This Honeywell EPKS C300 DCS course is designed to equip automation engineers with comprehensive knowledge of C300 controller architecture, configuration, and integration within the Experion PKS environment. Participants will learn to develop and troubleshoot control strategies, manage Series C I/O, implement redundancy, and work with FTE networking. The course combines theoretical concepts with hands-on training to ensure practical understanding of distributed control systems.
Honeywell EPKS C300 DCS Training Interview Questions Answers - For Intermediate
1. What are the key components of Honeywell Experion PKS integrated with C300?
Experion PKS integrates several core components with the C300 controller, including the Experion Server, Operator Station (HMI), Engineering Station, and Process History Database (PHD). These work together to provide real-time process control, data logging, visualization, alarm handling, and reporting in a unified environment that supports seamless operation and control.
2. How does C300 manage time synchronization across the system?
C300 uses Network Time Protocol (NTP) to synchronize time with the system's master time server, ensuring consistency across controllers, servers, and operator stations. Accurate time stamping is critical for events, alarms, and historical data. This synchronization supports diagnostic analysis and compliance with regulatory and audit requirements.
3. How is C300 different from older Honeywell controllers like the C200?
While C200 controllers were rack-mounted and used traditional I/O architecture, the C300 features a more modular and scalable design using Series C I/O. C300 uses Ethernet-based FTE instead of ControlNet as its backbone and offers enhanced processing power, improved diagnostics, and integration capabilities aligned with modern industrial control systems.
4. How are trends configured and visualized in Honeywell EPKS?
Trends are configured via the HMIWeb Display Builder or through Quick Builder. Operators can monitor real-time and historical trends of process parameters on the Experion Station. The trending tool allows selection of pens, time ranges, scales, and event markers, aiding in analysis, troubleshooting, and performance monitoring.
5. How does Honeywell EPKS handle user access control and security?
Experion PKS supports role-based access control integrated with Windows domain authentication. Users are assigned roles with defined privileges for viewing, configuring, or operating the system. Audit trails, password policies, and user activity logs enhance cybersecurity and support compliance with industry standards like ISA-99 and NERC-CIP.
6. What is Peer Control Data (PCD) and how does C300 utilize it?
PCD enables communication between controllers within the same system for sharing process data. In C300, this is facilitated through FTE. PCD ensures that one controller can use real-time values or statuses from another without duplication of signals or wiring, supporting efficient distributed control strategies across units or process areas.
7. How does the system handle diagnostics for I/O modules?
Series C I/O modules integrated with C300 continuously self-monitor and report health status to the controller. This includes wire break detection, short circuits, and module faults. The diagnostic information is available on Experion Station graphics and in Control Builder, helping maintenance teams to quickly isolate and fix issues.
8. Explain how Experion PKS supports hot redundancy in C300.
C300 controllers are configured in active-passive redundancy with synchronization handled automatically. When the active controller fails, the passive controller instantly takes over using shared memory and state replication. This "hot redundancy" minimizes switchover time and ensures that there is no disruption in control loops or logic execution.
9. What is the role of the FIM in the C300 architecture?
The Fieldbus Interface Module (FIM) connects the C300 controller to Series C I/O. It handles communication, data acquisition, and diagnostics between the controller and the field I/O modules. Redundant FIMs ensure availability and reliability, while also supporting different protocols like Foundation Fieldbus and Profibus for flexible integration.
10. How does C300 ensure deterministic control?
Determinism is achieved in C300 through the Control Execution Environment (CEE), which schedules execution cycles with fixed scan times. Control Builder allows users to define execution priorities and cycle times, ensuring that critical logic executes within guaranteed time frames, even under high system load.
11. Can online changes be made to logic in a C300 controller?
Yes, Control Builder supports online changes in C300 without requiring a controller reboot. Engineers can add or modify blocks, change parameters, and reconfigure connections while the controller continues to run. A change list tracks all modifications, and changes are downloaded only after confirmation, reducing the risk of process disruption.
12. What is the difference between local and remote I/O in C300?
Local I/O is physically mounted close to the C300 controller using a backplane, while remote I/O is located in field cabinets connected via fiber or copper links. Both types use Series C architecture and can be accessed through FIMs. Remote I/O helps reduce cabling and improve maintainability in large plants.
13. How are graphic displays developed in the Experion environment?
Graphic displays are created using HMIWeb Display Builder, which is a drag-and-drop tool. Engineers can add objects like valves, pumps, tanks, and indicators, and link them to live process values. Custom animations, color changes, and scripts can enhance operator interaction and visibility of system conditions.
14. What types of function blocks are commonly used in C300?
Commonly used function blocks in C300 include PID, AI (Analog Input), AO (Analog Output), DI (Digital Input), DO (Digital Output), timers, selectors, and math blocks. Each block is configurable with parameters and alarms, and can be interconnected to form complex control strategies using Control Builder.
15. How is the health of the C300 system monitored from the Experion Station?
Experion Station provides an integrated health monitoring dashboard for controllers, I/O modules, servers, and network devices. Visual indicators, alarm messages, and system logs highlight potential problems. Diagnostic views can display status such as redundant controller synchronization, I/O faults, communication errors, and firmware status to aid operators and engineers.
Honeywell EPKS C300 DCS Training Interview Questions Answers- For Advanced
1. How does Honeywell C300 handle exception-based scanning and why is it important?
Honeywell C300 supports exception-based scanning for optimized I/O processing. Instead of polling every input at fixed intervals, the system only processes data when a change is detected—this is particularly effective for digital signals or slowly varying analog signals. Exception-based scanning reduces CPU load, network traffic, and unnecessary data updates, enhancing overall system performance. The I/O modules detect status or value changes and immediately push the updates to the controller, ensuring faster response times for critical signals without overburdening the control loop scan cycles. This approach enables more scalable and responsive systems, especially in large or distributed plants.
2. Explain the concept of memory management in the C300 controller and its impact on system design.
Memory in the C300 controller is managed dynamically to store control strategies, block parameters, historical logs, and real-time data values. The controller comes with scalable memory configurations based on process complexity. Designers must carefully plan memory usage by estimating the number of function blocks, interconnections, alarms, and peer data links. Control Builder provides memory usage reports during strategy compilation, helping identify over-allocation or memory leaks. Efficient memory management ensures optimal controller performance, reduces the risk of scan overruns, and enhances redundancy switchover stability. Poor memory planning may lead to execution delays, dropped communication, or system reboots.
3. Describe how C300 supports change management and version control in process automation projects.
C300 integrates with Honeywell’s versioning and audit mechanisms within Control Builder and Experion Engineering tools. Every change to a Control Module or Sequential Control Module is logged with a timestamp, user ID, and a comment field for change justification. Engineers can compare current and previous versions, roll back changes, and generate reports for audits. Combined with Experion’s security roles and audit trail features, this supports regulatory compliance in industries like pharmaceuticals and chemicals. Additionally, version control helps in managing project lifecycle stages—from FAT to SAT to commissioning—ensuring consistent logic deployment and avoiding unauthorized modifications.
4. What is the impact of scan overruns in the C300 controller, and how are they mitigated?
A scan overrun occurs when the control logic takes longer to execute than the configured scan time. In a C300 controller, this can lead to delayed I/O updates, unstable control loops, and potentially unsafe operating conditions. The CEE is designed to log and alarm overruns immediately, allowing for operator or engineering intervention. To mitigate scan overruns, engineers can reduce the number of active function blocks, optimize execution cycle priorities, split control modules into multiple loops, or increase the scan interval slightly. Performance tuning tools within Control Builder help identify high-CPU-consuming modules or blocks, enabling informed adjustments.
5. How does C300 support simulation and testing of control strategies without actual field devices?
Honeywell’s Control Builder provides an offline simulation mode, allowing engineers to test control logic before downloading it to live hardware. Engineers can enable simulation at the block level or for entire modules, using test inputs and monitoring outputs in real-time. Simulated function blocks behave like real ones but use internal data values. Additionally, virtual I/O simulators can be linked to Experion stations for HMI testing. This capability is vital for FAT (Factory Acceptance Testing), debugging logic errors, and validating alarms, interlocks, and sequences—reducing commissioning time and minimizing risks during actual plant startup.
6. Discuss the role of OPC in integrating C300 with external systems like ERP or MES.
OPC (OLE for Process Control) is a standard interface used to bridge real-time data from the C300/Experion system to external platforms like ERP or MES. Honeywell’s OPC DA (Data Access) and OPC UA (Unified Architecture) servers expose live process variables, alarms, and historian data to third-party clients. OPC enables vertical integration, allowing production KPIs, inventory levels, and quality parameters to be monitored at the enterprise level. OPC tunneling and redundancy features ensure secure, reliable data delivery even in distributed or multi-vendor environments. Security, namespace configuration, and real-time tag mapping are key considerations during setup.
7. How is alarm shelving handled in Experion Station and why is it important for C300 operators?
Alarm shelving in Experion Station allows operators to temporarily suppress non-critical alarms that do not require immediate attention. This is especially useful during maintenance, calibration, or known equipment issues to avoid alarm floods and operator overload. Shelved alarms are not lost—they are logged, timestamped, and restored automatically after a defined duration. Operators can manually unshelve them anytime. Shelving is managed with access privileges and appears in the alarm summary with distinct visual indicators. For C300, this ensures cleaner alarm displays and helps maintain focus on genuine abnormal conditions during critical operations.
8. What are HMIWeb graphics, and how do they enhance operator interaction with the C300 controller?
HMIWeb is Honeywell’s modern web-based HMI technology used for creating graphical displays for operator stations. Graphics are developed using Display Builder and are embedded with dynamic objects linked to C300 process variables. Features include color-coded status indications, real-time trends, faceplates, and embedded scripts for advanced interactions. HMIWeb supports resolution-independent design, alarm integration, navigation hierarchies, and diagnostics. These graphics enhance operator decision-making by providing intuitive, real-time visibility into process operations, supporting fast fault identification, and promoting situational awareness across all process areas.
9. Explain the importance of dynamic parameter linking between Control Modules in C300.
Dynamic parameter linking allows one Control Module to use real-time values from another without hardcoding values or creating unnecessary peer links. This is particularly useful in modular engineering, where reusable templates or parameterized modules are employed. Linking is done via drag-and-drop or parameter referencing, and the control strategy maintains flexibility and adaptability. It reduces code duplication, improves readability, and facilitates scalable design. Moreover, during changes or troubleshooting, engineers can trace data flows between modules easily, ensuring faster diagnostics and improved strategy maintenance.
10. How does Honeywell's Experion PKS handle system diagnostics, and what tools are available for the C300?
Experion PKS provides comprehensive diagnostic tools for controllers, I/O, servers, and networks. For C300, diagnostic information includes controller health, execution times, module status, I/O health, communication link integrity, and redundancy status. These diagnostics are visualized through Experion Station, FTE View, and Control Builder. FTE View offers a graphical topology of the network, highlighting faults in real-time. The Alarm & Event subsystem logs all diagnostic events, which can be filtered and trended for proactive maintenance. Additionally, Honeywell offers Performance Pack add-ons for deeper analytics and predictive diagnostics.
11. How does C300 support advanced process control (APC) or model predictive control (MPC) strategies?
While C300 primarily executes traditional control strategies, it can interface with external APC or MPC applications via OPC, Modbus, or Profibus. These applications run complex models or optimization routines and send setpoints or control signals back to the C300 in real time. Honeywell’s Profit Suite is a native APC platform that can integrate with C300 for refining, petrochemical, and utilities optimization. By implementing APC at the supervisory level and using C300 for final control execution, plants achieve improved stability, energy savings, and throughput, especially in multivariable or constrained process environments.
12. How does Honeywell’s Experion handle batch management, and how does C300 fit into this ecosystem?
Experion PKS supports ISA-88 batch management through its Batch Manager application, which runs on dedicated servers and interfaces directly with C300. The controller hosts the equipment modules and procedural elements, while Batch Manager handles recipe execution, sequencing, operator instructions, and material tracking. Communication is achieved through shared databases and OPC links. The batch logic in C300 is modular, scalable, and includes phase management, setpoint control, and alarms. Experion provides batch records, audit trails, electronic signatures, and integration with MES systems, ensuring compliance with FDA and GMP regulations.
13. What steps are involved in commissioning a new C300-based control strategy in a live plant environment?
Commissioning involves multiple steps: (1) verifying controller and I/O hardware installation, (2) downloading and validating control strategies via Control Builder, (3) simulating and testing each module, (4) checking I/O point integrity and calibration, (5) verifying peer links and redundancy status, and (6) enabling live control. HMI displays are validated in parallel, and alarms are tested for correctness. Initial startup may involve a dry run with interlocks disabled to ensure safety. Documentation, backup, and operator training are key final steps before handing over the system for full operational use.
14. How does Honeywell EPKS ensure scalability in systems using multiple C300 controllers?
EPKS is designed for horizontal and vertical scalability. Horizontal scalability is achieved by adding more C300 controllers across process units, each with its own set of I/O and logic. Peer Control Data ensures inter-controller data sharing. Vertical scalability is achieved through centralized data collection, alarm management, historian integration, and MES connectivity via the Experion Server. Tools like Quick Builder and engineering templates make it easy to replicate strategies and displays across similar units. As demands grow, additional servers, historian capacity, and HMI clients can be added without redesigning the control architecture.
15. Describe how a plant-wide shutdown can be safely managed using C300 and Experion PKS.
A plant-wide shutdown is managed through carefully coordinated sequences programmed into Sequential Control Modules in C300. Each process unit is shut down in a predefined order based on interdependencies, ensuring energy, pressure, and flow are safely reduced. SCMs manage valve sequencing, interlock checks, and confirmation signals. Operators monitor progress through customized HMI graphics and receive real-time feedback via alarms and diagnostic messages. Experion PKS logs every shutdown step, creating audit trails and allowing post-event review. Integration with safety systems (like Honeywell’s Safety Manager) ensures emergency shutoffs operate independently, while the C300 manages normal shutdown sequences.
Course Schedule
Apr, 2025 | Weekdays | Mon-Fri | Enquire Now |
Weekend | Sat-Sun | Enquire Now | |
May, 2025 | Weekdays | Mon-Fri | Enquire Now |
Weekend | Sat-Sun | Enquire Now |
Related Courses
Related Articles
Related Interview
Related FAQ's
- Instructor-led Live Online Interactive Training
- Project Based Customized Learning
- Fast Track Training Program
- Self-paced learning
- In one-on-one training, you have the flexibility to choose the days, timings, and duration according to your preferences.
- We create a personalized training calendar based on your chosen schedule.
- Complete Live Online Interactive Training of the Course
- After Training Recorded Videos
- Session-wise Learning Material and notes for lifetime
- Practical & Assignments exercises
- Global Course Completion Certificate
- 24x7 after Training Support
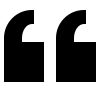