easy scalability; new modules can be added as the plant grows without disrupting existing operations. Features like auto-discovery and hot-swapping further simplify I/O management, enabling engineers to make real-time adjustments to the configuration.
8. Discuss the importance of time synchronization in Foxboro DCS.
Time synchronization in Foxboro DCS ensures that all system components, including controllers, I/O modules, and workstations, operate on a unified time reference. This synchronization is critical for accurate data logging, event sequencing, and alarm analysis. The system typically uses NTP (Network Time Protocol) to maintain precise timing across distributed nodes. Without proper synchronization, discrepancies in time-stamped data could lead to incorrect diagnostics and compromised operational decisions.
9. What makes Foxboro DCS an ideal solution for critical processes in industries like oil and gas?
Foxboro DCS is ideal for critical processes in industries like oil and gas due to its high reliability, redundancy features, and advanced control capabilities. The system’s ability to handle complex, continuous processes with minimal latency ensures stability and safety. Its fault-tolerant design and compliance with industry standards like ISA/IEC 62443 for cybersecurity provide robust protection against system failures and cyber threats. Additionally, its scalability and real-time analytics enable operators to optimize production and respond quickly to dynamic market demands.
10. How does Foxboro DCS facilitate operator training and skill development?
Foxboro DCS includes simulation tools that allow operators to practice handling real-world scenarios in a virtual environment. These tools replicate actual plant conditions, enabling operators to gain experience without risking disruptions to live processes. Additionally, the system offers intuitive HMIs and customizable dashboards, making it easier for operators to understand and interact with the system. Comprehensive documentation and training modules further support skill development, ensuring operators are well-prepared to manage complex processes.
11. Explain how Foxboro DCS achieves data redundancy and what its benefits are.
Data redundancy in Foxboro DCS is achieved by storing process data across multiple locations, such as redundant historians or mirrored databases. This ensures that even if one data repository fails, critical information remains accessible. Benefits of data redundancy include improved system resilience, faster recovery times, and uninterrupted access to historical data for analysis and reporting. It is particularly crucial in industries where data loss could compromise regulatory compliance or operational safety.
12. How does Foxboro DCS address the challenges of managing large-scale distributed systems?
Foxboro DCS manages large-scale distributed systems through its hierarchical architecture, where Field Control Processors handle local control tasks while workstations provide centralized monitoring and management. Its high-speed communication network ensures efficient data transfer across distributed nodes, while advanced software tools enable operators to oversee and troubleshoot the entire system from a single interface. Scalability features allow the system to grow with operational needs, ensuring it remains effective in managing even the most complex plants.
13. What is the significance of advanced alarm rationalization in Foxboro DCS?
Advanced alarm rationalization in Foxboro DCS involves prioritizing, suppressing, and categorizing alarms to reduce operator overload and improve response times. By eliminating nuisance alarms and focusing on critical issues, the system ensures that operators can act promptly during emergencies. Features like dynamic alarm thresholds and historical alarm analysis further enhance the system’s effectiveness, enabling continuous improvement in alarm management strategies.
14. How does Foxboro DCS support multi-site operations and centralized management?
Foxboro DCS supports multi-site operations by enabling centralized monitoring and control through cloud-based solutions and secure remote access. Operators can oversee multiple plants from a unified dashboard, gaining real-time visibility into each site’s performance. Centralized management streamlines decision-making, resource allocation, and compliance reporting, ensuring consistency across operations. The system’s ability to integrate with enterprise-level tools like ERP further enhances its capability for multi-site coordination.
15. What are the key factors to consider when implementing advanced cybersecurity in Foxboro DCS?
Implementing advanced cybersecurity in Foxboro DCS requires a multi-layered approach. Key factors include deploying firewalls, intrusion detection systems, and secure communication protocols like OPC UA. Role-based access control and multi-factor authentication are critical for limiting unauthorized access. Regular updates and patches ensure protection against emerging threats, while continuous monitoring and audit trails provide visibility into system activity. Training personnel on cybersecurity best practices is equally important, as human error remains a significant vulnerability in industrial systems.
Course Schedule
Jul, 2025 | Weekdays | Mon-Fri | Enquire Now |
Weekend | Sat-Sun | Enquire Now | |
Aug, 2025 | Weekdays | Mon-Fri | Enquire Now |
Weekend | Sat-Sun | Enquire Now |
Related Courses
Related Articles
Related Interview
Related FAQ's
- Instructor-led Live Online Interactive Training
- Project Based Customized Learning
- Fast Track Training Program
- Self-paced learning
- In one-on-one training, you have the flexibility to choose the days, timings, and duration according to your preferences.
- We create a personalized training calendar based on your chosen schedule.
- Complete Live Online Interactive Training of the Course
- After Training Recorded Videos
- Session-wise Learning Material and notes for lifetime
- Practical & Assignments exercises
- Global Course Completion Certificate
- 24x7 after Training Support
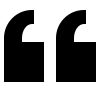