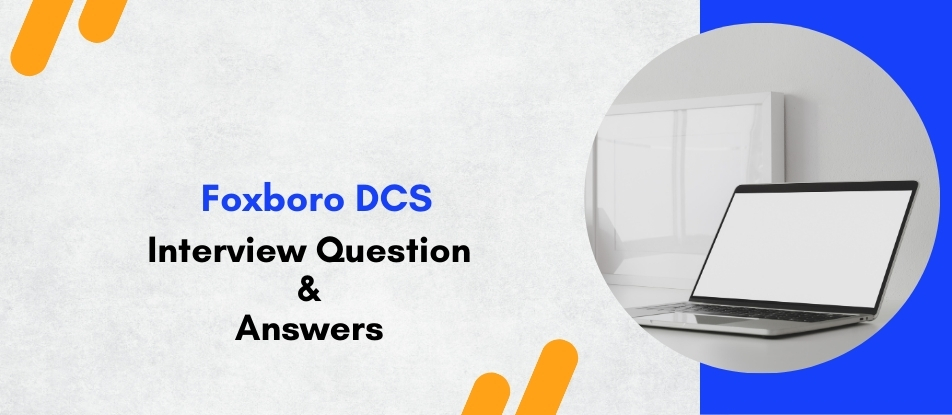
Foxboro DCS Training provides comprehensive instruction on the architecture, configuration, and operation of the Foxboro Distributed Control System by Schneider Electric. This course covers control strategies, FBMs, CPs, HMI, redundancy, and integration techniques. Participants gain hands-on experience in building and managing industrial automation systems with high reliability. Ideal for automation professionals, it prepares learners to handle real-world process control challenges in sectors like oil & gas, power, and manufacturing.
Foxboro DCS Training Interview Questions Answers - For Intermediate
1. What is the significance of the Foxboro DCS Communication Bus?
The Foxboro DCS Communication Bus, often based on Ethernet or Control Network protocols, is the backbone for data exchange between the controllers, workstations, and I/O modules. It ensures real-time, deterministic communication and supports redundancy to maintain system availability during network failures.
2. How does Foxboro DCS handle firmware updates and system upgrades?
Firmware updates and system upgrades in Foxboro DCS are managed through a controlled and phased process using the System Manager. These updates are tested in a staging environment and deployed during scheduled maintenance windows to minimize disruption. Foxboro also offers backward compatibility to protect previous configurations.
3. What are the key components of the Foxboro DCS architecture?
The main components include Control Processors (CPs), Fieldbus Modules (FBMs), Human-Machine Interfaces (HMIs), Engineering Workstations (EWS), Application Workstations, and the Historian. Together, these components enable scalable, redundant, and real-time process automation and data visualization.
4. Explain the use of redundant FBMs in Foxboro DCS.
Redundant FBMs are used to ensure uninterrupted field communication. In a redundant configuration, a backup FBM mirrors the primary one and takes over automatically upon failure. This setup eliminates single points of failure, improving system resilience and uptime.
5. What is FoxDraw and how is it used?
FoxDraw is the graphical interface design tool in the Foxboro DCS suite. It enables engineers to create process graphics, control displays, and operator panels. These graphical interfaces provide real-time process visualization, enhancing operator awareness and interaction.
6. How does Foxboro DCS support safety in industrial operations?
Foxboro DCS supports safety through features such as interlock logic, fail-safe configurations, alarm management, and diagnostics. It also integrates with Safety Instrumented Systems (SIS) for critical applications, ensuring plant safety and regulatory compliance.
7. Describe the procedure for configuring an analog input in Foxboro DCS.
To configure an analog input, the engineer selects the appropriate FBM type (e.g., FBM201), assigns a tag name, defines scaling parameters (engineering units, range), and maps it to the control strategy using the Control Editor. The signal can then be monitored and used in logic.
8. What is the difference between Foxboro DCS and a PLC system?
While both are used for automation, Foxboro DCS is ideal for large, complex, and continuous processes due to its distributed architecture, higher redundancy, and superior data management. PLCs are typically used in smaller, discrete automation systems with faster cycle times and less complexity.
9. What types of redundancy can be implemented in a Foxboro DCS setup?
Foxboro DCS supports multiple redundancy levels: Controller Redundancy, Power Supply Redundancy, Communication Redundancy, FBM Redundancy, and Network Redundancy. This multi-layered approach enhances fault tolerance and system uptime across all operational layers.
10. How are trends and reports generated in Foxboro DCS?
Trends and reports are generated using tools like FoxView and the Historian, which provide real-time and historical trending capabilities. Operators can define parameters, sampling rates, and durations, then export data into formats like CSV or PDF for analysis and compliance documentation.
11. What is EcoStruxure and how does it relate to Foxboro DCS?
EcoStruxure is Schneider Electric’s IoT-enabled platform that connects operational technology (OT) with IT. Foxboro DCS integrates seamlessly into EcoStruxure, allowing advanced analytics, cloud connectivity, predictive maintenance, and enterprise-wide optimization for industrial facilities.
12. What is a Control Block in Foxboro DCS?
A Control Block in Foxboro is a software element used in creating control strategies. Examples include PID, comparator, integrator, and logic blocks. These blocks are interconnected to create a visual representation of the control logic, which the controller executes continuously.
13. How do you troubleshoot communication failures in Foxboro DCS?
Troubleshooting involves checking the status of FBMs and CPs via diagnostic tools, verifying network cables, inspecting LED indicators, and reviewing system alarms. Tools like the System Manager and Event Logger provide real-time and historical data to isolate and resolve issues.
14. Can Foxboro DCS be virtualized?
Yes, engineering and HMI workstations in Foxboro DCS can be hosted on virtual machines, especially for testing and simulation purposes. However, core control hardware like CPs and FBMs still require physical infrastructure to interface with field devices and maintain real-time control integrity.
15. What types of I/O signals are supported by Foxboro DCS?
Foxboro DCS supports a wide range of I/O signals including analog input/output, digital input/output, thermocouple, RTD, pulse, and HART-enabled signals. This versatility allows it to accommodate different sensor and actuator types across industries.
Foxboro DCS Training Interview Questions Answers - For Advanced
1. How does Foxboro DCS manage time synchronization across its distributed components
Foxboro DCS uses Network Time Protocol (NTP) servers to synchronize time across all system components, including Control Processors (CPs), Fieldbus Modules (FBMs), operator workstations, and historians. Accurate time synchronization is crucial for event logging, data integrity, and sequence-of-events (SOE) recording. Each system element fetches timestamps from a centralized time server, ensuring that logs, trends, and alarms from different nodes align perfectly. This synchronization is vital during troubleshooting and post-event analysis, especially in high-integrity systems where process sequence and timing define root cause and impact analysis.
2. What is the significance of Sequence of Events (SOE) recording in Foxboro DCS?
SOE recording allows Foxboro DCS to capture high-resolution event data with precise timestamps, often in milliseconds. This feature is essential in safety-critical applications where diagnosing the exact sequence of system alarms, shutdowns, and operator actions can determine root causes. SOE works in conjunction with time-synchronized FBMs and controllers, recording changes in digital input/output states or control transitions. These records are stored in the Historian and can be analyzed through dedicated tools. This enhances system troubleshooting, facilitates audits, and improves operational safety by validating control logic and operator responses.
3. Explain how Foxboro DCS supports scalability for large enterprises with geographically distributed assets.
Foxboro DCS is highly scalable, allowing deployment from small standalone units to large enterprise-wide systems. It can be implemented in a hierarchical architecture—local DCS instances at plant levels integrated with a central monitoring or operations center. Communication over wide-area networks (WANs) is secured and structured using segmented architectures, remote access configurations, and redundant communications. Centralized historians and asset monitoring applications can aggregate data from distributed systems, enabling global visibility and performance benchmarking across multiple sites. This scalability is critical for multinational enterprises seeking standardized operations and unified control strategies.
4. What is the use of EcoStruxure Control Expert – DCS within the Foxboro ecosystem?
EcoStruxure Control Expert – DCS is an engineering and configuration environment tailored for Foxboro systems. It simplifies programming, deployment, and lifecycle management of control strategies. The tool provides a modern interface with drag-and-drop capabilities, function block design, simulation environments, and library management. It supports collaborative engineering, revision control, and modular deployment, reducing configuration errors and engineering time. Integration with the broader EcoStruxure architecture enables seamless interaction between DCS, PLC, SCADA, and cloud analytics, empowering users to develop unified and interoperable automation strategies.
5. How does Foxboro DCS ensure system availability during maintenance operations?
Foxboro DCS supports online configuration changes and module hot-swapping, allowing most maintenance tasks to be performed without system shutdowns. Redundant configurations of controllers, power supplies, and FBMs ensure that if one component is taken offline for maintenance, its backup continues operating without process interruption. Moreover, diagnostic tools within the System Manager provide real-time health monitoring and predictive alerts, enabling proactive maintenance. This approach minimizes downtime, improves mean time between failures (MTBF), and allows for planned maintenance without compromising process continuity.
6. Describe the architecture and function of the Foxboro Control Network.
The Control Network in Foxboro DCS is an Ethernet-based communication backbone connecting controllers, I/O modules, HMIs, engineering workstations, and data servers. It supports deterministic and non-deterministic communication, depending on configuration. Critical control messages are prioritized using quality-of-service (QoS) and VLAN segmentation. The network architecture often includes redundant switches and links to ensure availability. By using standard Ethernet technologies, the Control Network allows high-speed communication and easy integration with third-party systems and industrial IT infrastructure.
7. How are user roles and privileges managed in Foxboro DCS to ensure secure access?
User roles in Foxboro DCS are managed through a role-based access control (RBAC) system. Each user is assigned a role (e.g., operator, engineer, administrator), with specific access rights to view, modify, or configure system components. Password policies, session timeouts, and audit logs further enhance security. These roles can be integrated with enterprise Active Directory for centralized management and compliance. All activities are logged, ensuring traceability and accountability—a critical feature in regulated industries like pharmaceuticals or energy.
8. What types of diagnostics are available in Foxboro DCS and how do they support troubleshooting?
Foxboro DCS offers extensive diagnostics at hardware, software, and network levels. FBMs and CPs continuously monitor parameters like temperature, voltage, communication health, and loop status. Operators can access diagnostic summaries through HMIs or engineering tools, which display status in intuitive dashboards. The system also provides logs for alarm floods, configuration errors, and communication drops. These diagnostics help maintenance teams quickly isolate and resolve faults, ensuring system availability and reducing Mean Time to Repair (MTTR).
9. Explain how predictive maintenance is supported in Foxboro DCS.
Predictive maintenance in Foxboro DCS is enabled through continuous data acquisition, analytics, and integration with asset performance management (APM) tools. HART-enabled FBMs allow the system to gather diagnostic information from field instruments like valve stroke count, sensor drift, or device temperature. This data is analyzed using trend logic or integrated analytics platforms. Maintenance personnel receive early warnings about potential failures, enabling them to plan repairs before equipment breakdown occurs. This reduces unplanned downtime and extends equipment life.
10. What are the steps for migrating from a legacy Foxboro I/A Series system to the latest Foxboro DCS platform?
Migration from I/A Series to the modern Foxboro DCS platform follows a structured path. It starts with system assessment, followed by hardware compatibility checks and software upgrade planning. Existing control strategies and graphics are evaluated for portability using Foxboro's migration tools. A test environment is created to validate configurations before go-live. Data and alarm configurations are replicated, and system redundancy is tested. Schneider Electric provides migration services that ensure minimal downtime and safeguard historical data. The result is a modernized, more secure, and performance-optimized control system.
11. How does Foxboro DCS handle large volumes of real-time data from field instruments?
Foxboro DCS is designed to handle large data volumes through high-speed, distributed data acquisition systems and optimized communication protocols. FBMs collect analog, digital, and HART data, preprocess it locally, and transmit only meaningful values using compression and deadbanding. The historian stores this data efficiently for retrieval. Control Processors use prioritized task management to process critical control loops first. This combination of distributed processing, efficient data handling, and scalable historian architecture allows Foxboro to manage thousands of I/O points without latency.
12. What are the benefits of using Foundation Fieldbus in Foxboro DCS environments?
Foundation Fieldbus offers a digital, two-way communication protocol that enables smart devices to send real-time data, diagnostics, and alarms. When used with Foxboro DCS, it reduces wiring, supports device interoperability, and improves loop diagnostics. Each Fieldbus segment can host multiple devices, which execute control logic locally, offloading the central processor. This distributed intelligence increases reliability and improves performance. Integration with asset management systems further enhances device lifecycle management and maintenance planning.
13. How does Foxboro DCS ensure compliance in regulated industries like pharma or food processing?
Foxboro DCS supports compliance through features like electronic records and signatures (21 CFR Part 11), audit trails, and batch tracking. The system captures and stores all changes with timestamped logs, user identification, and justification. Batch processing complies with ISA-88, and alarm management aligns with ISA-18.2. The historian enables traceability, while integration with laboratory or quality systems ensures product consistency. These features collectively help maintain compliance with FDA, EMA, and other global regulatory frameworks.
14. Describe how Foxboro DCS supports multi-site remote operations and monitoring.
Foxboro DCS allows central monitoring of multiple sites through secure remote access, centralized data historians, and web-based dashboards. Using VPN tunnels, firewalls, and DMZ architectures, it ensures secure data transfer. Operators at the central control room can view real-time data, trends, and alarms from multiple plants. Cloud-based applications allow mobile access to KPIs and diagnostics. This setup enables lean operations, reduces on-site manpower, and provides unified visibility across geographies.
15. What are some common challenges in deploying Foxboro DCS and how can they be mitigated?
Common challenges include integration with legacy systems, managing complex control strategies, ensuring cybersecurity, and minimizing downtime during upgrades. These can be mitigated through proper project planning, simulation-based testing, use of standardized libraries, and phased migration approaches. Investing in operator and engineer training helps reduce configuration errors and improves system utilization. Partnering with certified Foxboro integrators and utilizing Schneider Electric’s lifecycle services ensures deployment success and long-term performance.
Course Schedule
Apr, 2025 | Weekdays | Mon-Fri | Enquire Now |
Weekend | Sat-Sun | Enquire Now | |
May, 2025 | Weekdays | Mon-Fri | Enquire Now |
Weekend | Sat-Sun | Enquire Now |
Related Courses
Related Articles
Related Interview
Related FAQ's
- Instructor-led Live Online Interactive Training
- Project Based Customized Learning
- Fast Track Training Program
- Self-paced learning
- In one-on-one training, you have the flexibility to choose the days, timings, and duration according to your preferences.
- We create a personalized training calendar based on your chosen schedule.
- Complete Live Online Interactive Training of the Course
- After Training Recorded Videos
- Session-wise Learning Material and notes for lifetime
- Practical & Assignments exercises
- Global Course Completion Certificate
- 24x7 after Training Support
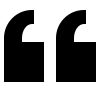