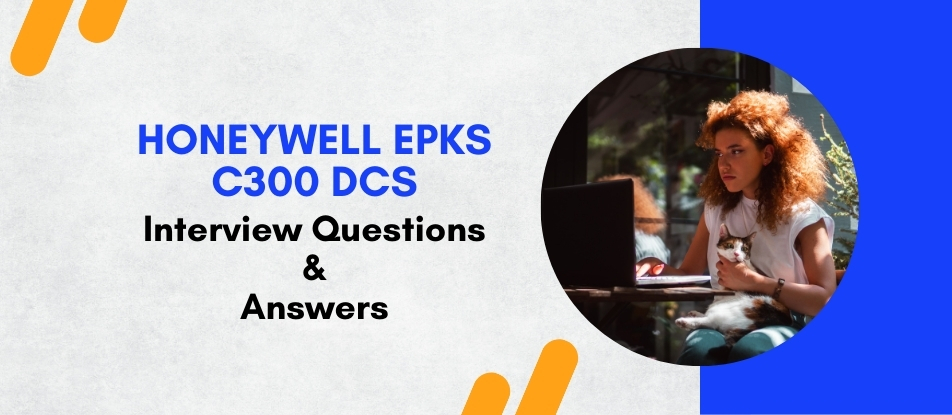
This comprehensive training course on Honeywell EPKS C300 DCS focuses on equipping participants with the skills needed to effectively utilize the C300 controller in process industries. The course delves into detailed aspects of system configuration, control strategy implementation, and network security. Trainees will gain firsthand experience through practical exercises on system optimization, troubleshooting, and integration with third-party systems, ensuring they can manage and maintain the C300 system to enhance operational efficiency and reliability.
Honeywell EPKS C300 DCS Interview Questions Answers - For Intermediate
1. What is the role of the Honeywell Uniformance PHD in the C300 system?
Uniformance PHD acts as a historical data archive that integrates with the C300 system to collect, store, and retrieve process data. It supports data-driven decision-making by providing detailed process insights and trend analysis.
2. How does C300 handle batch processing?
C300 utilizes the Batch Manager software which manages batch processes by executing recipes, controlling equipment, and documenting production. It ensures consistent, repeatable processes which are critical in batch-oriented industries like pharmaceuticals and food processing.
3. What are Smart IO Modules, and how do they contribute to the efficiency of the C300 system?
Smart IO Modules in the C300 system are capable of performing diagnostics and processing directly at the IO level, which reduces the data load on the controller and enhances system response and reliability.
4. Explain the concept of Control Builder in the Experion PKS C300 system.
Control Builder is a software tool used for developing and testing control strategies in the C300 system. It provides a user-friendly interface for engineers to design, simulate, and deploy control applications and strategies.
5. Discuss the interoperability of C300 with other DCS systems.
C300 is designed to interoperate with other DCS systems through standard communication protocols like OPC UA, Modbus, and EtherNet/IP, facilitating seamless data exchange and integration across different platforms.
6. Can you explain how redundancy is managed within the Flex Station components of the C300 system?
In the C300 system, Flex Stations can be configured with redundant links and power supplies to ensure continuous operation. The redundancy management includes automatic switchover to backup systems in case of any failure in the primary system.
7. What is Dynamic Configuration and how does it benefit C300 system operations?
Dynamic Configuration allows changes to the control system configuration without stopping the process. This is beneficial for C300 operations as it minimizes downtime and allows for flexibility in making system modifications on the fly.
8. How is system security maintained during remote access of the C300 DCS?
System security during remote access is maintained through encrypted VPN connections, rigorous authentication mechanisms, and strict access controls to ensure that only authorized users can interact with the DCS components.
9. Describe the alarm management features available in the Experion PKS C300 system.
The Experion PKS C300 system includes advanced alarm management features such as alarm shelving, suppression, and grouping. These features help in managing alarm floods and ensure that operators can focus on the most critical alarms.
10. How does the C300 system integrate with plant-wide asset management systems?
C300 integrates with asset management systems via standard communication interfaces, providing real-time data on equipment status and performance. This integration helps in proactive maintenance planning and reduces unplanned downtimes.
11. What is the procedure for updating the firmware of I/O modules in the C300 system?
Firmware updates in I/O modules are typically performed through the Device Management Application, which allows for downloading and installing firmware updates directly to the modules without interrupting their operation.
12. Explain how C300 supports predictive maintenance.
C300 supports predictive maintenance by integrating with advanced analytics tools that analyze historical and real-time data to predict equipment failures. This helps in scheduling maintenance activities before actual failures occur, thus reducing downtime.
13. Discuss the role of Virtualization in the C300 system architecture.
Virtualization in the C300 system involves using virtual machines to run multiple instances of system software, which enhances system scalability, flexibility, and redundancy by distributing the system load across multiple physical servers.
14. What are the capabilities of the C300 in handling multi-variable control?
The C300 is capable of handling multi-variable control through its Advanced Process Control (APC) functionalities. These functionalities allow the controller to manage multiple interdependent variables simultaneously, optimizing the overall process performance.
15. How does the C300 ensure data integrity during transmission between different system layers?
The C300 ensures data integrity during transmission by using checksums and data encryption techniques. These measures prevent data corruption and unauthorized access, maintaining the reliability and security of transmitted data.
Honeywell EPKS C300 DCS Interview Questions Answers - For Advanced
1. Explain the role of Honeywell's LEAPâ„¢ project methodology concerning the C300 system.
Honeywell's Lean Execution of Automation Projects (LEAPâ„¢) methodology significantly impacts the deployment and maintenance of the C300 system by adopting a lean project execution approach. This methodology centers on reducing costs, minimizing risks, and accelerating schedule performance by integrating hardware and software development more closely. For the C300 system, LEAP involves parallel workflows where hardware and software are configured and tested independently and then integrated seamlessly. This approach allows for virtual system commissioning, which can significantly reduce the amount of on-site work required and shorten project timelines.
2. Discuss the adaptive control functionalities in the C300 and their benefits in process variability reduction.
The C300 system incorporates adaptive control functionalities that automatically adjust control parameters in real time based on process feedback. This feature is particularly beneficial in applications with high process variability, as it ensures optimal control despite changes in process conditions. By continuously monitoring process deviations and dynamically adjusting control strategies, the C300 helps maintain setpoint targets and minimizes variability. This results in improved process efficiency, reduced energy consumption, and enhanced product quality, making it a vital tool in industries such as chemicals and refining where process conditions can frequently change.
3. How does the C300 integrate with Experion Collaboration Station and what are the benefits of this integration?
The C300 system's integration with Experion Collaboration Station offers substantial benefits by enhancing collaborative operations across different teams and locations. Experion Collaboration Station allows operators, engineers, and management to view and interact with real-time and historical process data via a centralized interface. This integration facilitates better decision-making by providing a comprehensive view of the process, enabling remote troubleshooting, and supporting collaborative problem-solving sessions. It enhances operational awareness and accelerates response to critical events, thereby improving overall plant performance and safety.
4. What is Rapid Project Implementation (RPI) in the context of C300 DCS, and how does it benefit project timelines?
Rapid Project Implementation (RPI) is a methodology applied within the C300 DCS framework to expedite the entire project lifecycle from design through commissioning. RPI leverages pre-configured templates and standard workflows to streamline the setup and deployment of control systems. By reducing the complexity and duration of implementation phases, RPI significantly shortens project timelines, allowing for quicker system turnover and reduced costs. This approach is particularly beneficial in projects where time constraints are critical, providing a competitive edge by enabling faster market entry.
5. Explain the procedure and importance of controller tuning in the C300 system.
Controller tuning in the C300 system is crucial for achieving optimal process control and efficiency. The tuning procedure involves adjusting control parameters such as PID gains to match the dynamics of the process. Accurate tuning ensures that the controller responds appropriately to disturbances, maintaining stability and minimizing overshoot. This is especially important in complex processes where even minor deviations can lead to significant quality or safety issues. The tuning process typically includes steps such as identifying the plant model, applying tuning algorithms, and validating performance through simulation or live tests.
6. How does the C300 utilize real-time analytics for predictive maintenance?
The C300 system utilizes real-time analytics to enhance predictive maintenance strategies by continuously analyzing data from process equipment to identify patterns or anomalies indicative of potential failures. These analytics tools employ advanced algorithms and machine learning techniques to predict when equipment might fail or require maintenance, allowing for proactive interventions. This capability not only helps avoid unplanned downtime but also optimizes maintenance schedules, reducing costs and extending equipment life by ensuring that maintenance is performed only when necessary.
7. Describe the security measures in place to protect the C300 system from unauthorized access.
To protect the C300 system from unauthorized access, several robust security measures are implemented, including multi-factor authentication, role-based access control, and rigorous user authentication mechanisms. The system also employs comprehensive auditing and logging features to track user actions and detect any unauthorized attempts to access the system. Network security is strengthened through the use of firewalls, intrusion detection systems, and secure communication protocols like SSL/TLS to encrypt data transmissions. Together, these measures ensure a high level of security, protecting critical process control systems from cyber threats.
8. What are the benefits of the SIL-3 certification for C300 controllers, and how does it impact system design?
The SIL-3 certification of C300 controllers signifies that they meet the highest safety integrity levels as defined by IEC 61508 standards, making them suitable for use in high-risk applications such as oil and gas production, chemical processing, and nuclear power generation. This certification requires rigorous testing and validation of the controllers to ensure they can reliably perform safety functions under anticipated conditions. The impact on system design is significant, as it necessitates the incorporation of redundant configurations, fail-safe mechanisms, and stringent quality controls to achieve and maintain the SIL-3 standard. This not only enhances the safety of the control system but also builds confidence among stakeholders regarding the system’s reliability in critical operations.
9. How does the C300 system manage large-scale data logging and retrieval for complex processes?
The C300 system manages large-scale data logging and retrieval through its powerful data management capabilities, which include high-capacity data historians and sophisticated data retrieval tools. The system is designed to handle vast amounts of data generated from complex processes, storing it in a structured manner that facilitates quick and efficient retrieval. Data logging is optimized to capture critical process parameters at high frequencies, ensuring that detailed process insights are available for analysis. Retrieval tools allow users to access historical data for trend analysis, performance assessment, and regulatory compliance, making the data management system a key component in supporting decision-making and process optimization.
10. Discuss the use of custom application development within the C300 environment.
Custom application development within the C300 environment allows users to tailor the control system to meet specific operational requirements that are not addressed by standard software components. This is achieved through the use of open APIs and scripting languages supported by the C300 system, which provides the flexibility to develop custom interfaces, reports, and control algorithms. Custom applications can enhance the functionality of the control system, integrate it with external systems, or automate unique processes, providing significant benefits in terms of operational efficiency and system usability.
11. How are software updates and patches managed in the C300 system to minimize disruption?
Software updates and patches in the C300 system are managed through a structured process that emphasizes minimal disruption to ongoing operations. Updates are typically scheduled during planned downtime and are thoroughly tested in a simulated environment before deployment. The system also supports hot swapping and online updates for certain components, allowing updates to be applied without stopping the entire system. This careful management ensures that the system remains secure and up-to-date with the latest features and bug fixes without compromising process continuity.
12. Explain the integration capabilities of C300 with enterprise resource planning (ERP) systems.
The C300 system's integration capabilities with ERP systems are facilitated through standard industrial protocols and middleware solutions that enable seamless data exchange. This integration allows real-time process data from the C300 system to be utilized for higher-level business planning and decision-making within the ERP framework. For instance, production data can directly influence supply chain management, inventory control, and financial planning. This holistic approach enhances operational visibility and coordination across various business functions, leading to improved efficiency and strategic alignment.
13. What role does the C300 play in energy management and sustainability initiatives?
The C300 system plays a pivotal role in energy management and sustainability initiatives by providing the tools necessary to monitor and control energy usage within industrial processes. Its advanced control capabilities allow for the optimization of process parameters to reduce energy consumption without compromising output quality. Furthermore, the system can integrate with energy management software to provide comprehensive reports and analytics on energy usage patterns, identifying opportunities for energy savings and contributing to broader sustainability goals.
14. How does the C300 support the implementation of Industry 4.0 in manufacturing environments?
The C300 supports the implementation of Industry 4.0 in manufacturing environments by enabling advanced connectivity, analytics, and automation features that are fundamental to smart manufacturing. The system facilitates the integration of IoT devices and supports data exchange across a connected infrastructure, allowing for greater automation and data-driven decision-making. By leveraging real-time data and predictive analytics, manufacturers can optimize operations, improve productivity, and enhance product quality, aligning with the objectives of Industry 4.0.
15. Discuss the training and certification process for operators and engineers on the C300 system.
The training and certification process for operators and engineers on the C300 system is comprehensive and designed to ensure that personnel are fully equipped to manage and operate the system effectively. Training typically includes hands-on sessions, simulations, and classroom instruction covering system architecture, operation, troubleshooting, and maintenance. Certification involves a combination of practical assessments and written exams to verify the competence of individuals in handling real-world scenarios. This process not only enhances the skill set of the workforce but also ensures that the system is operated at optimum efficiency, with reduced risks of errors or downtime.
Course Schedule
Jul, 2025 | Weekdays | Mon-Fri | Enquire Now |
Weekend | Sat-Sun | Enquire Now | |
Aug, 2025 | Weekdays | Mon-Fri | Enquire Now |
Weekend | Sat-Sun | Enquire Now |
Related Courses
Related Articles
Related Interview
Related FAQ's
- Instructor-led Live Online Interactive Training
- Project Based Customized Learning
- Fast Track Training Program
- Self-paced learning
- In one-on-one training, you have the flexibility to choose the days, timings, and duration according to your preferences.
- We create a personalized training calendar based on your chosen schedule.
- Complete Live Online Interactive Training of the Course
- After Training Recorded Videos
- Session-wise Learning Material and notes for lifetime
- Practical & Assignments exercises
- Global Course Completion Certificate
- 24x7 after Training Support
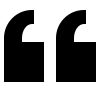