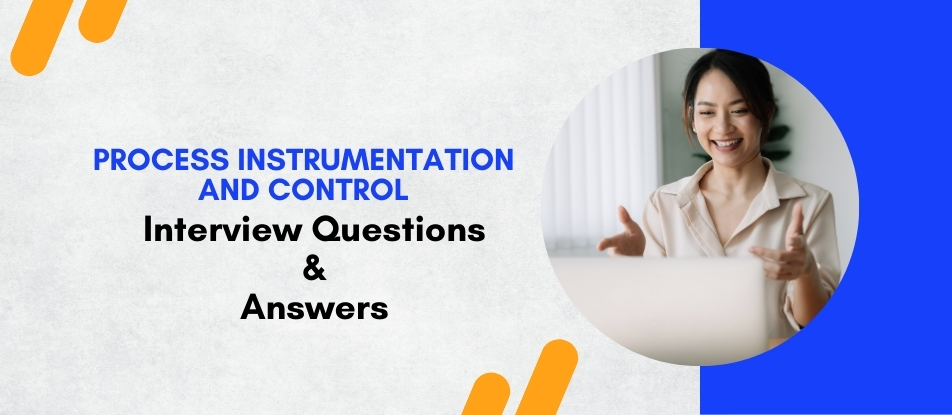
Process Instrumentation and Control Online Training provides a comprehensive understanding of the key principles and applications of process control systems. This course covers essential topics like sensors, transmitters, control loops, PLCs, and SCADA systems used in industrial automation. Participants will learn how to monitor, measure, and control process variables such as temperature, pressure, flow, and level, ensuring optimized plant performance. Designed for engineers, technicians, and industry professionals, this training combines theory with practical insights, empowering learners to enhance operational efficiency, reduce downtime, and maintain system reliability across various industries.
Process Instrumentation and Control Interview Questions Answers - For Intermediate
1. What is the primary difference between open-loop and closed-loop control systems?
Open-loop systems operate without feedback, executing control actions based solely on input commands. Closed-loop systems use feedback from sensors to adjust actions dynamically, ensuring the process variable meets the desired setpoint, and enhancing accuracy and stability.
2. Explain the function of a PID controller in process control.
A PID controller adjusts process inputs based on three terms: Proportional (reacts to current error), Integral (accumulates past errors), and Derivative (predicts future errors). This combination ensures precise control by minimizing the difference between the setpoint and the process variable.
3. What are the common types of process sensors used for temperature measurement?
Common temperature sensors include Thermocouples, Resistance Temperature Detectors (RTDs), Thermistors, and Infrared sensors. Each type varies in sensitivity, range, and application suitability, enabling accurate temperature monitoring in diverse industrial processes.
4. Describe the purpose of calibration in process instrumentation.
Calibration ensures that instruments provide accurate measurements by comparing them against standard references. Regular calibration identifies and corrects deviations, maintaining measurement precision and reliability critical for process control and safety.
5. What is a transmitter in process instrumentation, and what role does it play?
A transmitter converts sensor signals (often analog) into standardized signals (like 4-20 mA) for communication to control systems. It ensures signal integrity over distances, enabling accurate data transmission for monitoring and control purposes.
6. Explain the concept of process variables and provide three examples.
A process variable is a measurable parameter in a process, essential for monitoring and control. Examples include temperature, pressure, flow rate, level, and pH. Managing these variables ensures the process operates within the desired specifications.
7. What is the significance of HART communication in instrumentation?
HART (Highway Addressable Remote Transducer) allows simultaneous digital and analog communication over standard 4-20 mA lines. It facilitates device configuration, diagnostics, and data exchange without disrupting the primary analog signal, enhancing system flexibility.
8. Differentiate between primary and secondary elements in process instrumentation.
Primary elements directly interact with the process, measuring variables like temperature or pressure. Secondary elements receive signals from primary devices, processing and transmitting data to control systems for monitoring and control actions.
9. What are the key components of a typical control loop?
A control loop consists of a sensor (measures process variable), transmitter (sends signal), controller (computes adjustments), and final control element (like a valve or actuator) that modifies the process to achieve the setpoint.
10. Describe the role of a flow meter in process control.
A flow meter measures the rate of fluid movement within a system. Accurate flow measurement is crucial for process efficiency, quality control, and maintaining balance in chemical reactions, ensuring consistent and safe operations.
11. What is deadband in control systems, and why is it important?
Deadband is a range around the setpoint where no control action occurs. It prevents unnecessary adjustments due to minor fluctuations, reducing wear on actuators and avoiding system instability from excessive control activity.
12. Explain the principle of operation of a Differential Pressure Transmitter.
A Differential Pressure Transmitter measures the difference in pressure between two points. It’s commonly used to determine flow rates, level measurements, or filter conditions by translating pressure differences into electrical signals for monitoring.
13. What are the advantages of using smart instruments in process control?
Smart instruments offer features like self-diagnostics, digital communication, enhanced accuracy, remote configuration, and data logging. These capabilities improve system reliability, simplify maintenance, and enable more efficient and flexible control strategies.
14. How does an RTD differ from a thermocouple in temperature measurement?
RTDs (Resistance Temperature Detectors) measure temperature based on resistance changes, offering high accuracy and stability. Thermocouples generate a voltage from temperature differences, suitable for wide ranges and rapid responses but generally less precise than RTDs.
15. What is loop tuning, and why is it essential in control systems?
Loop tuning involves adjusting controller parameters (like PID settings) to achieve optimal system performance. Proper tuning ensures stability, minimizes overshoot, and improves response time, enhancing overall control system effectiveness.
16. Describe the function of a level transmitter in a storage tank.
A level transmitter monitors the liquid or solid level within a storage tank. It provides real-time data to control systems to manage filling, emptying, and maintaining appropriate levels, preventing overflow or shortages.
17. What is signal conditioning, and why is it necessary in instrumentation?
Signal conditioning modifies sensor outputs to suitable forms for processing, such as amplification, filtering, or converting signal types. It ensures accurate and reliable data transmission, improving measurement integrity and control system performance.
18. Explain the term 'process control loop stability'.
Process control loop stability refers to the system’s ability to return to equilibrium after a disturbance without oscillations or divergent behavior. Stable loops maintain consistent control, ensuring reliable and predictable process performance.
19. What is a field bus system, and how does it benefit process control?
A field bus system is a digital communication network connecting field devices like sensors and actuators to control systems. It offers high data transfer rates, reduced wiring, improved diagnostics, and enhanced integration, increasing system efficiency and flexibility.
20. Describe the importance of redundancy in safety instrumented systems (SIS).
Redundancy in SIS ensures reliability by having multiple layers or copies of critical components. If one component fails, others maintain system integrity, preventing accidents and ensuring safe operation in hazardous industrial environments.
Process Instrumentation and Control Interview Questions Answers - For Advanced
1. Explain the role of a PID controller in process control and how each component (Proportional, Integral, Derivative) affects system behavior.
A PID controller adjusts process variables by calculating an error value and applying proportional, integral, and derivative terms. The Proportional term reduces the error, the Integral eliminates steady-state error, and the Derivative anticipates future error, enhancing stability and response time.
2. Describe the differences between open-loop and closed-loop control systems, including their advantages and limitations in industrial applications.
Open-loop systems operate without feedback, suitable for simple, predictable processes but prone to disturbances. Closed-loop systems use feedback to adjust actions, offering higher accuracy and adaptability but are more complex and may require tuning.
3. What is the HART communication protocol, and how does it enhance field device communication in process control systems?
HART (Highway Addressable Remote Transducer) is a hybrid analog-digital protocol allowing simultaneous analog signals and digital communication. It enhances device diagnostics, configuration, and data exchange without additional wiring, improving system integration and maintenance.
4. Explain the concept of loop tuning in PID controllers and describe the Ziegler-Nichols method for determining optimal PID parameters.
Loop tuning adjusts PID parameters for desired performance. The Ziegler-Nichols method involves setting I and D to zero, increasing P until oscillations occur (ultimate gain), and then calculating P, I, and D based on the oscillation period to achieve balanced responsiveness and stability.
5. Discuss the importance of Instrument Performance Monitoring (IPM) and the techniques used to ensure accurate and reliable instrumentation in process control.
IPM ensures instruments operate correctly, maintaining data accuracy and process safety. Techniques include calibration, regular maintenance, trend analysis, redundancy, and diagnostics to detect drift, wear, and failures, thereby minimizing downtime and errors.
6. What are the primary differences between Intrinsic Safety and explosion-proof protection methods for instrumentation in hazardous areas?
Intrinsic Safety limits electrical energy to prevent ignition, suitable for low-power devices. Explosion-proof enclosures contain any explosions, allowing higher power devices. The choice depends on the specific hazardous environment and equipment requirements.
7. Describe Model Predictive Control (MPC) and its advantages over traditional PID control in complex industrial processes.
MPC uses a dynamic model to predict future process behavior and optimize control actions over a horizon. It handles multivariable interactions and constraints better than PID, improving efficiency and stability in complex, nonlinear processes.
8. Explain the significance of loop bandwidth in control systems and how it affects the system’s responsiveness and stability.
Loop bandwidth defines the frequency range where the controller effectively responds. Higher bandwidth improves responsiveness but risks instability due to noise and phase lag. Optimal bandwidth balances speed and stability for reliable control.
9. How do smart transmitters differ from traditional transmitters in process instrumentation, and what benefits do they offer in modern control systems?
Smart transmitters integrate digital communication, diagnostics, and configuration capabilities, unlike analog-only traditional transmitters. They offer enhanced accuracy, easier integration, remote monitoring, and predictive maintenance, increasing overall system efficiency.
10. Discuss the application of Distributed Control Systems (DCS) in process industries and their advantages compared to centralized control architectures.
DCS distributes control functions across multiple controllers interconnected via a network, enhancing scalability, reliability, and fault tolerance. Compared to centralized systems, DCS offers better real-time processing, easier maintenance, and improved flexibility for complex industrial processes.
Course Schedule
Jul, 2025 | Weekdays | Mon-Fri | Enquire Now |
Weekend | Sat-Sun | Enquire Now | |
Aug, 2025 | Weekdays | Mon-Fri | Enquire Now |
Weekend | Sat-Sun | Enquire Now |
Related Courses
Related Articles
Related Interview
- DevOps Interview Questions and Answers
- IBM Maximo Application Suite Training Interview Questions Answers
- Dynamics 365: Supply Chain Management Functional Consultant Expert (MB-335) Training Interview Questions Answers
- SmartPlant P&ID Interview Questions Answers
- Certified Threat Intelligence Analyst (CTIA) Training Interview Questions Answers
Related FAQ's
- Instructor-led Live Online Interactive Training
- Project Based Customized Learning
- Fast Track Training Program
- Self-paced learning
- In one-on-one training, you have the flexibility to choose the days, timings, and duration according to your preferences.
- We create a personalized training calendar based on your chosen schedule.
- Complete Live Online Interactive Training of the Course
- After Training Recorded Videos
- Session-wise Learning Material and notes for lifetime
- Practical & Assignments exercises
- Global Course Completion Certificate
- 24x7 after Training Support
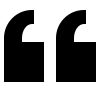