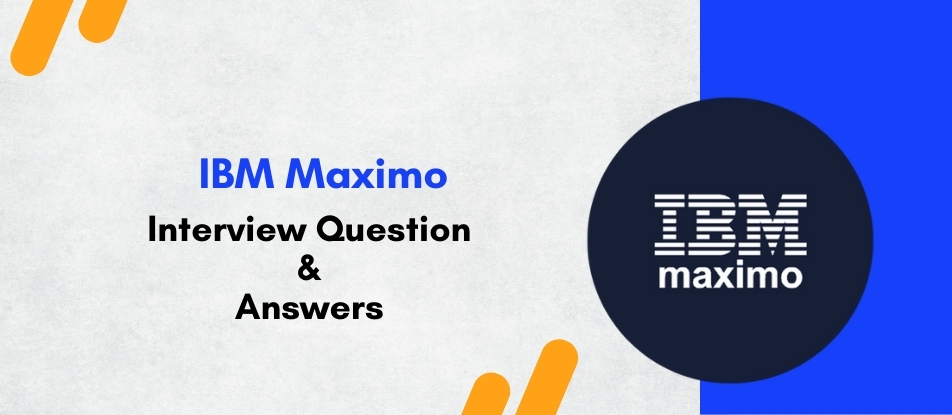
IBM Maximo Training offers an in-depth understanding of asset management and maintenance operations. Gain expertise in modules like work management, inventory control, and preventive maintenance, while exploring integration with IoT and analytics. This course is designed to enhance operational efficiency, streamline workflows, and empower professionals to manage the full lifecycle of assets effectively across diverse industries.
IBM Maximo Training Interview Questions Answers- For Intermediate
1. How does Maximo manage inventory for maintenance operations?
Maximo’s Inventory Management module tracks and controls spare parts and materials needed for maintenance operations. It allows users to monitor stock levels, set reorder points, and manage multiple storage locations. Maximo integrates inventory data with work orders, ensuring that required materials are available when needed, reducing delays and excess inventory costs.
2. What is the role of Domains in Maximo?
Domains in Maximo define a set of values that can be used in fields across the application. They ensure consistency and accuracy by restricting data entry to predefined options. For example, status domains for Work Orders might include values like "WAPPR," "APPR," or "COMP." Domains can be global, system-defined, or customized to meet specific business needs.
3. What are Failure Codes in Maximo, and why are they useful?
Failure Codes in Maximo categorize the reasons for asset failures. These codes help in analyzing recurring issues, identifying root causes, and improving maintenance practices. When technicians log failures using predefined codes, Maximo aggregates this data for reporting and decision-making, enabling organizations to reduce downtime and enhance asset reliability.
4. What is the significance of Condition Monitoring in Maximo?
Condition Monitoring in Maximo tracks asset performance metrics, such as temperature, pressure, or vibration, to predict potential failures. It triggers alerts or Work Orders when specific thresholds are exceeded. This proactive approach helps in preventing unexpected breakdowns and transitioning from reactive to predictive maintenance strategies.
5. How are security groups and roles used in Maximo?
Security groups and roles in Maximo define user permissions and access levels. Administrators assign users to security groups based on their responsibilities, controlling which modules, functions, or data they can access. This ensures data security, compliance with organizational policies, and appropriate segregation of duties.
6. What are Rotating Assets in Maximo?
Rotating Assets in Maximo are interchangeable assets, such as pumps or motors, that share common characteristics and can be swapped between locations. These assets are tracked by their unique identifiers but managed as a group, simplifying maintenance planning and inventory management for frequently replaced items.
7. How does Maximo handle workflow automation?
Maximo’s Workflow engine automates business processes by defining sequential or conditional steps for tasks like approvals, notifications, or escalations. For example, a workflow for a Work Order might include approvals from a supervisor and notifications to a technician. Automation reduces manual intervention, ensuring processes are consistent and efficient.
8. What are the key differences between Preventive and Predictive Maintenance in Maximo?
Preventive Maintenance (PM) in Maximo is scheduled based on time or usage intervals, while Predictive Maintenance (PdM) relies on real-time data and condition monitoring to predict failures. PM focuses on routine checks to prevent issues, whereas PdM uses advanced analytics to optimize maintenance timing and resources.
9. What is the purpose of the Classifications feature in Maximo?
Classifications in Maximo are used to categorize assets, locations, and other entities using a hierarchical structure. For instance, an asset might be classified under "Equipment > HVAC > Chiller." This feature enables better organization, reporting, and search capabilities by grouping similar items for easier management.
10. How does Maximo handle procurement for maintenance operations?
Maximo’s Procurement module streamlines the purchasing process for maintenance materials and services. It integrates with inventory and Work Order modules to generate purchase requisitions, issue purchase orders, and track supplier performance. This ensures timely procurement, cost control, and compliance with organizational policies.
11. What are Asset Meters in Maximo, and how are they used?
Asset Meters in Maximo track usage or condition data for assets, such as runtime hours or fluid levels. Meters are linked to maintenance triggers like PM schedules or Condition Monitoring thresholds. By monitoring meter readings, Maximo helps optimize maintenance activities and improve asset performance.
12. Explain the difference between Active and Inactive records in Maximo.
Active records in Maximo are those currently in use, such as active assets or open Work Orders. Inactive records, such as decommissioned assets or closed Work Orders, are retained for historical reference. This distinction helps maintain data relevance while preserving important records for auditing and reporting purposes.
13. What is the purpose of the Start Center in Maximo?
The Start Center in Maximo serves as a customizable dashboard for users, providing quick access to frequently used tools, reports, and KPIs. It displays relevant information like Work Order backlogs or inventory levels, tailored to the user’s role. This feature enhances productivity by centralizing critical data and actions.
14. How does Maximo integrate with third-party systems?
Maximo integrates with third-party systems through APIs, web services, and middleware like IBM Integration Bus or Maximo Integration Framework (MIF). These integrations enable data exchange with ERP, GIS, or IoT platforms, providing a unified view of operations. For example, Maximo can sync asset data with SAP for financial reporting.
15. What are the benefits of using Maximo in multi-site organizations?
Maximo supports multi-site configurations, allowing organizations to manage assets, inventory, and maintenance activities across multiple locations. Each site can have its own data and workflows, while administrators maintain centralized control. This setup improves operational visibility, standardizes processes, and ensures efficient resource allocation across sites.
IBM Maximo Training Interview Questions Answers- For Advanced
1. What is the Maximo Asset Health Insights (MAHI) module, and how does it enhance decision-making?
Maximo Asset Health Insights (MAHI) is an advanced module that provides a comprehensive view of an asset’s condition by consolidating data from IoT sensors, maintenance history, and external systems. It uses scoring models to evaluate asset health and offers visual dashboards for tracking key metrics. This module enables predictive and risk-based maintenance by highlighting critical assets that require immediate attention. By integrating real-time data and analytics, MAHI empowers organizations to make informed decisions, prioritize maintenance tasks, and reduce the likelihood of unexpected failures.
2. How does Maximo manage warranty tracking for assets?
Maximo provides robust warranty management functionality to track and enforce warranties for assets, components, and services. It stores warranty details, such as terms, coverage, and expiration dates, and links them to assets and Work Orders. When maintenance is performed on a warranted asset, Maximo alerts users and ensures that warranty claims are processed. This feature helps organizations recover costs for repairs covered under warranty, reducing maintenance expenses and enhancing asset lifecycle value.
3. Explain the difference between database configuration and application configuration in Maximo.
Database configuration in Maximo involves modifying the underlying database schema, such as creating new tables, adding attributes, or changing relationships between objects. It is typically done using the Database Configuration application and requires system downtime for applying changes. Application configuration, on the other hand, involves customizing the user interface, workflows, and business logic without altering the database structure. It includes tasks like modifying screen layouts, creating custom actions, and defining security settings. These configurations are critical for tailoring Maximo to meet organizational requirements.
4. How does Maximo facilitate integration with Geographic Information Systems (GIS)?
Maximo integrates with GIS platforms like Esri to provide spatial visualization of assets and work locations. This integration enables users to view assets on maps, analyze geospatial data, and plan maintenance activities based on location. For example, a utility company can use GIS integration to identify assets in flood-prone areas and prioritize inspections. Maximo’s GIS integration enhances situational awareness, improves resource allocation, and supports location-based decision-making, particularly in industries like utilities, transportation, and infrastructure management.
5. What is the significance of Maximo’s calibration management module?
The Calibration Management module in Maximo is designed for industries where precise measurements are critical, such as pharmaceuticals, oil and gas, and manufacturing. It manages the calibration of instruments and tools by tracking calibration schedules, generating Work Orders, and recording calibration results. The module ensures compliance with industry standards and regulatory requirements like FDA and ISO. By automating calibration processes, Maximo reduces errors, ensures accuracy, and maintains operational quality and safety.
6. How does Maximo handle Service Request Management, and why is it important?
Service Request Management in Maximo allows users to submit, track, and resolve service requests efficiently. It includes features like self-service portals, automated routing, and SLA tracking. When a request is submitted, Maximo assigns it to the appropriate team and tracks its progress until resolution. This functionality is crucial for managing internal and external service delivery, improving response times, and ensuring customer satisfaction. It also provides valuable data for analyzing service trends and identifying areas for improvement.
7. What is the role of Asset Reliability in Maximo, and how is it implemented?
Asset Reliability in Maximo focuses on improving the dependability and performance of critical assets. It involves tools like Failure Codes, Condition Monitoring, and Asset Health Insights to identify and mitigate reliability risks. By analyzing historical failure data and real-time sensor readings, Maximo helps organizations implement Reliability-Centered Maintenance (RCM) strategies. These strategies aim to balance preventive, predictive, and corrective maintenance to achieve optimal reliability at minimal cost.
8. How does Maximo support energy management and sustainability initiatives?
Maximo supports energy management by tracking energy usage and identifying inefficiencies in asset performance. It integrates with energy monitoring systems to collect data on electricity, water, and fuel consumption. By analyzing this data, Maximo helps organizations implement energy-saving measures, reduce emissions, and lower costs. Sustainability features, such as carbon tracking and waste management, enable companies to align their operations with environmental goals and comply with regulations. These capabilities make Maximo a valuable tool for organizations aiming to enhance their environmental performance.
9. Explain the concept of Multi-Tiered Locations in Maximo and their application.
Multi-Tiered Locations in Maximo allow users to define hierarchical relationships between locations, such as buildings, floors, and rooms. This feature is particularly useful for facilities management, where assets are distributed across multiple layers of a structure. For example, a hospital might use multi-tiered locations to manage equipment in different departments and floors. This hierarchy simplifies asset tracking, streamlines Work Order assignment, and provides better visibility into location-based asset performance.
10. How does Maximo handle complex procurement workflows for maintenance operations?
Maximo’s Procurement module supports complex workflows by integrating with Work Orders, inventory, and supplier management systems. It automates processes like requisition approval, purchase order generation, and vendor selection. Advanced features like supplier performance tracking and contract management ensure cost-effective and timely procurement. By providing a unified platform for procurement activities, Maximo reduces administrative overhead and ensures alignment with maintenance requirements.
11. What are the advantages of using Maximo Anywhere for mobile work management?
Maximo Anywhere enhances mobile work management by enabling field technicians to access and update Work Orders, asset details, and inventory data in real-time. Its offline functionality ensures continuous operation in remote areas without network connectivity. The application integrates features like barcode scanning, GPS, and photo capture, improving data accuracy and efficiency. By streamlining workflows and reducing manual tasks, Maximo Anywhere enhances field productivity, reduces delays, and improves service quality.
12. How does Maximo handle condition-based monitoring and maintenance?
Condition-Based Monitoring (CBM) in Maximo relies on IoT sensors and real-time data to assess asset conditions. It triggers maintenance activities only when specific thresholds, such as temperature or vibration levels, are exceeded. CBM minimizes unnecessary maintenance by focusing on actual asset conditions, reducing costs and extending asset life. Maximo’s CBM capabilities enable organizations to transition from reactive to proactive maintenance, improving operational efficiency and asset reliability.
13. What is the role of data analytics in Maximo, and how does it enhance asset management?
Data analytics in Maximo leverages historical and real-time data to provide insights into asset performance, maintenance trends, and operational efficiency. Tools like dashboards, KPIs, and predictive models enable organizations to identify inefficiencies, forecast failures, and optimize maintenance schedules. Advanced analytics, powered by AI, further enhances decision-making by uncovering hidden patterns and recommending actionable strategies. By integrating data analytics, Maximo empowers organizations to make data-driven decisions that improve asset utilization and reduce costs.
14. How does Maximo support disaster recovery and business continuity planning?
Maximo contributes to disaster recovery and business continuity by ensuring the availability of critical asset and operational data during emergencies. Its cloud deployment options provide robust backup and recovery capabilities, minimizing data loss and downtime. Maximo’s Work Order management and condition monitoring features help organizations prepare for and respond to disasters, such as equipment failures or natural calamities. By maintaining operational readiness, Maximo supports resilience and continuity in challenging situations.
15. What are the challenges of scaling Maximo for global enterprises, and how can they be addressed?
Scaling Maximo for global enterprises involves challenges like multi-language support, diverse regulatory compliance, and varying operational workflows. These can be addressed by leveraging Maximo’s multi-tenancy features, which allow separate configurations for different regions or business units. Customizable workflows and localization options ensure alignment with local requirements. Additionally, global implementation requires robust training programs, stakeholder engagement, and a phased rollout strategy to ensure successful adoption and scalability across the organization.
Course Schedule
Jul, 2025 | Weekdays | Mon-Fri | Enquire Now |
Weekend | Sat-Sun | Enquire Now | |
Aug, 2025 | Weekdays | Mon-Fri | Enquire Now |
Weekend | Sat-Sun | Enquire Now |
Related Courses
Related Articles
- The Role of DevOps in Modern Development Cycles
- PeopleSoft HR Training: Empowering HR Professionals
- Get Ahead with MB-260 Microsoft Customer Data Platform Training
- AmeTank: Revolutionizing Tank Design and Engineering in the Process Industry
- Boost Your Skills with Salesforce Service Cloud Consultant Training Course
Related Interview
- IBM Platform LSF Advanced Administration and Configuration for Linux (H023G) Training Interview Questions Answers
- PingFederate Interview Questions Answers
- Microsoft Power BI Interview Questions Answers
- AWS Data Engineering Training Interview Questions Answers
- AWS Certified Security Specialty Training Interview Questions Answers
Related FAQ's
- Instructor-led Live Online Interactive Training
- Project Based Customized Learning
- Fast Track Training Program
- Self-paced learning
- In one-on-one training, you have the flexibility to choose the days, timings, and duration according to your preferences.
- We create a personalized training calendar based on your chosen schedule.
- Complete Live Online Interactive Training of the Course
- After Training Recorded Videos
- Session-wise Learning Material and notes for lifetime
- Practical & Assignments exercises
- Global Course Completion Certificate
- 24x7 after Training Support
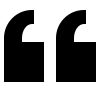