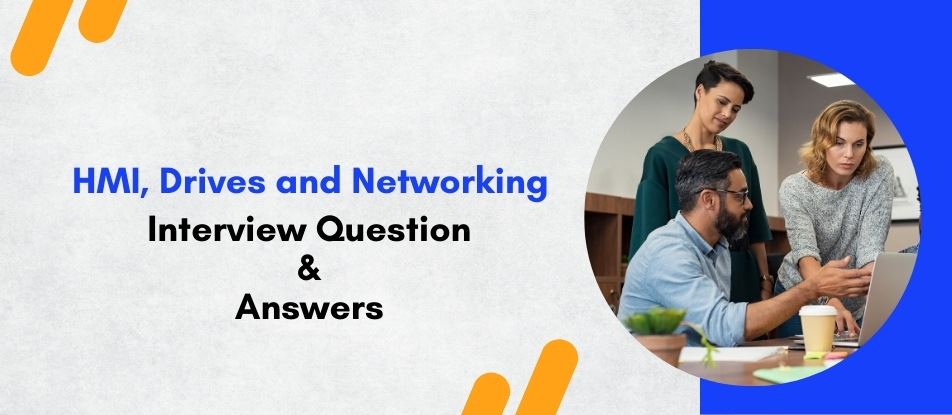
Master the fundamentals and advanced techniques of HMI, motor drives, and industrial networking in this hands-on training. Learn to design user-friendly interfaces, configure and optimize drives, and implement reliable communication protocols such as Profinet and Modbus. This course prepares professionals to troubleshoot, integrate, and enhance automation systems for improved efficiency and performance, making it ideal for engineers and technicians in industrial automation.
HMI, Drives and Networking Training Interview Questions Answers - For Intermediate
1. What is the difference between a centralized and a decentralized HMI system?
A centralized HMI system controls multiple processes from one location, often in a control room. In contrast, a decentralized HMI system has multiple distributed interfaces closer to the equipment, providing localized control and monitoring.
2. How do you ensure optimal performance of a VFD?
- Properly size the VFD for the motor.
- Configure parameters like voltage, current limits, and acceleration time correctly.
- Use recommended cabling and grounding to reduce electrical noise.
- Regularly monitor and maintain the system.
3. What is the significance of refresh rate in HMIs?
The refresh rate determines how frequently the HMI updates data from the connected devices. A high refresh rate improves responsiveness but may increase network load. Balancing the refresh rate is critical for system performance.
4. How does PID control integrate with drives?
PID (Proportional-Integral-Derivative) control helps maintain stable motor operation by adjusting speed or torque based on feedback. Drives often have built-in PID controllers to regulate process variables like pressure or flow rate.
5. What is DeviceNet, and how is it used in automation?
DeviceNet is a protocol for connecting industrial devices like sensors, actuators, and drives. It simplifies wiring by combining power and communication in a single cable and allows for modular system designs.
6. How do you test an HMI before deployment?
- Verify connectivity with the PLC or drive.
- Test navigation and functionality of the user interface.
- Simulate real-world conditions to check alarm handling and data accuracy.
- Ensure proper scaling of variables and visualization.
7. What are the common causes of drive failure?
- Overheating due to insufficient cooling.
- Electrical surges or spikes.
- Misconfigured parameters leading to overcurrent or undervoltage faults.
- Aging components like capacitors.
- Poor grounding or high electrical noise.
8. What is the purpose of a soft starter, and how does it differ from a VFD?
A soft starter gradually increases voltage to the motor during startup, reducing inrush current and mechanical stress. Unlike a VFD, it cannot control motor speed during operation and is primarily used for fixed-speed applications.
9. Explain redundancy in industrial networks.
Redundancy ensures system reliability by providing backup paths or devices. For example, in Ethernet networks, protocols like RSTP (Rapid Spanning Tree Protocol) enable alternative paths if a primary link fails.
10. How does a drive handle overvoltage or undervoltage conditions?
Drives detect voltage abnormalities using internal monitoring circuits.
- Overvoltage: Triggers energy-dissipation mechanisms, such as braking resistors, or shuts down the drive.
- Undervoltage: Reduces motor performance or halts operation to prevent damage.
11. What are the advantages of using industrial Ethernet over traditional fieldbuses?
- Higher bandwidth for faster data transmission.
- Scalability for complex systems.
- Standardized protocols like Ethernet/IP and Profinet for seamless device integration.
- Easier troubleshooting with diagnostic tools.
12. How does regenerative braking work in drives?
Regenerative braking converts the kinetic energy of a decelerating motor back into electrical energy. Drives equipped with regenerative modules can return this energy to the power grid or store it in batteries, improving energy efficiency.
13. What are the limitations of RS-485 communication in industrial networks?
- Limited data rate compared to Ethernet.
- Maximum cable length of approximately 1200 meters.
- Requires manual termination and biasing resistors for stable communication.
- Susceptible to electrical noise in high EMI environments.
14. What is the role of a gateway in industrial networking?
A gateway connects devices or networks using different protocols, enabling seamless communication. For example, a Modbus-to-Profinet gateway allows devices on a Modbus network to communicate with Profinet-enabled devices.
15. What are the benefits of using OPC (Open Platform Communications) in automation?
OPC provides a standardized method for devices to exchange data across different platforms. Benefits include:
- Interoperability between hardware and software.
- Centralized data access for SCADA, HMIs, and MES systems.
- Easy scalability and integration with IoT systems.
HMI, Drives and Networking Training Interview Questions Answers - For Advanced
1. What are the benefits of using Web-based HMIs over traditional HMIs in industrial automation?
Web-based HMIs leverage modern web technologies to provide remote access to industrial systems via standard web browsers, eliminating the need for proprietary software. They enable real-time monitoring and control from any location, facilitating remote diagnostics and troubleshooting. Additionally, they are highly scalable, allowing integration with cloud-based IIoT platforms. By supporting responsive design, web-based HMIs ensure consistent performance across devices, from smartphones to large displays. However, secure implementation with features like HTTPS and user authentication is critical to prevent unauthorized access.
2. How does field-oriented control (FOC) in drives improve motor efficiency?
Field-oriented control (FOC) enhances motor efficiency by controlling the motor’s magnetic flux and torque separately. This is achieved by converting the motor’s three-phase currents into two orthogonal components, enabling precise control over torque production. FOC provides smoother operation, better dynamic response, and higher energy efficiency, especially in high-performance applications like robotics and CNC machines. Its implementation, however, requires advanced processing capabilities and accurate feedback from sensors or estimators.
3. What is the significance of VLANs in industrial networking?
VLANs (Virtual Local Area Networks) segment a physical network into multiple logical networks, improving security and traffic management in industrial systems. By isolating critical devices like PLCs and drives from general traffic, VLANs reduce the risk of unauthorized access and minimize the impact of network congestion. They also enhance network performance by reducing broadcast domains. Proper VLAN configuration requires planning to ensure seamless communication between different segments while maintaining isolation.
4. Explain the working and advantages of an active front-end (AFE) in drives.
An active front-end (AFE) is a power rectifier that improves the performance of drives by providing sinusoidal current input, reducing harmonic distortion, and enabling bidirectional power flow for regenerative energy recovery. Unlike traditional diode rectifiers, AFEs actively regulate the input current, ensuring compliance with harmonic standards like IEEE 519. They are particularly beneficial in energy-intensive applications where regenerative braking and low harmonic distortion are critical.
5. How do industrial protocols like EtherCAT achieve real-time communication?
EtherCAT achieves real-time communication by using a master-slave architecture with a single Ethernet frame traveling through all devices in a ring topology. Each slave device extracts its data and inserts response data on-the-fly, minimizing latency. EtherCAT’s deterministic nature and low cycle times (as low as 12.5 µs) make it ideal for time-critical applications like motion control and robotics. It also supports synchronization with nanosecond-level precision using distributed clocks.
6. What are the steps to optimize an HMI’s performance in a complex industrial system?
Optimizing an HMI involves reducing graphical load by avoiding unnecessary animations and using efficient graphic rendering techniques. Organizing data logically with layered screens prevents information overload. Properly configuring communication settings, like poll rates and protocol selection, ensures responsive performance. Additionally, implementing efficient alarm management, compressing historical data logs, and using high-performance hardware with sufficient memory and processing power further enhance performance.
7. What is droop control in drives, and how is it applied in load sharing?
Droop control is a technique used in multi-drive systems to share load proportionally among drives. Each drive reduces its speed or torque slightly as the load increases, ensuring balanced operation without requiring a direct communication link between drives. This is commonly applied in parallel pump or fan systems, where maintaining equal load distribution prevents overloading a single motor while enhancing system reliability and efficiency.
8. How do software-defined networks (SDN) enhance industrial automation systems?
SDN decouples network control from the physical hardware, enabling centralized control of network traffic. This enhances industrial automation by providing real-time visibility into network performance and simplifying reconfiguration. SDN allows quick deployment of network policies, improved traffic prioritization for time-sensitive applications, and dynamic adjustment to changing system requirements. Its flexibility also supports seamless integration of IIoT devices and cloud-based analytics.
9. What challenges do regenerative drives face, and how are they addressed?
Regenerative drives face challenges like grid compatibility, harmonic distortion, and managing excess energy during grid faults. These issues are addressed by using active front-end rectifiers, implementing DC bus capacitors for energy storage, and integrating harmonic filters. In critical applications, dynamic braking resistors can dissipate excess energy to ensure system stability during power interruptions or regenerative surges.
10. How does the concept of edge computing apply to HMIs in industrial automation?
Edge computing in HMIs processes data locally at the device level instead of relying on centralized systems. This reduces latency, enhances real-time decision-making, and minimizes bandwidth usage for cloud communication. HMIs equipped with edge computing can analyze trends, detect anomalies, and trigger alarms independently. They also act as gateways for securely transmitting aggregated data to the cloud for further processing and analytics.
11. What are the best practices for implementing network redundancy in industrial automation?
Implementing network redundancy involves using redundancy protocols like RSTP or PRP to ensure continuous communication during link failures. Critical devices should be connected in ring or mesh topologies, and dual-homing can be employed to connect devices to multiple switches. Regular testing of failover mechanisms, proper documentation, and using industrial-grade switches with diagnostic capabilities are essential for maintaining network reliability.
12. How do adaptive control algorithms in drives improve energy efficiency?
Adaptive control algorithms dynamically adjust drive parameters to optimize motor operation based on load conditions. These algorithms monitor variables like speed, torque, and current, ensuring the motor operates at its peak efficiency point. For example, in HVAC systems, adaptive control can minimize energy consumption by maintaining the desired airflow while reducing motor speed during low-demand periods.
13. What are the limitations of traditional RS-232 communication in industrial networks, and how are they overcome?
RS-232 has limitations such as short communication distances (up to 15 meters), limited data rate (up to 115.2 kbps), and the inability to support multi-drop connections. These are overcome by using RS-485, which supports longer distances (up to 1200 meters) and multi-drop capabilities, or by transitioning to Ethernet-based protocols, which offer higher data rates, scalability, and compatibility with modern automation systems.
14. How do drives with multi-level inverters reduce power quality issues?
Drives with multi-level inverters divide the DC voltage into multiple levels, producing a near-sinusoidal AC waveform. This reduces harmonic distortion, voltage stress on the motor, and switching losses. Multi-level inverter drives are particularly effective in high-power applications, such as in the oil and gas or mining industries, where power quality and efficiency are critical.
15. How is network traffic prioritization achieved in industrial automation systems?
Network traffic prioritization is achieved using QoS (Quality of Service) mechanisms, which classify and prioritize data packets based on their importance. Critical data, such as control commands or safety messages, are given higher priority over non-essential traffic like file transfers. Protocols like IEEE 802.1Q (VLAN tagging) and DSCP (Differentiated Services Code Point) ensure that time-sensitive data is delivered with minimal latency and jitter, maintaining system reliability and performance.
Course Schedule
Apr, 2025 | Weekdays | Mon-Fri | Enquire Now |
Weekend | Sat-Sun | Enquire Now | |
May, 2025 | Weekdays | Mon-Fri | Enquire Now |
Weekend | Sat-Sun | Enquire Now |
Related Courses
Related Articles
Related Interview
Related FAQ's
- Instructor-led Live Online Interactive Training
- Project Based Customized Learning
- Fast Track Training Program
- Self-paced learning
- In one-on-one training, you have the flexibility to choose the days, timings, and duration according to your preferences.
- We create a personalized training calendar based on your chosen schedule.
- Complete Live Online Interactive Training of the Course
- After Training Recorded Videos
- Session-wise Learning Material and notes for lifetime
- Practical & Assignments exercises
- Global Course Completion Certificate
- 24x7 after Training Support
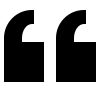