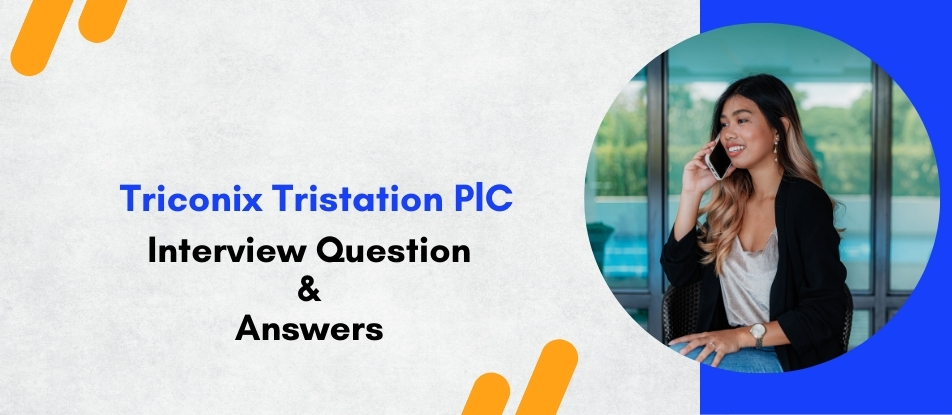
Triconex Tristation PLC Training provides comprehensive expertise in configuring and managing fault-tolerant safety systems. The course covers TMR architecture, Tristation 1131 software, logic programming, diagnostics, communication modules, and safety lifecycle management. Learners will develop practical skills in implementing and maintaining high-integrity systems compliant with IEC 61508/61511 standards. Designed for automation engineers, control system integrators, and safety professionals working in critical industrial environments such as energy, petrochemical, and manufacturing sectors.
Triconix Tristation PlC Training Interview Questions Answers - For Intermediate
1. What is the function of the I/O Bus in a Triconex PLC system?
The I/O Bus in a Triconex system connects the processor modules to the I/O modules across the backplane. It facilitates the transfer of input signals from the field to the processors and the output signals from processors to field devices. The I/O Bus is fully redundant, supporting fault tolerance and ensuring continuous data flow even in the case of partial bus failure.
2. What is meant by “system voting” in Triconex?
System voting is a fault-tolerant mechanism where the three processor modules in a TMR configuration independently process the same input data and logic. The outputs from each module are then compared, and a two-out-of-three majority vote determines the final output. This ensures error-free and safe output even if one processor malfunctions.
3. How is a fault in one processor handled by a Triconex TMR system?
If one processor in the TMR system fails, the remaining two continue processing and maintain correct operation using the majority vote. The system isolates the faulty processor and raises an alert, but operations remain unaffected. This design ensures high availability and no process downtime due to single module failure.
4. What is the purpose of the SOE (Sequence of Events) feature in Triconex?
The SOE feature records time-stamped digital input events with high accuracy, typically in milliseconds. It is used for post-event analysis, helping engineers to trace the exact sequence of events leading up to a fault or shutdown. This improves root cause analysis and safety investigations in critical systems.
5. How does Triconex ensure time synchronization across modules and systems?
Triconex systems use internal real-time clocks and can synchronize time across modules using a master time source. This is especially important for SOE data, alarm logging, and diagnostics. Time synchronization can also be done using NTP (Network Time Protocol) from a plant-wide time server to ensure consistency.
6. What is the role of the system status indicators on Triconex modules?
Each module in the Triconex system includes LED indicators that display status information such as power, health, activity, fault, and communication. These indicators help technicians quickly identify operational issues, faulty modules, or synchronization errors without needing to connect a programming tool.
7. How are firmware updates managed in a Triconex system?
Firmware updates in Triconex systems are performed through Tristation 1131, usually during planned maintenance windows. The update process involves stopping the system or upgrading individual modules one at a time (if supported). The system ensures that updates are verified and validated before deployment to avoid operational disruptions.
8. What is the significance of configuration files in Tristation 1131?
Configuration files in Tristation 1131 define the I/O layout, processor settings, communication protocols, and logic parameters. These files are essential for system deployment and troubleshooting. Backing up and documenting these configurations is critical for system recovery and disaster preparedness.
9. Can Triconex systems support remote diagnostics and monitoring?
Yes, Triconex systems support remote diagnostics via Ethernet or serial communications using Tristation 1131. Engineers can monitor processor health, I/O status, and system diagnostics remotely, reducing the need for on-site interventions and improving response times for troubleshooting.
10. What is the purpose of the Triconex Safety Integrity Level (SIL) certification?
The SIL certification verifies that the Triconex system meets rigorous safety standards defined by IEC 61508. Triconex is typically certified up to SIL 3, which is suitable for high-risk applications. SIL certification ensures that the system performs its safety functions reliably even under defined fault conditions.
11. How is the cold restart behavior of a Triconex system managed?
During a cold restart, the Triconex system performs a full hardware and software initialization. It reloads the last saved logic and configuration, re-synchronizes processors, and checks for hardware faults before resuming operations. The cold start ensures the system comes back in a known and safe state.
12. What redundancy options are available for communication in Triconex systems?
Triconex offers redundant communication paths using dual communication modules or ports. If one path fails, the system automatically switches to the backup path to maintain connectivity. This redundancy is critical for data exchange with SCADA or DCS systems and ensures uninterrupted monitoring and control.
13. How does Triconex handle analog signal processing?
Analog signals are received through Analog Input (AI) modules, which digitize the signals and apply filtering or scaling if needed. The data is then voted upon (in TMR systems) to ensure accuracy. Analog Output (AO) modules send processed signals to field devices like actuators or control valves.
14. Can online edits be made in Triconex logic, and what are the safety implications?
Yes, Triconex allows online logic edits using Tristation 1131. These edits undergo strict validation and safety checks before being downloaded to the system. Redundancy checks and voting ensure that no unsafe changes affect system operation. However, such edits should always follow change management protocols to avoid risk.
15. What is the function of the “force” command in Tristation 1131?
The "force" command allows engineers to override the actual value of an input or output for testing or diagnostic purposes. It’s commonly used during commissioning or troubleshooting. Forced values are clearly flagged in the system, and safeguards are in place to prevent unintentional changes in live systems.
Triconix Tristation PlC Training Interview Questions Answers - For Advanced
1. How does the Triconex system handle I/O diagnostics, and what happens when a fault is detected?
Triconex systems are designed with advanced I/O diagnostics to ensure system integrity and early detection of field device issues. Each I/O module performs continuous built-in self-tests to monitor signal quality, connection status, and channel health. For example, Analog Input modules check for open or short circuits, overvoltage, and out-of-range values, while Digital Input modules verify state changes and wiring integrity. When a fault is detected, the system generates a diagnostic message visible on Tristation 1131 and triggers LED indicators on the affected module. If configured, the system can automatically isolate the faulty channel or switch to redundant I/O paths, ensuring continuous process control. These diagnostics not only improve system reliability but also reduce troubleshooting time, supporting predictive maintenance strategies in high-stakes industrial environments.
2. In what ways does Triconex support scalability and system expansion in large-scale deployments?
Triconex systems are inherently modular and scalable, making them suitable for small safety applications as well as large-scale industrial complexes. Multiple Triconex racks can be connected through fiber-optic or Ethernet-based peer-to-peer communication for distributed control. Each rack can be configured with redundant power supplies, communication modules, and a wide variety of I/O modules. The software environment, Tristation 1131, supports centralized configuration and monitoring, even across distributed systems. Additionally, users can implement remote I/O stations, reduce wiring complexity, and integrate various communication protocols to connect with enterprise or cloud-based systems. This modular scalability allows organizations to start small and expand seamlessly as operational needs grow.
3. Explain the importance and implementation of redundancy in Triconex communication modules.
Redundancy in communication modules is critical to maintaining consistent connectivity between the Triconex controller and external systems such as SCADA, DCS, and HMIs. Triconex offers dual redundant Network Communication Modules (NCMs) and Gateway Communication Modules (GCMs) that operate in parallel. If one module fails, the other takes over without data loss or communication interruption. These modules also support redundant network paths (e.g., dual Ethernet) and automatically switch to the standby path when needed. This failover mechanism ensures real-time monitoring and control data is always available, supporting high availability requirements in safety-critical systems where communication loss can trigger unintended shutdowns or delayed responses.
4. How does Triconex address electromagnetic compatibility (EMC) and environmental noise in critical facilities?
Triconex hardware is designed to meet stringent EMC standards, including IEC 61000 and ISA guidelines for electromagnetic immunity and emissions. The modules feature shielding, filtered connectors, and noise-isolating circuits to prevent external electromagnetic interference from corrupting signals or causing logic faults. Grounding and bonding practices are essential during installation, and the system architecture ensures differential signal handling in analog circuits, reducing susceptibility to noise. The TMR system also acts as a noise filter, since corrupted data from one processor path can be outvoted by the other two. These design features make Triconex a robust choice in environments with high EMI, such as substations or heavy industrial plants.
5. How does the Triconex system support long-term data retention and archival for regulatory compliance?
Triconex systems can store event logs, SOE data, and diagnostics locally or export them to external systems for long-term archival. Through integration with historian software like OSIsoft PI, GE Proficy, or Schneider’s EcoStruxure, users can automate data capture and retention over months or years. The communication modules support OPC UA and Modbus TCP/IP, which can be used to send data to plant-level databases. Tristation 1131 also provides export functionality in CSV or proprietary formats. These capabilities support compliance with regulatory frameworks such as OSHA, EPA, and IEC/ISA standards, where maintaining historical safety data is essential for audits, reporting, and continuous improvement.
6. What is the process for implementing a Safety Instrumented Function (SIF) using a Triconex PLC?
Implementing a SIF with Triconex begins with defining the process hazard and required safety response based on a PHA or HAZOP study. After determining the Safety Integrity Level (SIL) requirement, engineers develop the safety logic in Tristation 1131 using certified function blocks and programming standards. Redundant I/O modules are used to collect data from sensors and send signals to actuators, with all paths subject to diagnostics and voting. Once programmed, the logic undergoes verification and validation testing, including FAT and SAT. The entire SIF must be documented, version-controlled, and reviewed for compliance with IEC 61511 standards. Periodic proof testing and audit trails ensure ongoing reliability.
7. How is fault tolerance achieved in Triconex power supply systems?
Fault tolerance in power supply systems is implemented through dual redundant power supply units (PSUs) in each chassis. These PSUs operate in a load-sharing configuration, so if one fails, the other takes over instantly. Power supplies are hot-swappable and monitored continuously through diagnostic feedback. Additionally, Triconex supports multiple power sources, such as AC and DC, which can be configured to maintain backup operation during utility failure or UPS maintenance. Alarms and system logs are generated in the event of power fluctuations or failures, allowing proactive intervention. This redundancy ensures that even the most critical safety applications maintain uninterrupted power.
8. What is the role of the System Access Controller (SAC) in a Triconex environment?
The System Access Controller (SAC) is a security feature that controls physical and logical access to the Triconex system. It manages authentication, user roles, and login privileges to ensure that only authorized personnel can make logic changes, perform diagnostics, or access system configurations. The SAC enforces password policies and can log user activity for auditing purposes. In high-security environments, it works in conjunction with access management systems, domain authentication, or VPNs to enforce cybersecurity protocols. This component is crucial for preventing unauthorized or accidental changes that could compromise system safety.
9. Explain the procedure and precautions for firmware updates in Triconex controllers.
Firmware updates in Triconex are tightly controlled due to the system’s role in safety-critical operations. Updates are typically performed during scheduled maintenance windows and require a validated firmware image from Schneider Electric. The procedure begins with a full system backup, followed by verification of hardware compatibility and system health. The firmware is uploaded using Tristation 1131 or via specialized maintenance tools. During the update, one processor module is updated at a time while the others continue operation, ensuring fault tolerance. After installation, the system performs checksums and self-tests to confirm integrity. A rollback option is available in case of failure. All updates must be documented under change management policies to ensure traceability and compliance.
10. How can a Triconex system be used in High-Integrity Pressure Protection Systems (HIPPS)?
HIPPS applications demand ultra-reliable safety systems capable of shutting off flow in milliseconds to prevent overpressure scenarios. Triconex is ideal for HIPPS because it meets SIL 3 standards and supports ultra-fast input scanning and output response. Redundant pressure transmitters feed data into AI modules, and logic developed in Tristation 1131 performs condition checks and initiates shutdown if pressure thresholds are exceeded. The TMR architecture ensures no single point of failure affects system operation. Valve actuators are controlled through DO modules, often configured with redundant wiring and diagnostics. HIPPS implementations with Triconex are commonly found in offshore platforms and gas pipelines where containment is critical.
11. How does Triconex support fail-safe design principles in safety instrumented systems?
Fail-safe design in Triconex involves configuring the system so that any detected failure leads to a safe state, such as shutting down a process or activating an alarm. This is achieved through hardware and software strategies. On the hardware side, DO modules default to safe positions (e.g., de-energized relays) when faults are detected. On the software side, logic routines include watchdog timers, fault detectors, and failover conditions. Redundant sensors and final elements are configured with diagnostic coverage to ensure that failure leads to a known safe condition. This philosophy is fundamental to achieving compliance with IEC 61508/61511 standards and ensuring personnel and equipment safety.
12. How are time-critical responses ensured in Triconex, particularly for fast-acting safety functions?
Triconex systems achieve deterministic timing through real-time operating systems and prioritized scanning routines. Input scans, logic execution, and output updates occur in tightly controlled cycles, often as low as 10 milliseconds. For fast-acting functions, such as gas detection or emergency trips, dedicated high-speed input/output modules are used. These modules are hardwired for minimal latency and directly linked to the processor. Additionally, voting mechanisms and diagnostics are streamlined in these cases to prioritize speed over diagnostics depth. Real-time task scheduling and watchdog monitoring ensure that any delays or missed cycles are caught immediately, making the system reliable for rapid safety interventions.
13. What are some common challenges in implementing Triconex systems and how can they be mitigated?
Common challenges include managing system complexity, ensuring proper documentation, integrating with diverse protocols, and meeting compliance requirements. These can be mitigated by thorough planning during the system design phase, including clear specification of safety functions, redundancy levels, and testing procedures. Using certified function blocks and standard templates in Tristation 1131 can reduce programming errors. Integration challenges can be addressed by choosing compatible communication modules and simulating interfaces before commissioning. Continuous training, version control, and change management practices further ensure smooth operation and maintain compliance with safety and cybersecurity standards.
14. How does Triconex support integration with digital twins and virtual commissioning platforms?
Triconex can be integrated with digital twins through simulation environments that emulate real-world conditions. Using Tristation 1131’s offline simulation feature, logic and I/O responses can be tested without physical hardware. For more advanced digital twin use cases, Triconex can interface with platforms like AVEVA, SimSci, or third-party simulation tools using OPC UA, Modbus, or custom APIs. This enables virtual commissioning, where the control system’s behavior is tested against a dynamic model of the plant. Benefits include early detection of logic flaws, reduced commissioning time, and safer plant startup. This approach aligns with Industry 4.0 objectives and predictive maintenance strategies.
15. What future trends are expected in Triconex and safety system technologies?
Future trends include increased integration with cloud-based analytics, AI-driven diagnostics, and edge computing. Schneider Electric is already incorporating capabilities such as predictive maintenance and digital twin support into its safety platforms. Triconex systems are expected to evolve with enhanced cybersecurity features, including blockchain-based audit trails, machine learning for anomaly detection, and real-time threat response. Additionally, interfaces with IIoT devices and mobile-friendly diagnostics are gaining traction. As plants move toward autonomous operations, the role of safety systems like Triconex will expand from passive protection to intelligent, proactive systems that guide operational decisions.
Course Schedule
Apr, 2025 | Weekdays | Mon-Fri | Enquire Now |
Weekend | Sat-Sun | Enquire Now | |
May, 2025 | Weekdays | Mon-Fri | Enquire Now |
Weekend | Sat-Sun | Enquire Now |
Related Courses
Related Articles
Related Interview
- Salesforce Billing Interview Questions Answers
- AWS Solution Architect Associate Level Interview Questions Answers
- SAP Build Work Zone Training Interview Questions Answers
- MB-800: Microsoft Dynamics 365 Business Central Functional Consultant Interview Questions
- Kronos UKG Workforce Management (Dimensions) Training Interview Questions Answers
Related FAQ's
- Instructor-led Live Online Interactive Training
- Project Based Customized Learning
- Fast Track Training Program
- Self-paced learning
- In one-on-one training, you have the flexibility to choose the days, timings, and duration according to your preferences.
- We create a personalized training calendar based on your chosen schedule.
- Complete Live Online Interactive Training of the Course
- After Training Recorded Videos
- Session-wise Learning Material and notes for lifetime
- Practical & Assignments exercises
- Global Course Completion Certificate
- 24x7 after Training Support
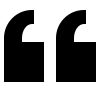