-software-interview-questions-answers.jpg)
Enhance your expertise with our SmartPlant® 3D (SP3D) Software Online Training Course. Designed for engineers and designers, this comprehensive program covers modeling, design workflows, and project management using SP3D. Learn through interactive modules, hands-on exercises, and expert guidance to streamline your plant design processes. Elevate your skills and boost productivity with flexible, accessible online learning.
SmartPlant® 3D (SP3D) Software Interview Questions Answers - For Intermediate
1. What are the primary modules within SP3D and their functions?
SP3D comprises modules like Piping, Equipment, Structural, Instrumentation, and Electrical. Each module allows users to design and model respective components in 3D, ensuring integration and coordination across disciplines. This modular approach facilitates efficient project management, accurate visualization, and streamlined collaboration among engineering teams.
2. How does SP3D handle data integration with other engineering software?
SP3D integrates data through standard interfaces like IFC, DXF, and XML. It supports APIs for custom integrations and utilizes Common Data Environment (CDE) for centralized data management. This ensures seamless data exchange with software like AutoCAD, Microsoft Office, and ERP systems, enhancing interoperability and reducing data redundancy.
3. Explain the role of Project Setup in SP3D.
Project Setup in SP3D involves defining project parameters, including units, templates, and standards. It configures project folders, assigns roles, and sets up data management protocols. Proper setup ensures consistency, facilitates team collaboration, and establishes a structured environment for efficient project execution and data integrity.
4. What is the significance of isometric drawings in SP3D?
Isometric drawings in SP3D provide detailed, three-dimensional representations of piping systems. They are essential for fabrication, installation, and maintenance, offering clear visualization of pipe routes, connections, and components. SP3D automates isometric generation, ensuring accuracy and consistency, thereby reducing errors and enhancing communication among stakeholders.
5. Describe the process of creating a 3D model for piping in SP3D.
Creating a piping model in SP3D involves defining the project structure, placing components like pipes, fittings, and supports, and routing pipes based on design specifications. Users utilize tools for alignment, snapping, and validation. The software ensures adherence to standards, enabling accurate and efficient 3D representation of the piping network.
6. How does SP3D manage design standards and templates?
SP3D manages design standards through predefined templates and rule sets that enforce company or industry standards. Templates include predefined settings for components, drawings, and reports. Users can customize these templates to maintain consistency across projects, ensuring compliance and reducing the likelihood of design discrepancies.
7. What are the key features of SP3D’s clash detection capabilities?
SP3D’s clash detection identifies geometric conflicts between different disciplines, such as piping and structural elements. It uses rule-based algorithms to automatically detect clashes, prioritize issues, and generate reports. This proactive approach minimizes rework, ensures design integrity, and facilitates timely resolution of conflicts during the design phase.
8. Explain the use of isometric templates in SP3D.
Isometric templates in SP3D define the formatting and standards for isometric drawings, including line styles, symbols, and annotations. They ensure consistency across all isometrics, adhere to industry standards, and streamline the creation process. Templates can be customized to meet specific project requirements, enhancing clarity and professionalism in documentation.
9. How does SP3D support collaboration among multidisciplinary teams?
SP3D supports collaboration through centralized data management, role-based access, and real-time updates. It integrates with Common Data Environment (CDE) systems, enabling seamless information sharing. Features like project-wide search, version control, and concurrent engineering tools ensure all team members work with the latest data, enhancing coordination and reducing conflicts.
10. What is the purpose of the Equipment module in SP3D?
The Equipment module in SP3D allows users to model, catalog, and manage equipment within the plant design. It includes features for placing equipment, defining properties, and linking to piping and instrumentation. This module ensures accurate representation of equipment placement, facilitates maintenance planning, and integrates seamlessly with other design disciplines.
11. Describe the workflow for generating reports in SP3D.
Generating reports in SP3D involves selecting the desired report type, configuring report parameters, and extracting data from the model. Users can customize templates, filter information, and automate report generation. SP3D supports various report formats, enabling comprehensive documentation for project management, compliance, and stakeholder communication.
12. How does SP3D handle revisions and version control?
SP3D manages revisions through integrated version control systems that track changes, maintain historical data, and manage document versions. Users can check in/check out models, compare revisions, and revert to previous states if needed. This ensures data integrity, facilitates audit trails, and supports collaborative workflows without conflicting modifications.
13. What customization options are available in SP3D for user-specific needs?
SP3D offers customization through scripting, APIs, and configurable templates. Users can create custom tools, automate repetitive tasks, and modify interface elements to suit specific workflows. Additionally, the software supports user-defined properties and standards, allowing tailored solutions that enhance productivity and align with organizational requirements.
14. Explain the integration of SP3D with Asset Lifecycle Management (ALM).
SP3D integrates with Asset Lifecycle Management systems by linking design data to asset information throughout its lifecycle. This connection facilitates seamless transitions from design to construction, operation, and maintenance. Integration ensures accurate asset tracking, enhances data consistency, and supports informed decision-making across all phases of the asset’s lifecycle.
15. What are the benefits of using SP3D’s automatic routing for piping?
SP3D’s automatic routing optimizes pipe paths based on design rules, constraints, and space availability. It reduces manual effort, ensures compliance with standards, and minimizes routing errors. Automatic routing enhances efficiency, accelerates project timelines, and ensures optimal use of space and resources within the plant design.
16 How does SP3D support the creation of structural models?
SP3D supports structural modeling by providing tools to create and manage structural elements like beams, columns, and foundations. It allows for the integration of structural designs with piping and equipment models, ensuring alignment and stability. The software facilitates detailed analysis, visualization, and documentation of structural components within the overall plant design.
17. Describe the role of the Instrumentation module in SP3D.
The Instrumentation module in SP3D manages the placement and integration of instrumentation devices within the plant design. It includes tools for defining instrument properties, connecting to piping and electrical systems, and ensuring compliance with control system requirements. This module ensures accurate representation of instrumentation, supporting effective monitoring and control of plant operations.
18. What is the importance of template management in maintaining consistency in SP3D projects?
Template management ensures that all project elements adhere to predefined standards and formats, promoting uniformity across designs and documentation. Consistent templates reduce errors, facilitate easier collaboration, and streamline training for new users. Effective template management enhances overall project quality and efficiency by maintaining standardization throughout the project lifecycle.
19. How does SP3D facilitate the creation of detailed fabrication drawings?
SP3D generates detailed fabrication drawings by extracting precise 3D model data, including dimensions, annotations, and component specifications. It automates drawing creation, ensuring accuracy and consistency. Users can customize drawing templates, apply standards, and include necessary details for fabrication, streamlining the transition from design to manufacturing processes.
20. Explain the use of the SmartPlant Foundation about SP3D.
SmartPlant Foundation serves as the data management backbone for SP3D, providing a centralized repository for project data. It ensures data integrity, supports collaboration, and facilitates access control. Integration with SP3D allows for efficient data sharing, versioning, and consistency across all project disciplines, enhancing overall project coordination and management.
SmartPlant® 3D (SP3D) Software Interview Questions Answers - For Advanced
1. How does SmartPlant® 3D handle data interoperability with other engineering software platforms?
SmartPlant® 3D utilizes industry-standard formats like IFC, STEP, and XML for seamless data exchange. It supports APIs and integrates with databases such as Oracle and SQL Server, enabling real-time collaboration. The software's interoperability features ensure consistency across various engineering tools, facilitating efficient project workflows and minimizing data loss or duplication during transitions between different platforms.
2. Explain the process of customizing user interfaces in SP3D to enhance workflow efficiency.
Customizing SP3D user interfaces involves using the Interface Configuration Editor to modify toolbars, menus, and panels. Users can create personalized workspace layouts, assign shortcuts, and integrate custom tools or scripts. Additionally, leveraging the SP3D SDK allows for deeper customization through programming, enabling tailored workflows that align with specific project requirements and improve overall productivity.
3. What are the key steps in performing clash detection within SP3D, and how are conflicts resolved?
Clash detection in SP3D involves defining clash rules, selecting relevant model components, and running the clash analysis tool. The software identifies spatial conflicts between elements like pipes and structures. Resolving conflicts typically requires adjusting the design within SP3D, such as repositioning components or altering specifications. Collaborative review processes and automated reporting help address and document clash resolutions effectively.
4. Describe the integration of P&ID models with SP3D and its significance in the design process.
Integration of P&ID models with SP3D is achieved through linking databases and using SmartPlant® P&ID. This connection ensures that piping and instrumentation designs are accurately reflected in the 3D model. It facilitates consistency, reduces errors, and streamlines updates. The integration is crucial for maintaining alignment between process diagrams and 3D layouts, enhancing overall design accuracy and project coordination.
5. How does SP3D support parametric modeling, and what are its benefits in complex plant design?
SP3D supports parametric modeling by allowing designers to define relationships and constraints between model elements. Parameters such as dimensions, materials, and connections are interlinked, enabling automatic updates when changes occur. This approach enhances flexibility, ensures design consistency, and reduces manual adjustments. In complex plant designs, parametric modeling improves accuracy and accelerates the modification process.
6. What role do templates play in SP3D project setup, and how can they be effectively utilized?
Templates in SP3D provide predefined settings, standards, and configurations for project setup. They ensure consistency across projects by standardizing elements like layer configurations, naming conventions, and component libraries. Effective utilization involves customizing templates to match company standards, enabling rapid project initiation, reducing setup time, and maintaining uniformity in design practices across different projects and teams.
7. Explain the use of isometric drawings in SP3D and the process of generating them from the 3D model.
Isometric drawings in SP3D represent 3D piping layouts in a two-dimensional format, facilitating easier interpretation and fabrication. To generate them, users select the desired piping routes and apply isometric templates. SP3D automatically extracts relevant data from the 3D model, including dimensions, components, and annotations. The software then formats this information into detailed isometric drawings, which are essential for construction and installation.
8. How does SP3D manage large-scale projects in terms of performance and data handling?
SP3D manages large-scale projects by utilizing robust data management systems like Intergraph’s SmartPlant Enterprise platform. It employs efficient data indexing, modular project structures, and distributed databases to handle extensive data volumes. Performance is optimized through hardware scalability, parallel processing, and network optimization, ensuring smooth operation and quick access to large datasets essential for complex, large-scale engineering projects.
9. Discuss the role of automation scripts in SP3D and provide an example of their application.
Automation scripts in SP3D streamline repetitive tasks, enhance accuracy, and save time. Using scripting languages like VBScript or Python, users can automate processes such as batch component placement, data extraction, or custom reporting. For example, a script can automatically generate a bill of materials (BOM) from the 3D model, ensuring consistency and reducing manual data entry errors, thereby increasing overall project efficiency.
10. What are the best practices for maintaining data integrity and version control in SP3D projects?
Best practices include using a centralized data management system like SmartPlant Foundation, enforcing strict access controls, and implementing consistent naming conventions. Regular backups, audit trails, and versioning protocols ensure that changes are tracked and reversible. Additionally, establishing clear workflows for data updates and collaboration minimizes conflicts and maintains data integrity, ensuring reliable and accurate project information throughout the design lifecycle.
Course Schedule
Jul, 2025 | Weekdays | Mon-Fri | Enquire Now |
Weekend | Sat-Sun | Enquire Now | |
Aug, 2025 | Weekdays | Mon-Fri | Enquire Now |
Weekend | Sat-Sun | Enquire Now |
Related Courses
Related Articles
Related Interview
- Piping Design and Drafting Interview Questions Answers
- Advanced Cloud Security Practitioner Interview Questions Answers
- AVEVA ERM Training Interview Questions Answers
- SAP Document Compliance (SDC) Training Interview Questions Answers
- SAP Master Data Governance on SAP S4 HANA Training Interview Questions Answers
Related FAQ's
- Instructor-led Live Online Interactive Training
- Project Based Customized Learning
- Fast Track Training Program
- Self-paced learning
- In one-on-one training, you have the flexibility to choose the days, timings, and duration according to your preferences.
- We create a personalized training calendar based on your chosen schedule.
- Complete Live Online Interactive Training of the Course
- After Training Recorded Videos
- Session-wise Learning Material and notes for lifetime
- Practical & Assignments exercises
- Global Course Completion Certificate
- 24x7 after Training Support
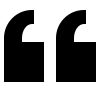