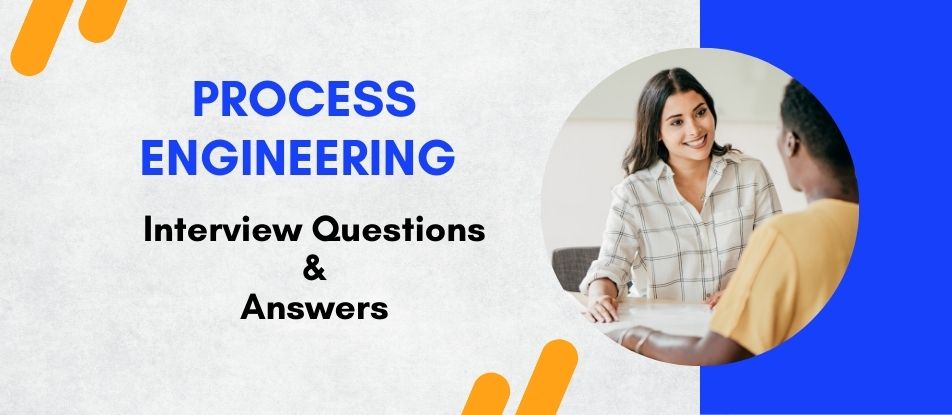
The Process Engineering training course equips participants with the knowledge and skills to design, analyze, and optimize industrial processes. Covering key topics such as process design, control systems, and safety protocols, this comprehensive program combines theoretical learning with practical applications. Ideal for engineers and technical professionals, the course ensures proficiency in enhancing efficiency, reducing costs, and improving overall process performance in various industries.
Process Engineering Interview Questions - For Intermediate
1. What is Process Engineering?
Process engineering involves designing, implementing, controlling, and optimizing industrial processes, particularly continuous ones within the chemical, petrochemical, agriculture, mineral processing, advanced material, food, pharmaceutical, and biotechnological industries.
2. Can you explain what a P&ID diagram is and its importance?
A Piping and Instrumentation Diagram (P&ID) shows the piping and related components of a physical process flow. It's crucial for the design and operation of process systems as it provides a detailed graphical representation of the actual process.
3. What are the key components of a distillation column?
Key components include the feed, reboiler, condenser, top and bottom products, trays or packing, and reflux drum. Each component plays a critical role in the separation process.
4. How do you perform a mass balance?
Mass balance involves accounting for the mass entering and leaving a system, ensuring mass in equals mass out, under steady state conditions. It’s fundamental in designing and analyzing processes.
5. What is the difference between batch and continuous processing?
Batch processing involves processing a fixed amount of material in steps over time, whereas continuous processing involves feeding and removing material simultaneously and continuously through the process.
6. What safety considerations are essential in process design?
Key safety considerations include ensuring the containment of hazardous materials, designing for overpressure scenarios through relief systems, maintaining ergonomic safety standards, and implementing fail-safes and redundancies.
7. Explain the term 'process optimization'.
Process optimization refers to refining a process to achieve better yields, improve quality, reduce costs, or minimize waste, often by using mathematical models and simulations.
8. What is a control loop in process control?
A control loop is a feedback mechanism used to control a process variable to a desired set point. It typically includes a sensor, controller, and actuator.
9. How do heat exchangers work, and what types are there?
Heat exchangers transfer heat between two or more fluids without them mixing. Types include shell and tube, plate, and air-cooled.
10. What are the principles of fluid mechanics that are applicable in process engineering?
Key principles include conservation of mass, momentum, and energy. Understanding these principles helps in designing equipment like pumps, compressors, and turbines.
11. What is the importance of material and energy balances in process engineering?
Material and energy balances are fundamental to process engineering as they provide a quantitative assessment of the materials and energy required in a process. They ensure that all inputs and outputs are accounted for, which is critical for process design, optimization, and sustainability.
12. What software tools are commonly used in process engineering?
Common tools include AutoCAD, MATLAB, Aspen Plus, HYSYS, and Microsoft Visio.
13. How do you ensure quality in a process?
Quality in processes can be ensured through rigorous testing, continuous monitoring, and adherence to standards such as ISO 9001.
14. What is Six Sigma, and how is it applied in process engineering?
Six Sigma is a set of techniques and tools for process improvement, aiming at reducing variability and defects. It involves the DMAIC methodology: Define, Measure, Analyze, Improve, and Control.
15. What role does environmental compliance play in process design?
Environmental compliance is critical to ensure that processes meet legal and ethical standards regarding emissions, waste management, and resource conservation.
16. Explain how pumps and compressors are selected for a given process.
Selection is based on fluid properties, flow rate requirements, pressure conditions, and efficiency considerations, among other factors.
17. What is CFD (Computational Fluid Dynamics), and how is it used in process engineering?
CFD is a tool used to simulate fluid flow, heat transfer, and related phenomena. It’s useful in designing and optimizing equipment and processes, such as reactors and separators.
18. What is a reactor, and what types are commonly used in the industry?
A reactor is a vessel designed to contain and control chemical reactions. Common types include batch, continuous stirred-tank, and plug flow reactors.
19. Can you explain the concept of 'scale-up' in process engineering?
Scale-up involves adapting a laboratory process to a production scale, addressing challenges like heat transfer differences, mixing issues, and kinetic changes.
20. What is a Process Flow Diagram (PFD) and how does it differ from a P&ID?
A PFD shows fewer details than a P&ID and focuses on major process streams, equipment, and flow paths. It is used in the early stages of process design.
Process Engineering Interview Questions - For Advanced
1. What are the key factors to consider in process design and how do they impact overall efficiency?
In process design, several key factors must be considered to ensure overall efficiency. These include material and energy balances, process control, equipment selection, and safety considerations. Material and energy balances ensure that all inputs and outputs are accounted for, which is critical for optimizing resource use. Process control involves maintaining the desired operation conditions, minimizing variability, and ensuring consistent product quality. Equipment selection impacts the operational efficiency, cost, and safety of the process. Lastly, safety considerations are paramount to prevent accidents and ensure compliance with regulations. These factors collectively ensure that the process operates smoothly, efficiently, and safely.
2. How does pinch analysis contribute to energy efficiency in process engineering?
Pinch analysis is a technique used to identify and minimize energy consumption in industrial processes. It involves plotting the temperature-enthalpy diagrams for hot and cold streams to find the 'pinch point,' which is the point of closest approach between these streams. By understanding this pinch point, engineers can optimize heat exchange networks to reduce the need for external heating and cooling. This leads to significant energy savings and reduces operating costs. Additionally, pinch analysis helps in designing processes that are more environmentally friendly by lowering the carbon footprint.
3. Describe the role of process simulation software in process engineering.
Process simulation software plays a crucial role in process engineering by allowing engineers to model and analyze complex processes before implementation. These tools can simulate various scenarios, optimize process conditions, and predict the performance of the process under different operating conditions. This helps in identifying potential issues early, reducing the risk of costly errors during actual implementation. Additionally, simulation software aids in designing more efficient and cost-effective processes, improving safety by allowing virtual testing of hazardous conditions, and providing a platform for training operators.
4. What are the challenges in scaling up a chemical process from the lab to industrial scale?
Scaling up a chemical process from the lab to industrial scale presents several challenges. One major challenge is maintaining the same reaction conditions and product quality as in the lab. Differences in heat and mass transfer rates, mixing efficiency, and reaction kinetics can significantly impact the process. Another challenge is dealing with increased production volumes, which may require larger equipment and different materials of construction. Additionally, safety hazards and environmental impacts become more pronounced at a larger scale, necessitating rigorous risk assessments and mitigation strategies. Economic considerations, such as capital investment and operating costs, also play a crucial role in the scale-up process.
5. Explain the concept of process intensification and its benefits.
Process intensification involves developing innovative technologies to make chemical processes more efficient, economical, and sustainable. This can be achieved by designing equipment and processes that reduce the size, energy consumption, and waste production while increasing throughput and product quality. Benefits of process intensification include reduced capital and operating costs, lower environmental impact, and improved safety due to smaller equipment and less hazardous materials. Additionally, intensified processes often offer enhanced control and flexibility, enabling faster response to market demands and the development of new products and processes.
6. How is Six Sigma methodology applied in process engineering?
Six Sigma is a data-driven methodology used to improve process performance by reducing variability and defects. In process engineering, Six Sigma is applied through a structured approach known as DMAIC: Define, Measure, Analyze, Improve, and Control. During the Define phase, the project goals and customer requirements are identified. The Measure phase involves collecting data on current process performance. In the Analyze phase, data is examined to identify root causes of variability and defects. The Improve phase focuses on implementing solutions to address these root causes. Finally, the Control phase ensures that the improvements are sustained over time through monitoring and control plans. Six Sigma helps in achieving higher quality, efficiency, and customer satisfaction.
7. What are the common types of reactors used in chemical engineering and their applications?
Common types of reactors used in chemical engineering include batch reactors, continuous stirred-tank reactors (CSTR), plug flow reactors (PFR), and packed bed reactors. Batch reactors are versatile and suitable for small-scale production and research. CSTRs are used for continuous production and are ideal for reactions requiring constant mixing and uniform temperature. PFRs, with their tubular design, are used for reactions with high conversion rates and are common in large-scale production. Packed bed reactors, containing solid catalysts, are used in processes like catalytic cracking and gas purification. Each reactor type has specific applications based on reaction kinetics, scale, and desired outcomes.
8. How do advanced control systems improve process operations?
Advanced control systems, such as Distributed Control Systems (DCS) and Supervisory Control and Data Acquisition (SCADA), improve process operations by providing real-time monitoring and control. These systems enable precise regulation of process variables like temperature, pressure, flow rate, and composition, leading to enhanced process stability and product quality. They also facilitate automation, reducing the need for manual intervention and minimizing human error. Advanced control systems can integrate with optimization algorithms to continuously adjust process conditions for optimal performance. Additionally, they provide valuable data for predictive maintenance and troubleshooting, further improving efficiency and reliability.
9. Discuss the importance of HAZOP studies in process safety management.
HAZOP (Hazard and Operability) studies are critical in process safety management as they systematically examine potential hazards and operational issues in process design and operation. By using a structured approach to identify deviations from normal operation and their possible causes, HAZOP studies help in recognizing and mitigating risks before they lead to incidents. The process involves a multidisciplinary team that reviews the design and operation using guidewords to explore different scenarios. HAZOP studies contribute to safer processes by ensuring that all potential hazards are addressed, leading to improved safety, compliance with regulations, and protection of personnel and the environment.
10. What is the role of computational fluid dynamics (CFD) in process engineering?
Computational Fluid Dynamics (CFD) plays a significant role in process engineering by allowing engineers to simulate and analyze fluid flow, heat transfer, and chemical reactions within process equipment. CFD provides detailed insights into flow patterns, temperature distribution, and mixing efficiency, which are critical for optimizing reactor design, heat exchangers, and other process units. By using CFD, engineers can identify potential issues such as dead zones, hotspots, and pressure drops, and make informed decisions to enhance process performance. Additionally, CFD helps in designing more efficient and cost-effective equipment, reducing the need for physical prototyping and experiments.
Course Schedule
Mar, 2025 | Weekdays | Mon-Fri | Enquire Now |
Weekend | Sat-Sun | Enquire Now | |
Apr, 2025 | Weekdays | Mon-Fri | Enquire Now |
Weekend | Sat-Sun | Enquire Now |
Related Courses
Related Articles
Related Interview
- MB-800: Microsoft Dynamics 365 Business Central Functional Consultant Interview Questions
- Palantir Foundry Data Analyst Training Interview Questions Answers
- ServiceNow PPM Interview Questions Answers
- Oracle Fusion SCM Training Interview Questions Answers
- Microsoft Azure Active Directory Interview Questions Answers
Related FAQ's
- Instructor-led Live Online Interactive Training
- Project Based Customized Learning
- Fast Track Training Program
- Self-paced learning
- In one-on-one training, you have the flexibility to choose the days, timings, and duration according to your preferences.
- We create a personalized training calendar based on your chosen schedule.
- Complete Live Online Interactive Training of the Course
- After Training Recorded Videos
- Session-wise Learning Material and notes for lifetime
- Practical & Assignments exercises
- Global Course Completion Certificate
- 24x7 after Training Support
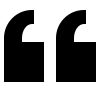