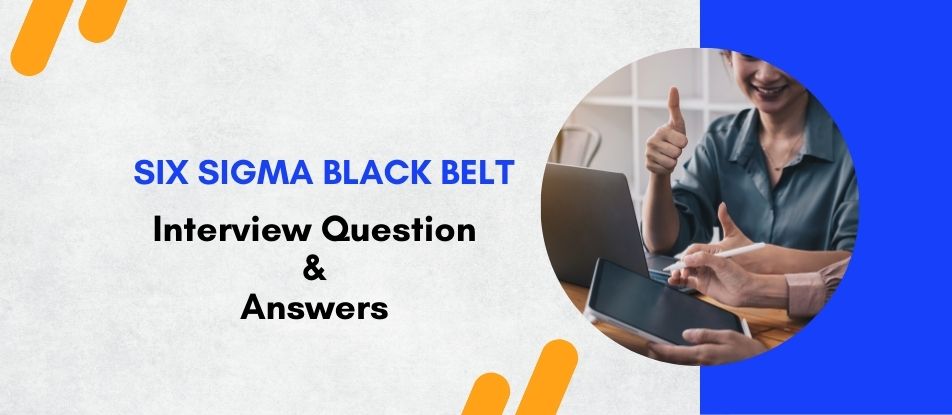
The Lean Six Sigma Black Belt training is an advanced program designed to equip professionals with in-depth knowledge and skills in process improvement and quality management. The course covers advanced statistical analysis, project management, and leadership techniques. Participants will learn to identify, analyze, and solve complex business problems, leading to increased efficiency and reduced costs. Ideal for those seeking to lead Six Sigma projects and drive organizational excellence.
Six Sigma Black Belt Interview Questions - For Intermediate
1. What does the term "Six Sigma" refer to?
Six Sigma is a set of techniques and tools for process improvement, aiming to reduce variability in processes and ensure quality control, with a goal of less than 3.4 defects per million opportunities.
2. What are the main differences between a Green Belt and a Black Belt in Lean Six Sigma?
Green Belts are employees who take up Lean Six Sigma implementation along with their other job responsibilities, whereas Black Belts are full-time professionals dedicated to implementing Lean Six Sigma principles.
3. Can you explain what FMEA is and its importance?
Failure Modes and Effects Analysis (FMEA) is a systematic approach used to identify and analyze potential failures in a product or process before they occur, prioritizing them based on their severity, occurrence, and detectability.
4. How do you define a "good" metric in Lean Six Sigma?
A good metric is Specific, Measurable, Achievable, Relevant, and Time-bound (SMART), and it directly reflects process performance and customer satisfaction.
5. What is the importance of the Kano Model in Lean Six Sigma?
The Kano Model is used to categorize customer preferences into must-be, one-dimensional, and delighter factors, helping in prioritizing features based on customer satisfaction.
6. Describe the process capability index and its significance.
The process capability index (Cp and Cpk) measures a process's ability to produce output within specification limits, indicating the process's efficiency and stability.
7. What role does change management play in Lean Six Sigma projects?
Change management is critical for addressing resistance, ensuring stakeholder engagement, and securing buy-in for changes, thus facilitating smooth implementation and adoption of improvements.
8. How would you handle a team member who is resistant to change?
By communicating the benefits, providing training and support, involving them in decision-making, and gradually introducing changes to ease the transition.
9. What is a Gemba walk, and why is it important?
A Gemba walk involves going to the place where work is done, observing the process, and talking with workers to identify waste and opportunities for improvement.
10. How do you prioritize projects in a multi-project environment?
Projects are prioritized based on their alignment with strategic goals, potential impact on key metrics, resource availability, and urgency.
11. What is "Just-In-Time" (JIT) production, and how does it relate to Lean?
JIT is a production strategy that strives to improve a business's return on investment by reducing in-process inventory and associated carrying costs, closely aligned with Lean's waste reduction focus.
12. Can you explain the concept of "Total Productive Maintenance" (TPM)?
TPM is a holistic approach to equipment maintenance that aims to achieve perfect production by minimizing breakdowns, small stops or slow running, and defects.
13. What does "voice of the customer" (VOC) mean, and why is it important?
VOC refers to the process of capturing customers' requirements, preferences, and experiences to guide improvement efforts and ensure the product/service meets or exceeds their expectations.
14. What are common tools used in Lean Six Sigma for data analysis?
Tools include statistical software, Pareto charts, cause and effect diagrams, control charts, and process mapping.
15. What is the impact of Lean Six Sigma on company culture?
It fosters a culture of continuous improvement, employee empowerment, customer focus, and quality awareness throughout the organization.
16. Describe a time when you had to overcome a significant challenge in a Lean Six Sigma project.
This question assesses problem-solving skills and resilience, looking for an example of identifying a problem, analyzing root causes, implementing a solution, and monitoring the outcome.
17. How do you measure the success of a Lean Six Sigma project?
Success is measured by the extent to which project goals were achieved, including improvements in process efficiency, quality, customer satisfaction, and financial savings.
18. What is "quick win" in the context of Lean Six Sigma, and why is it important?
Quick wins are improvements that can be implemented rapidly and easily, providing immediate benefits and building momentum and support for the project.
19. How can Lean Six Sigma be applied in non-manufacturing environments?
By focusing on reducing waste, improving processes, and enhancing efficiency in areas such as service delivery, administration, and operations.
20. What is the importance of benchmarking in Lean Six Sigma?
Benchmarking involves comparing processes and performance metrics to industry bests and best practices from other companies, aiming to identify areas for improvement and setting standards.
Six Sigma Black Belt Interview Questions - For Advanced
1. What are the primary tools used in Lean Six Sigma for process improvement?
Lean Six Sigma uses a variety of tools to enhance process improvement. These include:
- DMAIC (Define, Measure, Analyze, Improve, Control): A structured problem-solving methodology used to improve existing processes.
- Value Stream Mapping: A visual tool to analyze and design the flow of materials and information required to bring a product or service to a consumer.
- Root Cause Analysis: Techniques like the 5 Whys and Fishbone Diagram to identify the underlying causes of defects or problems.
- Control Charts: Statistical tools used to monitor process stability and control over time.
- Pareto Analysis: A method to identify the most significant factors in a dataset and prioritize problem-solving efforts.
- Failure Mode and Effects Analysis (FMEA): A proactive tool for identifying potential failure modes and their impacts, allowing for preventative actions.
- Design of Experiments (DOE): A systematic method to determine the relationship between factors affecting a process and the output of that process.
2. How does the Lean Six Sigma approach integrate Lean and Six Sigma methodologies?
Lean Six Sigma integrates the principles of Lean and Six Sigma to improve processes by eliminating waste and reducing variability. Lean focuses on improving process flow and efficiency by eliminating non-value-added activities (waste), while Six Sigma emphasizes reducing process variation and defects through statistical analysis. The integration of these methodologies allows organizations to achieve significant improvements in quality, efficiency, and customer satisfaction. Lean tools like 5S, Kaizen, and Value Stream Mapping are used alongside Six Sigma tools like DMAIC, statistical analysis, and control charts to provide a comprehensive approach to process improvement.
3. Describe the role of a Lean Six Sigma Black Belt in an organization.
A Lean Six Sigma Black Belt plays a critical role in an organization by leading complex improvement projects and mentoring Green Belts. Responsibilities include:
- Project Leadership: Leading cross-functional teams to complete high-impact projects using the DMAIC methodology.
- Data Analysis: Applying advanced statistical tools to analyze data, identify root causes, and develop solutions.
- Coaching and Mentoring: Guiding and supporting Green Belts and other team members in Lean Six Sigma methodologies and tools.
- Change Management: Facilitating organizational change by promoting a culture of continuous improvement and helping stakeholders adapt to new processes.
- Strategic Planning: Aligning Lean Six Sigma projects with organizational goals and strategies to ensure maximum impact on business performance.
4. What is the importance of statistical process control (SPC) in Lean Six Sigma?
Statistical Process Control (SPC) is crucial in Lean Six Sigma as it provides a method for monitoring and controlling processes through statistical techniques. SPC helps in:
- Detecting Variability: Identifying and understanding variations in processes to maintain consistency and predictability.
- Preventing Defects: Monitoring process performance in real-time to detect and address issues before they result in defects.
- Improving Quality: Using control charts and other SPC tools to ensure processes remain within specified control limits, thereby improving product quality.
- Driving Continuous Improvement: Providing data-driven insights that inform decision-making and support ongoing process enhancements.
5. Explain the concept of Design for Six Sigma (DFSS) and its significance.
Design for Six Sigma (DFSS) is a methodology focused on designing products and processes that meet customer requirements and achieve Six Sigma quality levels from the outset. Its significance lies in:
- Proactive Quality Management: Incorporating quality principles in the design phase to prevent defects and ensure robustness.
- Customer-Centric Approach: Utilizing tools like Voice of the Customer (VOC) to understand and incorporate customer needs into the design.
- Innovation and Efficiency: Applying DFSS principles to develop innovative solutions that are efficient, cost-effective, and capable of meeting high-quality standards.
- Lifecycle Benefits: Enhancing the overall product lifecycle by ensuring reliability, maintainability, and sustainability from the beginning.
6. How does the Failure Mode and Effects Analysis (FMEA) tool work in Lean Six Sigma?
Failure Mode and Effects Analysis (FMEA) is a systematic tool used to identify and prioritize potential failure modes in a process or product. It works by:
- Identifying Failure Modes: Listing all possible ways a process or product can fail.
- Assessing Risk: Evaluating the severity, occurrence, and detectability of each failure mode to calculate a Risk Priority Number (RPN).
- Prioritizing Actions: Using the RPN to prioritize which failure modes require corrective actions to mitigate risks.
- Implementing Solutions: Developing and implementing actions to reduce or eliminate high-risk failure modes, followed by monitoring their effectiveness.
7. What is the role of hypothesis testing in Lean Six Sigma projects?
Hypothesis testing plays a critical role in Lean Six Sigma projects by providing a method for making data-driven decisions. Its role includes:
- Testing Assumptions: Validating or refuting assumptions about process behaviors and relationships between variables.
- Analyzing Data: Using statistical tests to determine if observed differences or relationships are statistically significant.
- Driving Improvements: Informing process improvement efforts by identifying which factors have a significant impact on process performance.
- Reducing Variation: Helping to understand the sources of variation and their effects on the process, leading to more targeted improvement strategies.
8. Describe the DMAIC process and its phases in Lean Six Sigma.
The DMAIC process is a structured problem-solving methodology used in Lean Six Sigma, consisting of five phases:
- Define: Identifying the problem, setting project goals, and defining customer requirements.
- Measure: Collecting data to establish baselines, measure current performance, and identify key process input variables.
- Analyze: Using data analysis and statistical tools to identify root causes of defects or problems.
- Improve: Developing and implementing solutions to address root causes, followed by testing and validating improvements.
- Control: Establishing control measures to sustain improvements, monitoring process performance, and implementing standard operating procedures.
9. What is the significance of the Control phase in the DMAIC methodology?
The Control phase is significant in the DMAIC methodology as it ensures that improvements are sustained over time. Its importance includes:
- Maintaining Gains: Implementing control mechanisms to ensure that process improvements are maintained and not reverted.
- Monitoring Performance: Using control charts and other tools to continuously monitor process performance and detect any deviations.
- Standardizing Processes: Establishing standard operating procedures (SOPs) and documentation to ensure consistency and repeatability.
- Training and Communication: Educating employees on new processes and changes, and ensuring effective communication across the organization.
10. How can Lean Six Sigma be applied in service industries, and what are its benefits?
Lean Six Sigma can be effectively applied in service industries to improve efficiency, quality, and customer satisfaction. Its application includes:
- Streamlining Processes: Identifying and eliminating waste in service processes, such as reducing waiting times and improving workflow.
- Improving Quality: Using Six Sigma tools to reduce errors and variability in service delivery, leading to higher quality and reliability.
- Enhancing Customer Experience: Focusing on customer needs and feedback to enhance service offerings and ensure customer satisfaction.
- Increasing Efficiency: Applying Lean principles to optimize resource utilization, reduce costs, and improve overall operational efficiency.
- Driving Continuous Improvement: Creating a culture of continuous improvement where employees are engaged in identifying and implementing improvements.
The benefits of Lean Six Sigma in service industries include increased customer loyalty, reduced operational costs, improved employee morale, and a stronger competitive position in the market.
Course Schedule
Apr, 2025 | Weekdays | Mon-Fri | Enquire Now |
Weekend | Sat-Sun | Enquire Now | |
May, 2025 | Weekdays | Mon-Fri | Enquire Now |
Weekend | Sat-Sun | Enquire Now |
Related Courses
Related Articles
Related Interview
Related FAQ's
- Instructor-led Live Online Interactive Training
- Project Based Customized Learning
- Fast Track Training Program
- Self-paced learning
- In one-on-one training, you have the flexibility to choose the days, timings, and duration according to your preferences.
- We create a personalized training calendar based on your chosen schedule.
- Complete Live Online Interactive Training of the Course
- After Training Recorded Videos
- Session-wise Learning Material and notes for lifetime
- Practical & Assignments exercises
- Global Course Completion Certificate
- 24x7 after Training Support
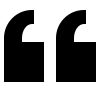